Finished Machined Bronze Wear Plates
Finished Machined Bronze Wear Plates
Say goodbye to the hassle of frequent lubrication maintenance. Our self-lubricating technology ensures smooth operation and reduces wear and tear, extending the lifespan of your equipment. Experience uninterrupted productivity and cost savings as you bid farewell to the need for messy lubricants and time-consuming upkeep.
Manufacturing on Demand, alternative solutions
Finished Machined Bronze Wear Plates
Understanding the Benefits and Manufacturing of Bronze Wear Plates
Bronze wear plates are critical components in industrial machinery, playing a pivotal role in reducing wear and tear, enhancing machine life, and streamlining operations. These plates have gained popularity due to their remarkable properties and versatile applications.
Bronze wear plates play a pivotal role in managing linear motion, especially in scenarios involving substantial forces. Acting as linear bearings, they are essential in guiding and controlling movement. At viiplus, we provide an extensive range of bronze wear plates, encompassing options from basic unfinished cast bronze plates to completely finished and precisely machined components. These versatile plates are designed to meet diverse industrial needs, ensuring smooth operation and longevity in machinery. Whether you’re looking for a basic solution or a more sophisticated, custom-fit component, our selection caters to a wide array of requirements, promising quality and efficiency in every piece.
The oilless 500 series encompasses a range of self-lubricating bearings and wear plates engineered for exceptional performance under extreme temperature conditions and high-load capacities. This series features journal-style bearings and flat wear plates, notably the oilless 500 Sp101 Bearing Pad Slide Wear Plate. Distinctive attributes of the oilless 500 series are:
- Bearings made of high-strength brass integrated with solid lubricant.
- Enhanced precision.
- Suitable for applications requiring large oscillating angles in circumferential oscillation.
The manufacturing process of the oilless 500 series bearings and wear plates involves advanced casting techniques that incorporate a unique solid lubricant into the brass alloy base. This innovative approach eliminates the need for traditional lubrication, offering a significant advantage in scenarios where conventional lubrication is impractical or undesirable.
Customizable and available for mass production, the oilless 500 series can accommodate orders up to 500 units per week. It caters to a diverse range of industrial applications, such as heavy machinery, hydroelectric power, offshore marine operations, and the nuclear sector.
Exploring the Versatility and Efficiency of Bronze Wear Plates,Cast Bronze Wear Plate, Bridge Bearing Plate, Finished Machined Bronze Wear Plates, Self Lubricating Bronze Wear Plate
Bronze wear plates are integral components in various machinery, designed to reduce wear and tear between moving parts. These plates serve as a bearing surface, effectively lowering friction and wear. This not only prolongs the lifespan of the machine but also cuts down on maintenance expenses.
Alloys: Our cast bronze wear plates are available in the following bronze alloys:
For a comprehensive wear plate solution, we provide fully machined wear plates tailored to your specific requirements. These plates are precisely machined according to your unique specifications. Common configurations include custom hole patterns, grease grooves, and mounting holes.
These plates are generally crafted from bronze alloys, like aluminum bronze alloys, known for their remarkable wear properties and low friction coefficients. The most commonly used alloy is C95400, predominantly made of copper with aluminum as the primary alloying element, boasting outstanding mechanical properties and wear resistance.
Some bronze wear plates incorporate graphite into their composition. This addition bestows self-lubricating properties on the plates, diminishing the need for regular maintenance and enhancing efficiency.
The production of these wear plates involves precise machining to meet specific requirements. They often feature custom designs, including unique hole patterns, grease grooves, and mounting holes. Their applications are diverse, ranging from press die and slide components to various types of dies (stamping, forming, progressive, fine blanking) and molds (injection, die casting).
Employing bronze wear plates enables manufacturers to achieve smoother and more efficient operations, reduce maintenance costs, and enhance the performance of their machinery, particularly in press die and slide components.
Regular lubrication is essential for these wear plates to prevent excessive wear. However, the graphite-impregnated types can function without external lubrication, making them suitable for situations where oil lubrication is impractical or frequent lubrication is not feasible.
In the world of industrial machinery and construction, the importance of reliable and durable components cannot be overstated. Among these essential components are bronze wear plates, known for their resilience and versatility. In this post, we’ll delve into the world of bronze wear plates, exploring their types, applications, and the specific alloys that make them indispensable in various industries.
1. Introduction to Bronze Wear Plates
Bronze wear plates are utilized in a variety of applications due to their strength and corrosion resistance. They play a critical role in reducing friction and wear in heavy machinery, thereby extending the lifespan of the equipment.
2. Types of Bronze Wear Plates
- Finished Machined Bronze Wear Plates: These plates are ready for use in machinery and are known for their precise dimensions and smooth surface finish. Ideal for high-load applications, they provide excellent wear resistance and durability.
- Precision Ground Wear Plate: These plates are characterized by their exceptionally smooth surface, achieved through precision grinding. This process ensures a high level of accuracy and uniformity, making them suitable for applications where precision is paramount.
- Self-Lubricating Bronze Wear Plate: These plates are designed to release lubricant during operation, reducing the need for regular maintenance. They are particularly useful in environments where lubrication is challenging.
3. Bronze Alloys Used in Wear Plates
Different bronze alloys offer unique properties, making them suitable for specific applications:
- C95400 Aluminum Bronze: Known for its high strength and resistance to corrosion, this alloy is ideal for heavy-load applications.
- C93200 SAE 660 Bearing Bronze: This alloy is renowned for its excellent machining properties and wear resistance, making it a popular choice for bearings and bushings.
- C86300 Manganese Bronze: With its impressive strength and resistance to impact, this alloy is suitable for heavy-duty applications.
4. Applications of Bronze Wear Plates
- Cast Bronze Wear Plate: Used in a variety of industrial applications, these plates offer superior resistance to wear and tear.
- Bridge Bearing Plate: Essential in bridge construction, these plates bear heavy loads while allowing for slight movements, reducing stress on the structure.
- Bronze Slide Bearing: These bearings facilitate smooth sliding movements in machinery, reducing friction and wear.
- Aluminum Bronze Wear Plate: Particularly used in environments where corrosion resistance is crucial, such as in marine applications.
Bronze wear plates, with their diverse types and alloys, are crucial in ensuring the efficiency and longevity of machinery in various sectors. Whether it’s for heavy industrial use or precision applications, the right bronze wear plate can significantly impact the performance and durability of your equipment.
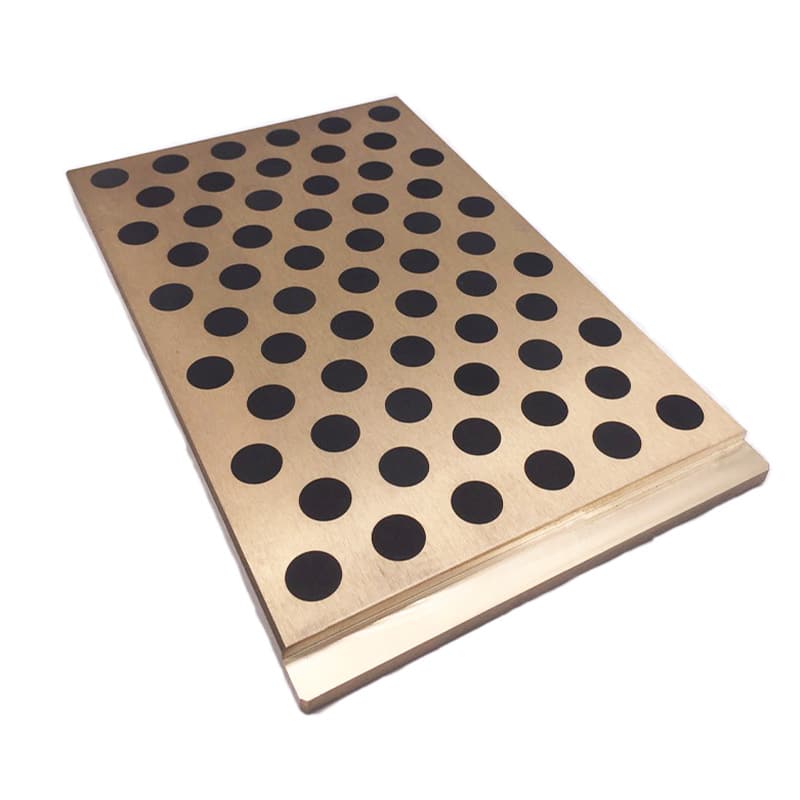
Finished machined bronze wear plates are components used in machinery to minimize wear and tear between moving parts.
Custom parts play a crucial role in various industrial applications, and at our company, we specialize in crafting components from a wide range of materials to meet specific needs. Our offerings include parts made from several types of bronze and other metal alloys, each selected for its unique properties and advantages:
- Bearing Bronze Alloys: Ideal for applications requiring high wear resistance and strength. These alloys are commonly used in bearings and bushings due to their durability and load-bearing capabilities.
- Aluminum Bronze Alloys: Known for their excellent corrosion resistance and strength, these alloys are suitable for marine and heavy industrial applications.
- Tin Bronze Alloys: These alloys offer superior resistance to fatigue and wear, making them ideal for gears and other high-stress components.
- Manganese Bronze Alloys: With high strength and resistance to impact, these alloys are perfect for heavy-duty applications where toughness is key.
- Brass Alloys: Versatile and corrosion-resistant, brass alloys are widely used in decorative as well as functional parts.
- Copper Alloys: Known for their excellent thermal and electrical conductivity, copper alloys are used in a variety of electrical components.
In addition to these material options, we offer a range of specialized features to enhance the performance of our custom parts:
- Oil/Grease Grooves: These features are integrated into bearings and wear plates to facilitate lubrication and reduce wear.
- Flanges: Custom flanges can be designed to meet specific mounting and connection requirements in machinery.
- Wear Plates: Essential in reducing friction and wear in moving parts, these plates can be tailored to various sizes and specifications.
- Graphite Plugs: These are used in self-lubricating bearings, providing consistent lubrication and reducing maintenance needs.
- Thrust Washers: Designed to absorb axial loads, these washers are crucial in many types of machinery for smooth operation.
- Large Diameter Bearings: We specialize in producing large diameter bearings for applications requiring support for substantial loads.
Our commitment is to provide high-quality, precision-engineered custom parts that meet the exact requirements of our clients, ensuring optimal performance and longevity in their applications. Whether you need a standard part or a complex custom solution, our expertise in metal alloys and component design can deliver the results you need.
Benefits of Using Bronze Wear Plates
- Reduced Friction and Wear: The primary function of bronze wear plates is to serve as a bearing surface, significantly reducing friction between moving parts. This reduction in friction translates to less wear and tear on machinery.
- Extended Machine Life: By minimizing wear, bronze wear plates contribute to the longevity of the machines in which they are used. This extended life span of machinery is crucial for industries seeking to optimize asset usage.
- Lower Maintenance Costs: With reduced wear comes fewer maintenance requirements. This not only saves on direct repair costs but also minimizes machine downtime, contributing to overall operational efficiency.
- Versatility in Applications: Bronze wear plates are utilized in various industrial applications, including but not limited to, press die components, stamping dies, and injection molds. This versatility makes them a valuable component across numerous sectors.
- Self-Lubricating Properties: Some bronze wear plates are designed with self-lubricating features, especially those embedded with graphite. This reduces the need for frequent lubrication, making them ideal for challenging environments where regular maintenance is not feasible.
Manufacturing of Bronze Wear Plates
The production process of bronze wear plates typically involves:
- Alloy Selection: The process begins with selecting the appropriate bronze alloy. Commonly used alloys include aluminum bronze, known for their excellent wear resistance and low coefficient of friction.
- Casting or Forging: The selected alloy is then cast or forged into the basic shape required for the wear plate.
- Machining: The cast or forged blanks are then machined to precise dimensions. Advanced machining techniques ensure that the plates meet the exact specifications required for different applications.
- Custom Features: Depending on their intended use, wear plates may be machined with specific features like custom hole patterns, grease grooves, and mounting holes.
- Quality Control: Each wear plate undergoes rigorous quality control checks to ensure it meets the necessary standards and specifications.
Types of Bronze Wear Plates
- Standard Bronze Wear Plates: These are the most common types, used in general applications where wear resistance is the primary requirement.
- Graphite Impregnated Bronze Plates: These plates contain graphite and are used in applications requiring self-lubrication. They are particularly beneficial where regular lubrication is a challenge.
- Customized Wear Plates: Tailored to specific applications, these plates are designed with unique features like specific alloy compositions, shapes, and additional enhancements to suit particular industrial needs.
Conclusion
Bronze wear plates are an indispensable component in modern machinery, offering a multitude of benefits ranging from reduced maintenance to enhanced machine longevity. Their manufacturing process, which involves precision and customization, caters to a wide range of industrial applications. Understanding the different types of bronze wear plates available allows industries to select the most appropriate type for their specific needs, thereby maximizing efficiency and performance.
Your expert in self-lubricating Bearing
and Bronze alloys – serving globally
Brand replacement products and functionally equivalent parts, alternative solutions
Manufactures flange bronze bearings, service & maintenance companies to meet the exacting specifications required in a wide range of industrial applications.
Machined bronze bushing that meet the exacting requirements & specifications supplied by our clients. Spherical bearings, spindles, semi-spheres and supports that we have manufactured.
You will find to follow a selection of self lubricating bronze bearing material CuSn7Zn4Pb7, CuSn12, CuAl10Fe5Ni5,
CuZn25Al5Mn4Fe3
Alternative solution,We offer an outsourced machining service for bronze bushes, manufacturing precise parts to the designs supplied to us by our clients.
Selection of other composite bushing material of self lubricating bearing that we have manufactured.
Wrapped Bronze Sleeve Bearing, Are you interested in our products?
Manufacturer of bimetal and steel bronze bushing parts according to client’s drawing.