Oil Groove Bushings, Flanged Aluminum Bronze Bushing with Grease Grooves, Custom Parts
Beautifully crafted leather products.
Oil Groove Bushings: Premium Performance Bronze Bushings with Integrated Oil Grooves. Cost-Efficiency and Reduced Downtime. Services include Grease Groove Design and Expedited Delivery. Flanged aluminum bronze bushings with grease grooves present a compelling solution for businesses and industries seeking robust, efficient, and long-lasting bearings. These unique bushings are particularly suitable for high-load, low-speed applications, including but not limited to construction equipment, gearboxes, pumps, and conveyors. The design and the material selection of these bushings contribute significantly to their efficacy. Understanding these features will help illustrate the value and benefits of choosing these specialized bushings. Applications: Bronze bushings with oil groove designs find applications across a wide range of industries, owing to their versatility, durability, and cost-effectiveness. They are commonly used in applications such as construction machinery, agricultural equipment, pumps, turbines, gearboxes, and conveyors. Anywhere that demands a robust, reliable, and efficient bearing solution, you are likely to find bronze bushings with oil grooves.
Bronze Toggle Bushing, cutting lubrication grooves in virtually any pattern
We offer our valuable clients a premium quality Bronze Toggle Bushing in bronze metal, which is manufactured using the latest equipment coupled with technically qualified personnel in the industry. Our in-house production capacity enables us to manufacture Bronze Bushes in large quantities, so that we can offer quality products at very competitive prices. We manufacture Toggle Bushes for injection molding machines. Injection Molding Machines Bronze Bearing Request A Quote!
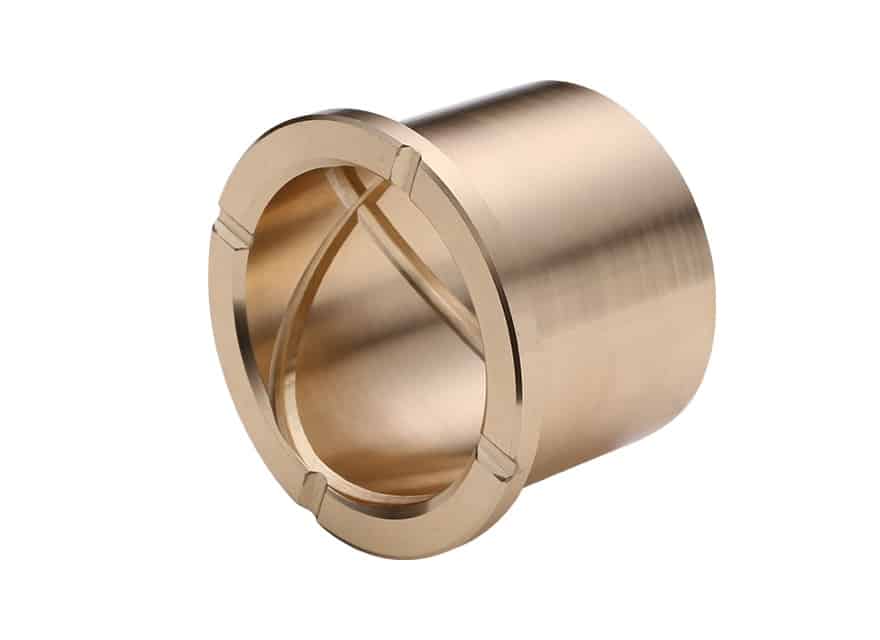
Product Quality Index
Energy Generation
Oil-Grease, Oil & Grease Bushing, Quality BushingGrease Groove Design, Injection Moulding Machine Parts
Bronze Bushing with Grease Groove
Oil Groove Bearings & Bronze Bushings
Cast Bronze Graphite Slide Bushes With Graphite Plug. Bronze Bushings With Oil Grooves, Bronze sleeve bushings or bronze bearings are hard and strong, in contrast to brass bushings which are softer and more prone to deformation. Contact our bronze bearings experts for assistance. Main applications: Solid Bronze bushings are designed for oscillating movements in both rotational and axial directions. They are not suitable for rotating movements at medium or high speeds. Grooved Cast Bronze Bushings Manufacturing: We specialize in cutting lubrication grooves in various patterns such as “8” Groove and “11” Groove. Other common groove patterns include figure eight, double figure eight, loop, double loop, circular, wick, or straight. Examples of applications include construction machinery, transport equipment, and off-shore equipment.
Design Of Oil Groove Bronze Bearings: The Double Loop And Double Figure Eight Designs Are Specifically Recommended For Use With Grease Lubrication.
Flanged Aluminum Bronze Bushing with Grease Grooves, bronze bushing with grease groove
Share your wedding moments with your guests
earth moving bushings
Oil Grooved Bush, Flange bushing, bronze bushing with grease groove
We manufactures a wide range of injection moulding machines bronze bushing. We are among the select few companies in India that offer both Hydraulic and Toggle Injection Moulding Machines. We have built a great network and are finding more growth in the market with our latest flagship product self-lubricating bronze bushing bearing series for injection molding machines, which is the latest in its competition. Not only are we competitive on price, but it is a self-lubricating bearing product with unmatched performance, which offers minimal downtime and failure rates. Brass bearings and bushes with figure of 8 oil grooves are engineered to enhance lubrication and reduce wear under various operating conditions. Customization and precision manufacturing are key to ensuring that these components perform reliably and efficiently in their intended applications.
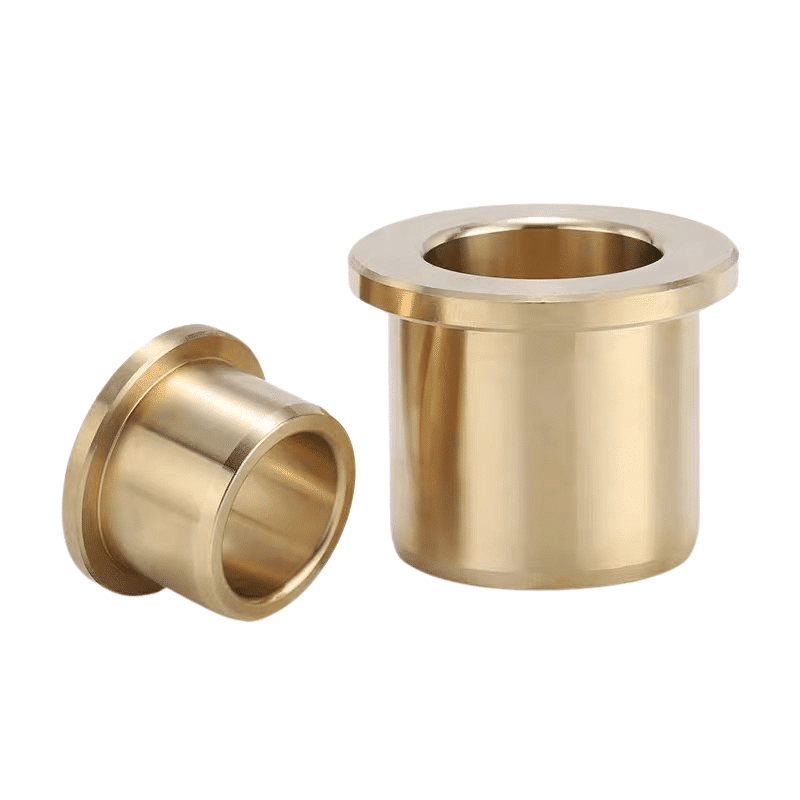
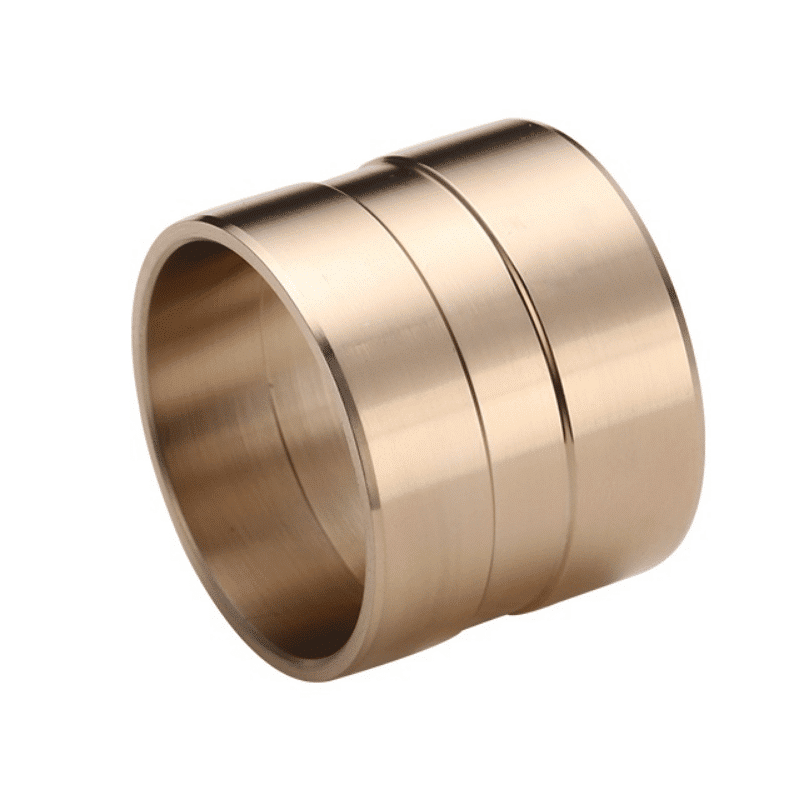
Product Quality Index
Energy Generation
Self-lubricating Bronze Toggle Bushings
oil groove bushing sizes Flanged aluminum bronze bushings with grease grooves are a testament to innovative engineering and material science. These components offer a hard-wearing, efficient solution for various industrial applications, especially in environments where high-load capacity and longevity are paramount. With the added advantages of customizability and self-lubricating options, they present an exceptional choice for businesses seeking to optimize their equipment performance.
The material specification for SAE 660 cast bronze sleeve bearings is defined by the continuous cast bronze alloy C93200, as per ASTM B505 standards. This material is also known as High Leaded Tin Bronze.
Material Specification: SAE 660/C93200
Chemical Composition: This alloy is primarily composed of 83% Copper (Cu), 7% Tin (Sn), 7% Lead (Pb), and 3% Zinc (Zn).
Characteristics: SAE 660 bronze is recognized for its excellent hardness, strength, resistance to wear, and superior machinability. It serves as a versatile leaded tin bronze material for bearings and bushings.
Usage: Due to its outstanding wear resistance, easy machinability, and self-lubricating features, SAE 660 is extensively utilized across various sectors. It is ideal for automotive components, fasteners, industrial bushings, machinery parts, main spindle bearings, and more.
SAE 660 cast bronze sleeve bearings are engineered to perform effectively at temperatures up to 450°F, making them suitable for a wide range of general bearing applications. Depending on the specific use case, additional lubrication might be required. These bearings can withstand a maximum pressure of 4,000 psi, a maximum velocity of 750, and have a maximum PV value of 75,000. The continuous casting method guarantees a consistent grain structure within the bearing, thereby boosting its functionality and longevity.
SAE 660 cast bronze sleeve bearings, crafted from C93200 continuous cast bronze, are engineered for exceptional quality and performance. The continuous casting technique ensures a consistent bronze structure throughout the bearing, eliminating porosity and hard particle inclusions typical of other casting methods. These bearings are available in an extensive array of sizes, with more than 900 standard dimensions readily available in stock. They offer customization options like resizing, oil grooving, or graphite application to meet specific needs.
The bearings are made from a leaded tin bronze alloy known for its robustness, strength, wear resistance, and superior machinability. The inner diameter tolerances are precise, with an example being +.001″ to -.001″. Similarly, the outer diameter tolerances are meticulously maintained, one example being +.002″ to +.003″.
For optimal lubrication, the design of oil and grease grooves is crucial, particularly in applications with oscillatory movements. These grooves ensure even distribution of lubrication, minimizing friction and wear, and thus prolonging the lifespan of the bearing. A notable design is the Figure 8 groove, which enhances lubrication and reduces friction during operation.
SAE 660 bronze bearings are ideal for various applications, such as in the automotive, aerospace, and power generation sectors, valued for their high load capacity, superior wear resistance, and self-lubricating features. Custom manufacturing options are available, including the grooved Figure 8 design, to provide industry-specific solutions that ensure reliability and durability.
In essence, SAE 660 cast bronze sleeve bearings are a blend of performance and cost-efficiency, offering desirable material properties and customizable features that cater to a broad spectrum of industrial applications.
The Superior Performance of Graphite and Bronze Bushings with Oil Grooves: Reducing Costs and Downtime
In today’s competitive industrial landscape, finding cost-effective, efficient solutions is crucial. Graphite and bronze bushings with oil grooves are among the most effective, providing superior performance in hundreds of applications and presenting an exceptional replacement option for traditional carbon bearings.
Incredible Productivity Boost
Utilizing graphite and bronze bushings with oil grooves allows for increased productivity. As the oil grooves distribute lubrication evenly across the bearing surface, the reduction in friction significantly enhances the efficiency of the machinery. This increase in efficiency leads to heightened productivity, allowing companies to achieve more within shorter time frames.
Custom Design and Engineering Support
These bushings are available with extensive customization options, offering designs tailored to a variety of applications. Whether it’s specific dimensional requirements or specific performance characteristics, companies can design their bushings to best suit their needs. Coupled with comprehensive engineering support, businesses can ensure they have the optimal bushing design for their application.
Short Lead Times
Despite their customizability, these bushings also offer short lead times. With swift manufacturing processes and efficient supply chains, companies can get their customized graphite and bronze bushings in a timely manner. This not only helps to maintain steady operations but also to manage unexpected maintenance and replacement tasks efficiently.
Maintenance Reduction with Oil Groove Design
An essential feature of these bushings is the design of oil grooves. These grooves serve as reservoirs that hold and evenly distribute the lubricating oil when the bushing is in operation. This design helps to reduce maintenance to a minimum, as the consistent lubrication significantly decreases wear and tear, extending the lifespan of both the bushing and the mating shaft.
Good Quality and Reduced Costs
Graphite and bronze bushings with oil grooves are of high quality, crafted to withstand heavy-duty usage in various industrial applications. Their durability and low-maintenance design help companies reduce costs associated with frequent replacements and machine downtimes. In the long run, investing in these bushings can lead to significant savings.
Conclusion
By providing a range of services from custom design to engineering support, and boasting short lead times, graphite and bronze bushings with oil grooves offer a comprehensive solution for businesses. Their potential to increase productivity, coupled with their quality and cost-reducing benefits, make these bushings a compelling choice for those looking to optimize their industrial processes.
Oil Groove Bushings: Understanding their Function and Benefits
Oil groove bushings, also known as oil-impregnated bushings, are an essential component in many mechanical systems and equipment. These bushings are designed with oil grooves, which are filled with oil to provide lubrication and reduce friction between the bushing and shaft. In this article, we will discuss the function and benefits of oil groove bushings, and why they are important for many applications.
- Function
Oil groove bushings are designed to support rotating or sliding shafts and to reduce friction and wear between the shaft and the bushing. The oil grooves in the bushing are filled with oil, which provides lubrication to the shaft and helps to reduce friction and wear. This helps to extend the life of the equipment and improve its performance.
- Material Selection
Oil groove bushings are available in a variety of materials, including bronze, steel, and plastic, and the selection of the right material depends on the specific requirements of the application. Bronze bushings are a good choice for heavy-duty applications, as they are strong and durable. Steel bushings are a good choice for applications that require high strength and stiffness, and plastic bushings are a good choice for applications where weight reduction is a priority.
- Benefits
Oil groove bushings provide many benefits for mechanical systems and equipment, including:
- Improved Lubrication: The oil grooves in the bushing provide a continuous supply of oil to the shaft, which helps to reduce friction and wear, and improve the performance of the equipment.
- Extended Equipment Life: By reducing friction and wear, oil groove bushings help to extend the life of the equipment and reduce the need for maintenance and repairs.
- Reduced Noise: The oil grooves in the bushing help to reduce friction and noise, making the equipment quieter and more pleasant to use.
- Cost-Effective: Oil groove bushings are a cost-effective solution for many applications, as they help to reduce maintenance costs and extend the life of the equipment.
In conclusion, oil groove bushings are an essential component in many mechanical systems and equipment, and they provide many benefits, including improved lubrication, extended equipment life, reduced noise, and cost-effectiveness. When selecting an oil groove bushing, it is important to consider the specific requirements of the application, such as load capacity, speed, and operating temperature, and to choose a material that meets these requirements, ensuring reliable and long-lasting performance.
Oil Groove Grease Bronze Bearing
Oil groove cast bronze is a type of bronze alloy that has been cast with grooves or channels designed to distribute lubricating oil throughout the surface of the bearing. This type of bronze is commonly used in manufacturing bearings and bushings because the addition of the grooves helps to improve lubrication and reduce friction, thereby increasing the lifespan of the bearing.
Oil groove cast bronze bearings can be made from a variety of different bronze alloys, including those that contain copper (Cu), tin (Sn), lead (Pb), aluminum (Al), zinc (Zn), iron (Fe), and manganese (Mn). The choice of alloy will depend on the specific application requirements, such as corrosion resistance, wear resistance, and strength.
Oil groove cast bronze bearings are commonly used in heavy machinery, industrial equipment, and automotive applications where high load-bearing capacity and durability are required. They are often used in applications where the bearing operates at low speeds and high loads, such as in gearboxes, camshafts, and connecting rods.
600S2 CuSn12 bronze groove bearing Bushings
600S2 CuSn12 is a type of bronze alloy that contains copper (Cu) and tin (Sn). This type of bronze is commonly used in manufacturing bearings and bushings because it has good corrosion resistance and excellent wear resistance.
A groove bearing bushing is a type of bearing that has a groove or channel cut into the surface of the bearing. This groove helps to distribute lubricant and prevent the bearing from overheating or wearing down too quickly.
So, a 600S2 CuSn12 bronze groove bearing bushing is a type of bushing made from the 600S2 bronze alloy and contains a groove or channel to distribute the lubricant. This type of bushing would be suitable for applications where good corrosion resistance and wear resistance are required, and where the addition of a groove would help to improve the lubrication of the bearing.
600S4 CuSn10Pb10 is a type of bronze alloy that contains copper (Cu), tin (Sn), and lead (Pb). This type of bronze is commonly used in manufacturing bearings and bushings because it has good corrosion resistance, excellent wear resistance, and good machinability.
A groove bearing bushing is a type of bearing that has a groove or channel cut into the surface of the bearing. This groove helps to distribute lubricant and prevent the bearing from overheating or wearing down too quickly.
So, a 600S4 CuSn10Pb10 bronze groove bearing bushing is a type of bushing made from the 600S4 bronze alloy and contains a groove or channel to distribute the lubricant. This type of bushing would be suitable for applications where good corrosion resistance, wear resistance, and machinability are required, and where the addition of a groove would help to improve the lubrication of the bearing. However, it’s important to note that lead is a toxic substance and can have negative environmental and health impacts, so alternatives to lead-containing alloys may be preferred in certain applications.
600S5 CuZn25AI5 BRONZE GREASE BEARINGS
Available
Cylindrical bushes
Thrust washers
Flange bushes
supplied by customer order, the tolerance is according to JDB standard dimension.
600S5 CuZn25AI5 is a type of bronze alloy that contains copper (Cu), zinc (Zn), and aluminum (Al). This type of bronze is commonly used in manufacturing bearings and bushings because it has good corrosion resistance, high strength, and good wear resistance.
Grease bearings are a type of bearing that uses grease as a lubricant. Grease is a semi-solid lubricant that is made by mixing oil with a thickener. Grease lubrication can be beneficial because it can provide longer lubrication intervals, reduce friction and wear, and protect against corrosion and contamination.
So, a 600S5 CuZn25AI5 bronze grease bearing is a type of bearing made from the 600S5 bronze alloy and lubricated with grease. This type of bearing would be suitable for applications where good corrosion resistance, high strength, and good wear resistance are required, and where grease lubrication would be beneficial for improving the performance and lifespan of the bearing.
“600 Strong” is not a specific type of bronze alloy, so I assume you are referring to a bronze alloy that has been marketed or labeled as “600 Strong”.
ZCuZn25AI6Fe3Mn3 is a type of bronze alloy that contains zinc (Zn), copper (Cu), aluminum (Al), iron (Fe), and manganese (Mn). This type of bronze is commonly used in manufacturing bearings, gears, and other high-stress components because it has excellent strength, wear resistance, and corrosion resistance.
So, a “600 Strong” cast bronze ZCuZn25AI6Fe3Mn3 would be a type of cast bronze alloy that contains the elements listed above and is marketed or labeled as having exceptional strength properties. This type of bronze would be suitable for applications where high strength, wear resistance, and corrosion resistance are required, such as in heavy machinery or industrial equipment. However, it’s important to note that the performance of a specific alloy will depend on factors such as the manufacturing process, casting quality, and application conditions, so it’s always important to consult with a materials expert to select the most appropriate material for a specific application.
Oil Groove Types: Understanding the Different Options Available
Oil groove bushings, also known as oil-impregnated bushings, are an essential component in many mechanical systems and equipment. These bushings are designed with oil grooves, which are filled with oil to provide lubrication and reduce friction between the bushing and shaft. In this article, we will discuss the different types of oil grooves available and their applications.
- Continuous Oil Groove
The continuous oil groove is a type of oil groove that runs around the circumference of the bushing. This type of oil groove provides a continuous supply of oil to the shaft, which helps to reduce friction and wear. Continuous oil grooves are ideal for applications that require a high level of lubrication, such as high-speed or heavy-load applications.
- Interrupted Oil Groove
The interrupted oil groove is a type of oil groove that is interrupted or broken, at certain points along the circumference of the bushing. This type of oil groove provides a more controlled and consistent supply of oil to the shaft, which helps to reduce friction and wear. Interrupted oil grooves are ideal for applications that require moderate levels of lubrication, such as medium-speed or medium-load applications.
- Multiple Oil Grooves
The multiple oil groove is a type of oil groove that consists of several smaller grooves, rather than one continuous or interrupted groove. This type of oil groove provides a higher level of lubrication to the shaft, which helps to reduce friction and wear. Multiple oil grooves are ideal for applications that require a high level of lubrication, such as high-speed or heavy-load applications.
- Spiral Oil Groove
The spiral oil groove is a type of oil groove that is spiral-shaped and runs around the circumference of the bushing. This type of oil groove provides a continuous and consistent supply of oil to the shaft, which helps to reduce friction and wear. Spiral oil grooves are ideal for applications that require a high level of lubrication, such as high-speed or heavy-load applications.
In conclusion, there are several types of oil grooves available, each with its own unique advantages and applications. When selecting an oil groove bushing, it is important to consider the specific requirements of the application, such as load capacity, speed, and operating temperature, and to choose a type of oil groove that meets these requirements, ensuring reliable and long-lasting performance.
Bronze Toggle Bushings Material
Material grade |
600 | 600S1 | 600S2 | 600S3 | 600S4 | 600S5 |
CuZn25AI6Mn4Fe3 | Cusn5PbZn5 | CuAI10Ni5Fe5 | CuSn12 | CuAI10Fe3 | CuZn25AI6Mn4Fe3 | |
Density | 8.0 |
8.9 |
7.8 |
8.9 | 8.5 | 8.0 |
Yield Strength | >450 |
>90 |
>260 |
>150 | >160 | >450 |
Tensile strength | >750 |
>200 |
>600 |
>260 | >590 | >800 |
Elongation % | >12 |
>15 |
>10 |
>8 | >15 | >8 |
Hardness | >210 |
>70 |
>150 |
>95 | >160 | >250 |
Solid Bronze Turned Bushings
Bronze Bushing Tech. Data
Performance | 650-1 | 650-2 |
650-3 |
650-4 | 650-5 |
Max. Load |
100 |
60 |
70 |
250 |
60 |
Max. Sliding Speed |
dry 0.4 oil 0.5 |
2 |
2 |
0.1 |
0.5 |
Max. PV |
3.8 |
0.5 |
0.6 |
2.5 |
0.8 |
Density |
8.0 |
8.0 |
7.6 |
7.8 |
7.3 |
Tensile strength |
>600 |
>250 |
>500 |
>1500 |
>250 |
Elongation (%) |
>10 |
>4 |
>10 |
– |
– |
Hardness |
>210 |
>80 |
>80 |
HRC>55 |
>160 |
Temp. |
300 |
350 |
300 |
350 |
400 |
Friction coefficient |
Oil:0.03 |
Oil:0.03 | Oil:0.03 | Dry running:0.16 | Dry running:0.16 |
Solid lubricant
Solid lubricant | SM01 | SM02 | SM03 |
Main ingredients | Graphite | Graphite + disulfide group | PTFE+graphite+paraffin |
Characteristic | Very good chemical stability Qualitative, use temperature <250. C |
Very good wear resistance and chemical stability Sex, use temperature <400. C |
Very low friction coefficient and very good The water wettability, the use temperature is -40. C~80. C |
Applications | General use (Atmosphere) | High temperature, high load | For sea (w |
Bronze Toggle Bushings
Bronze Bushes Alloy materials
Corresponding grade | |||||
International grade | ZCuSn6Zn6Pb3 | ZCuSn6Zn6Pb3 | steel+
ZCuSn6Zn6Pb3 |
GCr15 | HT250 |
International ISO338 | GCuSn6Zn6Pb3 | GCuSn6Zn6Pb3 | steel)+
CuSn6Zn6Pb3Fe3Ni5 |
Harnessing Aluminum Bronze for Top-Notch Performance: Manufacturing Innovations and Broad Applications
As technology continues to evolve, businesses and industries have been continually seeking materials that provide superior performance and durability. Aluminum bronze, thanks to its commendable mechanical properties and excellent corrosion resistance, has become a material of choice for various applications. Let’s explore the manufacturing innovations and wide-ranging applications of this versatile alloy.
Manufacturing Innovation
Manufacturing with aluminum bronze requires innovation and expertise. The alloy is known for its high castability and machinability, meaning it can be easily shaped into complex components and machined to precise dimensions. Recent advancements in manufacturing technologies have further facilitated the processing of aluminum bronze, allowing for the creation of components with exceptional precision and uniformity.
Modern manufacturing techniques, such as computer numerical control (CNC) machining, enable detailed, high-accuracy production of aluminum bronze parts. Additive manufacturing or 3D printing methods have also been employed, providing an avenue for the rapid prototyping and production of custom components.
Superior Mechanical Properties
Aluminum bronze boasts an array of desirable mechanical properties that contribute to its popularity in numerous industrial applications. The alloy exhibits impressive strength and toughness, allowing it to resist heavy loads and shocks without deformation. Additionally, its superior wear resistance ensures a longer operational life for components made from this material.
The corrosion resistance of aluminum bronze is another factor that sets it apart. The alloy is highly resistant to a range of corrosive environments, including seawater and certain aggressive industrial chemicals. This makes it suitable for use in a broad spectrum of environments, from marine applications to chemical processing plants.
Wide-ranging Applications
Thanks to these advantageous properties, aluminum bronze finds use in a multitude of applications. In the construction and heavy equipment industries, the alloy is often used for bushings, bearings, and gears due to its load-bearing capabilities and durability. It is also utilized in the marine industry for ship propellers and underwater fastenings, thanks to its superior resistance to seawater corrosion.
Furthermore, in the energy sector, aluminum bronze is employed in the production of components for turbines, pumps, and valves. Its resistance to wear and high-stress situations makes it a reliable material for these critical components.
As we step forward together with our customers, the use of aluminum bronze continues to provide top performance and innovative solutions. Its remarkable mechanical properties, coupled with manufacturing innovations, offer immense potential across various industrial applications. The commitment to harnessing and expanding these possibilities ensures we continue delivering superior quality and efficiency in our products and services.
Bronze Toggle Bushings Groove Type
Solid-self-lubricating Bearings Standard size
Cutting lubrication grooves in various patterns can be achieved using different machining techniques depending on the material, the complexity of the pattern, and the precision required. Here are a few common methods:
1. CNC Machining
- Process: CNC (Computer Numerical Control) machines are highly versatile and can be programmed to cut complex patterns with high precision.
- Materials: Suitable for metals, plastics, and other machinable materials.
- Advantages: High precision, repeatability, and the ability to create complex patterns.
- Disadvantages: Initial setup and programming can be time-consuming and expensive.
2. EDM (Electrical Discharge Machining)
- Process: Uses electrical discharges (sparks) to erode material, allowing for the creation of intricate patterns.
- Materials: Typically used for hard metals and conductive materials.
- Advantages: Can produce very fine and precise grooves with complex shapes.
- Disadvantages: Slower process and higher cost compared to conventional machining.
3. Laser Cutting
- Process: Uses a focused laser beam to cut or engrave patterns into the material.
- Materials: Suitable for metals, plastics, and other materials that can be vaporized or melted by the laser.
- Advantages: High precision and the ability to create intricate patterns without physical contact.
- Disadvantages: Limited to materials that can be cut or engraved by a laser, and the initial setup cost can be high.
4. Waterjet Cutting
- Process: Uses a high-pressure jet of water, often mixed with abrasive particles, to cut materials.
- Materials: Suitable for a wide range of materials, including metals, plastics, ceramics, and composites.
- Advantages: Can cut thick materials and produce complex patterns without generating heat.
- Disadvantages: Slower than laser cutting and requires management of water and abrasive materials.
5. Manual Machining
- Process: Traditional machining techniques using lathes, mills, and other manual tools.
- Materials: Metals, plastics, and other machinable materials.
- Advantages: Lower initial cost and flexibility for small-scale or custom work.
- Disadvantages: Lower precision and higher labor intensity compared to automated methods.
Considerations for Cutting Lubrication Grooves:
- Pattern Complexity: Choose a method that can handle the complexity of the desired pattern.
- Material Type: Ensure the selected method is suitable for the material you are working with.
- Precision Requirements: Higher precision may necessitate CNC, EDM, or laser cutting.
- Production Volume: For high-volume production, automated methods like CNC or laser cutting are preferable.
- Cost Constraints: Balance the initial setup cost and per-unit cost based on your budget and production needs.
By selecting the appropriate method, you can effectively cut lubrication grooves in virtually any pattern required for your application.
A Deep Dive into Bronze Bushings with Oil Groove Design
The world of industrial machinery is replete with diverse components, each playing a unique role in the functioning and efficiency of the system. Among these, bronze bushings with an oil groove design have earned a reputation for their robustness and their ability to significantly enhance the performance of a range of equipment. Let’s delve into the features and benefits of these specialised bushings. Bronze bushings are renowned for their superior durability and anti-corrosive properties. Bronze, an alloy primarily composed of copper, is resistant to wear and tear, making it an excellent material for bushings that need to withstand high loads and stress. The resilience of bronze allows for a longer lifespan of the bushing, which in turn reduces the need for frequent replacements and maintenance. Design: Oil Groove: The design of these bushings incorporates an oil groove, which is a trench or channel cut into the inner surface of the bushing. The purpose of this groove is to retain lubricant and distribute it evenly across the bearing surface when the machinery is in operation. The lubricant reduces friction between the bushing and the shaft, thus preventing overheating, wear and tear. This further enhances the bushing’s lifespan, and improves the overall efficiency of the machine by reducing energy loss due to friction. The oil groove design therefore plays a pivotal role in maintaining the smooth functioning of the equipment, and in reducing maintenance time and costs.