Sand Casting
Bearings and Bushings for the Future: Precision and Customization: Our company, in bearing engineering with decades of experience, designs and develops high-precision self-lubricating bronze bearings & plain bushes. We offer a wide array of sliding bearings tailored to meet specific needs. Renowned for our expertise in custom bronze bushing and slide plate solutions, we provide an expansive selection of bushing metal alloys. Contact us today to benefit from unparalleled services at competitive prices.
Sand Casting
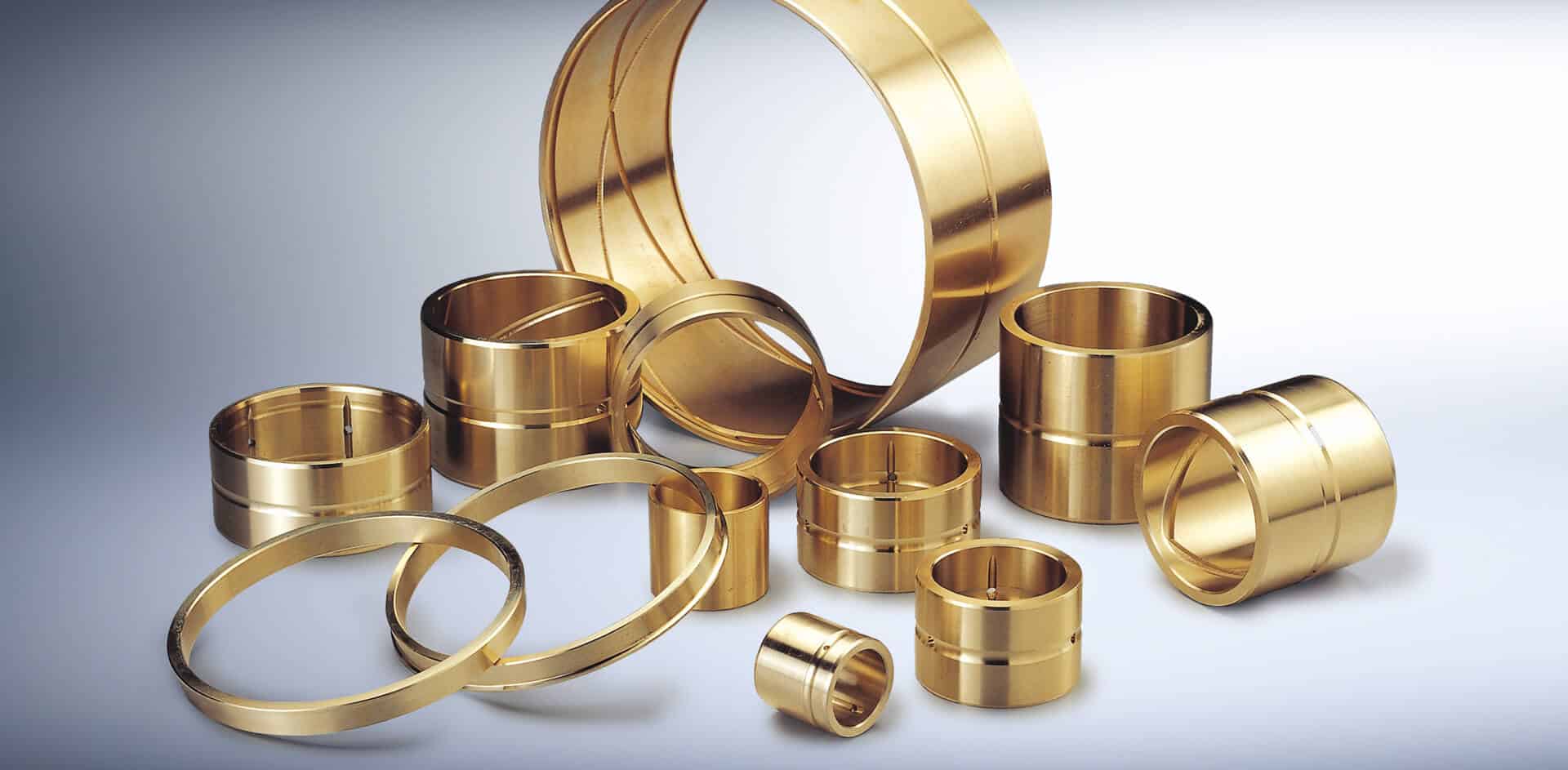
Start Sourcing The Bronze Bearing Today
Give us a call to schedule your purchasing oder for the bronze bushing.
SAND CASTING SERVICES
Our Slide Bearing & Bushing Products: Don’t See What You’re Looking For? Contact Us. If We Don’t Have It In Our Product Portfolio, We Can Review The Application And Propose A Custom Solution.
Custom Size Bronze Bearings: Overview of Sand Casting
Introduction to Sand Casting Sand casting is a fundamental metal casting process where sand serves as the mold material. The process begins by packing sand around a model, then removing it to reveal a cavity that matches the desired shape of the cast. Molten metal is poured into this cavity, and once it solidifies, the mold is broken apart to extract the casting. For internal features or undercuts, sand cores are employed.
Benefits and Applications The versatility of sand casting is apparent, as it can produce a wide range of shapes and sizes suitable for various industries. This method is cost-effective due to the minimal equipment requirements for small batch production and the economical nature of sand. It supports various ferrous and non-ferrous metals, typically requiring a minimum wall thickness of 3.8 mm for aluminum castings.
Specific Techniques and Alloys Warner Brothers Foundry Company offers rapid turnaround times for their sand casting services, which helps keep your production schedules on track. In our foundry, we use well-known alloys such as aluminum bronze, tin bronze, and manganese bronze.
No-Bake Sand Molding For more complex designs, the no-bake sand molding process employs a chemical binder to maintain the sand’s shape, allowing for the production of intricate and high-quality castings. This method is particularly beneficial for large parts or designs with deep pockets.
When to Choose Sand Casting Sand casting is ideal for producing large parts, parts with complex manufacturing processes, or when only a medium quantity is needed. Industries such as automotive, architecture, and food and beverage frequently use this process for items like brake drums, sculptures, and housings.
Conclusion Choosing the right sand casting process and alloy can significantly impact the quality and functionality of the final product. Warner Brothers Foundry Company excels in providing customized solutions and expert guidance in selecting the best alloy for your project, ensuring your sand casting needs are met with precision and efficiency.
Sand Casting Production
This process involves making a pattern in the shape of the desired part. The pattern is then placed in a box called a jar and packed with sand. A binding agent is added to the sand to help it harden. The mold is cured and the pattern is removed.
Introduction to Sand Mold Casting
Basic Components:
Sand mold casting primarily uses foundry sand and a binder to shape and solidify the mold. The most common type of sand used is siliceous sand. However, for higher temperature applications, special sands like zircon, chromite, and corundum are preferred due to their superior heat resistance.
Binders:
To ensure the sand mold retains its shape during the casting and solidification of metal, binders such as clay are mixed with the sand. Other binders can include various oils, water-soluble silicates, phosphates, and synthetic resins, depending on the specific requirements of the casting.
Types of Sand Molds:
Sand molds can be categorized based on the binder used and how they gain strength:
Clay Wet Sand Mold: Uses a mixture of clay and water as the binder. The mold is formed and used while still wet, common in many traditional casting processes.
Clay Dry Sand Mold: Similar to the wet sand mold but with slightly more moisture. After forming, these molds are baked to harden, making them suitable for heavier or more intricate castings.
Chemically Hardened Sand Mold: Utilizes synthetic resins or water glass as binders that are activated by hardeners to solidify the mold. This method is versatile, allowing for complex shapes and high-quality finishes.
Advantages of Clay Wet Sand Casting:
Economical and abundant materials.
Reusable sand after treatment.
Short mold preparation times and high work efficiency.
Ability to withstand slight deformations without breaking.
Disadvantages:
Requires heavy-duty mixing equipment to properly coat the sand grains with clay.
High labor and skill required for manual molding due to the sand’s high strength.
Molds are less rigid, which can compromise the dimensional accuracy of the casting.
Susceptible to defects like sand flushing, inclusions, and porosity.
Conclusion:
Sand casting is a flexible and cost-effective method suitable for a wide range of metal castings, supported by its long history and adaptability to different production scales. Whether using traditional clay methods or modern chemical binders, the technique remains foundational in the casting industry, particularly for large or complex components.
Technical Data:
Material | CuZn25AI5Mn4Fe3 | CuSn5Pb5Zn5 | CuAI10Ni5Fe5 | CuSn12 | CuZn25AI5Mn4Fe3 |
Density | 8 | 8.9 | 7.8 | 8.9 | 8 |
Hardness | ≥210 | ≥70 | ≥150 | ≥75 | ≥235 |
Tensile strength | ≥750 | ≥250 | ≥500 | ≥270 | ≥800 |
Yield strength | ≥450 | ≥90 | ≥260 | ≥150 | ≥450 |
Elongation | ≥12 | ≥13 | ≥10 | ≥5 | ≥8 |
Coefficient linear expansion | 1.9×10-5/℃ | 1.8×10-5/℃ | 1.6×10-5/℃ | 1.8×10-5/℃ | 1.9×10-5/℃ |
Max. Temp. | -40~+300℃ | -40~+400℃ | -40~+400℃ | -40~+400℃ | -40~+300℃ |
Max. dynamic load | 100 | 60 | 50 | 70 | 120 |
Max. speed(Dry) | 15 | 10 | 20 | 10 | 15 |
N/mm²*m/s(Lubrication) | 200 | 60 | 60 | 80 | 200 |
Compression deformation | < 0.01 mm | < 0.05mm | < 0.04mm | < 0.05mm | < 0.005mm |
Typical Applications
Solutions For Every Industry
Searching for Dependable Bushing Solutions? viiplus Has What You Need.
Design Guides, Materials
Bushing design, Comprehensive design manuals covering a range of self-lubricating materials used in all of viiplus’s manufacturing processes.
Technical Guides
Manufacturing On Demand, Technical Guides For Machining Design. Discover the latest in metal alloys, materials, and design tips for manufacturing custom machined and self-lubricating bearing parts.
Get Instant Quote
To receive your instant quote, simply upload your drawing file and choose your production process & bushing material.
Prototyping, Place Order
After you place your order, we will start the production process. You will receive updates when your order has completed production and is ready to be dispatched.
Receive Your custom Parts
We provide precision-inspected high-quality parts, packing lists and documents, and delivery tracking.