Metal Polymer Composite
Metal Polymer Composite
Say goodbye to the hassle of frequent lubrication maintenance. Our self-lubricating technology ensures smooth operation and reduces wear and tear, extending the lifespan of your equipment. Experience uninterrupted productivity and cost savings as you bid farewell to the need for messy lubricants and time-consuming upkeep.
Manufacturing on Demand, alternative solutions
Metal Polymer Composite
Metal/Polymer Composite Plain Bush: Maintenance-Free and ISO 3547 Compliant
the Metal/Polymer Composite Plain Bush: Maintenance-Free and ISO 3547 Compliant
The metal/polymer composite plain bush represents a revolutionary solution for various industrial applications. Compliant with ISO 3547 standards, this bushing combines the strength of steel backing with the versatility of a polymer sliding layer, offering unparalleled performance and reliability.
Key Features:
Maintenance-Free: The composite design eliminates the need for regular maintenance, reducing downtime and operational costs.
Steel Backing: The robust steel backing provides exceptional support and stability, ensuring durability even in demanding environments.
Flange Bush: Equipped with a flange for easy installation and added stability in applications requiring axial support.
Low-Maintenance Sliding Layer: The sliding layer, crafted from a polymer composite, is designed for minimal wear and friction. It features lubrication pockets that enhance lubricant retention, further reducing the need for maintenance.
Bronze or Stainless Steel Backing: Customers have the option to choose between a bronze or stainless steel backing, depending on specific application requirements.
Applications:
The metal/polymer composite plain bush finds wide-ranging applications across industries, including:
Automotive: Suspension systems, steering components, and engine mechanisms.
Machinery: Bearings, linkages, and pivot points in various machinery and equipment.
Marine: Marine engine components, ship propulsion systems, and deck machinery.
In conclusion, the metal/polymer composite plain bush offers a maintenance-free solution with superior performance and reliability. With its innovative design and versatile applications, it is poised to become an essential component in modern industrial settings.
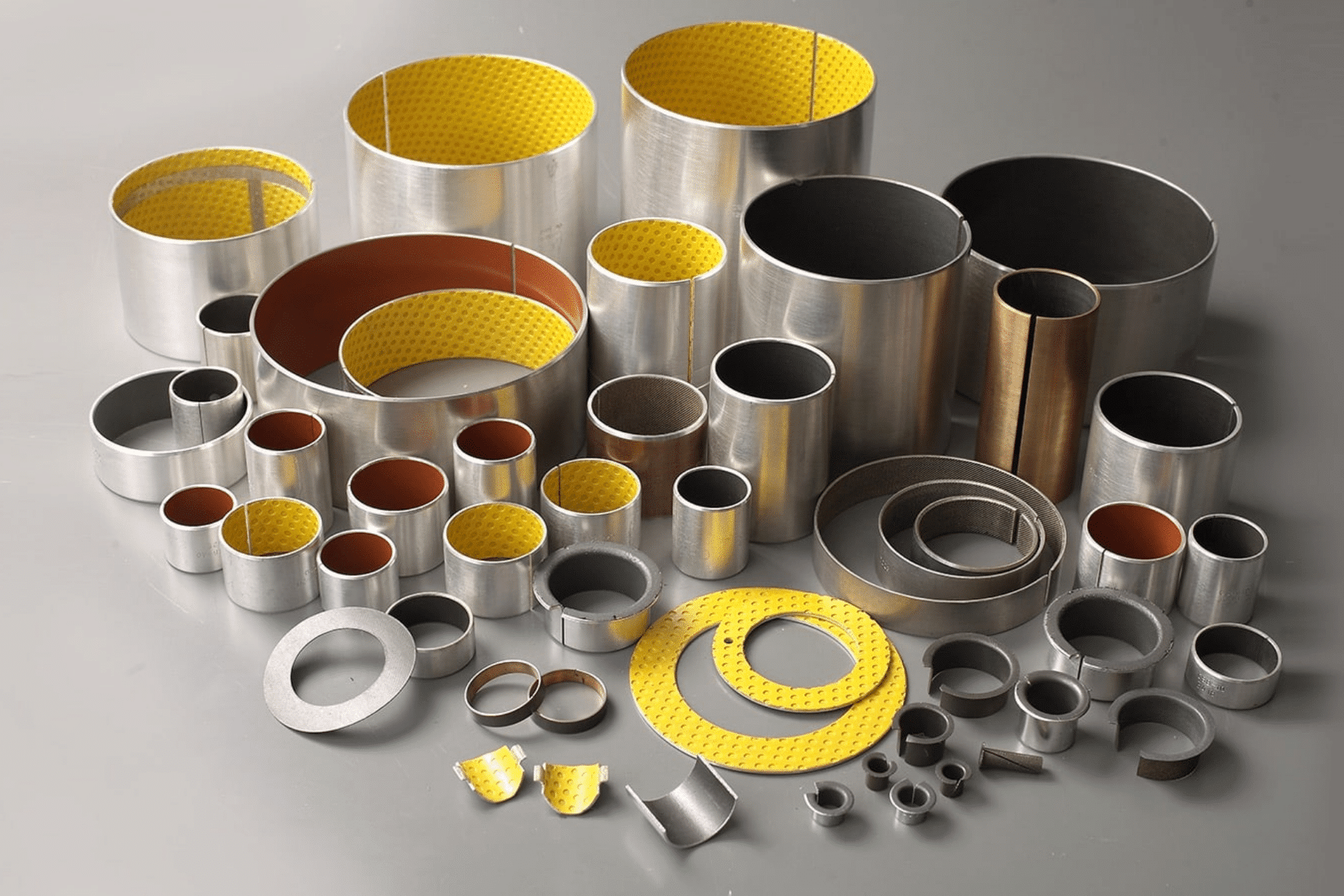
Metal/Polymer Composite Plain Bush
Boundary self-lubricating bushings present a high-performance bearing solution that combines the advantages of multiple materials to deliver outstanding friction and wear resistance. Designed to reduce friction and wear during mechanical motion, these bushings aim to lower maintenance costs and enhance equipment operational efficiency.
Structure and Materials:
Boundary self-lubricating bushings typically consist of the following components:
Base: The base of the bushing is usually made of steel, offering excellent strength and rigidity to withstand loads during mechanical motion.
Intermediate Layer: Sintered spherical bronze powder is sandwiched between the steel base, providing superior lubrication and wear resistance, reducing friction between the bushing and mating components.
Surface Layer: The bushing’s surface is coated with modified polyoxymethylene (POM). POM, an engineering plastic, exhibits a low friction coefficient, excellent wear resistance, and chemical stability. Modified POM further enhances the bushing’s wear resistance and impact resistance.
Lubrication Pockets: The design of lubrication pockets on the surface helps retain lubricating oil, thereby providing better lubrication performance under boundary lubrication conditions.
Applications:
Boundary self-lubricating bushings find applications in various environments, especially those requiring low friction and high wear resistance. They are commonly used in:
Mechanical Power Transmission: In components such as rails, sliders, and bearings, reducing friction and wear between moving parts.
Heavy Industries: In sectors like steel, mining, and cement, where they endure heavy loads and impacts.
Food and Pharmaceutical Industries: Due to their non-toxic nature, they are suitable for food processing and pharmaceutical equipment, ensuring product hygiene and safety.
Water Treatment and Chemical Industries: Their corrosion resistance protects equipment from damage in environments exposed to chemicals.
Advantages:
Compared to traditional bronze bushings, boundary self-lubricating bushings offer several advantages:
Cost-Effectiveness: By using a combination of steel and bronze powder, along with special surface treatments, material costs can be reduced without compromising performance.
Extended Lifespan: Thanks to their excellent wear resistance and self-lubricating properties, the lifespan of these bushings is typically longer than that of traditional bronze bushings.
Low Maintenance Requirements: Self-lubricating bushings reduce the need for lubricating oil, thus lowering maintenance costs and time.
Environmentally Friendly: Reduced lubricating oil usage helps minimize environmental pollution and improve workplace cleanliness.
In conclusion, boundary self-lubricating bushings represent an efficient, economical, and environmentally friendly bearing solution suitable for a wide range of industrial applications.
Exploring the World of Composite Bearings: A Game Changer in Industrial Applications
Composite bearings have carved a niche in the world of mechanical components, thanks to their robust design and versatile applications. These bearings are composed of a steel-backed layer coupled with either POM (polyoxymethylene) or PEEK (polyether ether ketone) coated bronze, creating a durable and efficient system for managing friction and load.
Structure and Composition
The core of composite bearings is high-quality mild steel, which serves as a substrate. This is layered with sintered porous spherical bronze powder, providing a solid foundation for the bearing’s functionality. The surface of the bearing is treated with a wear-resistant lubricant, primarily consisting of modified POM or PEEK. This sophisticated structure not only enhances durability but also supports efficient operation under various conditions.
Lubrication Efficiency
One of the standout features of composite bearings is their lubrication system. The surface includes strategically placed oil holes which fulfill dual purposes: storing grease and trapping dust. This design significantly extends the lifespan of the bearings by maintaining cleanliness and lubrication. Additionally, the copper powder layer aids in heat dissipation during operation and reinforces the bond between the plastic layer and the base steel plate.
Load Carrying and Lubrication Conditions
Composite bearings are engineered to excel in mechanical load carrying. They are particularly adept at operating under boundary lubrication conditions, where they can function for extended periods without the need for regular oiling. The regular arrangement of oil holes ensures optimal distribution of lubricant across the bearing surface, facilitating smooth operation even under high loads and low-speed motions.
Application Versatility
The practical applications of composite bearings are extensive and varied. They are particularly beneficial in environments where fluid lubrication is challenging, such as in heavy-load, low-speed, or oscillating movements. Industries that benefit from these bearings include:
- Automotive Industry: Used in pedal assemblies, balance bushings, brake calipers, and more.
- Logistics Machinery: Ideal for trucks, truck-mounted cranes, forest machinery, and packaging machines.
- Hydraulic and Pneumatic Components: Useful in hydraulic motors, cylinders, and agricultural machinery.
Environmental and Manufacturing Advantages
Composite bearings are designed to be environmentally friendly. The wear-resistant materials used do not contain harmful pollutants like lead, ensuring compliance with RoHS standards. Moreover, the flexibility in manufacturing allows for both standard construction products like bushings and thrust washers, as well as custom solutions tailored to customer specifications.
Conclusion
Composite bearings represent a significant advancement in bearing technology. Their unique structure, combined with superior lubrication and load-carrying capabilities, makes them suitable for a wide range of industrial applications. With the added benefits of environmental safety and manufacturing flexibility, composite bearings are not just a component but a comprehensive solution in modern engineering. Whether for the automotive sector, heavy machinery, or hydraulic systems, these bearings offer reliability and performance that can significantly enhance the efficiency and lifespan of machinery.
Your expert in self-lubricating Bearing
and Bronze alloys – serving globally
Brand replacement products and functionally equivalent parts, alternative solutions
Manufactures flange bronze bearings, service & maintenance companies to meet the exacting specifications required in a wide range of industrial applications.
Machined bronze bushing that meet the exacting requirements & specifications supplied by our clients. Spherical bearings, spindles, semi-spheres and supports that we have manufactured.
You will find to follow a selection of self lubricating bronze bearing material CuSn7Zn4Pb7, CuSn12, CuAl10Fe5Ni5,
CuZn25Al5Mn4Fe3
Alternative solution,We offer an outsourced machining service for bronze bushes, manufacturing precise parts to the designs supplied to us by our clients.
Selection of other composite bushing material of self lubricating bearing that we have manufactured.
Wrapped Bronze Sleeve Bearing, Are you interested in our products?
Manufacturer of bimetal and steel bronze bushing parts according to client’s drawing.