centrifugal cast
centrifugal cast
Say goodbye to the hassle of frequent lubrication maintenance. Our self-lubricating technology ensures smooth operation and reduces wear and tear, extending the lifespan of your equipment. Experience uninterrupted productivity and cost savings as you bid farewell to the need for messy lubricants and time-consuming upkeep.
Manufacturing on Demand, alternative solutions
centrifugal cast
Centrifugal Cast Bronze, centrifugal casting bronze bushings
specializes in providing oversized bronze bearings, casting self-lubricating bearing bushings, and groove bronze solutions. The company offers a wide range of centrifugal casting bronze bushings to suit different requirements, with a focus on high-quality, reliable performance, and customization options.
Centrifugal Cast Bronze is a specialized casting method used to produce bronze components with unique properties.
The ASTM B271 standard is related to centrifugal castings made from copper-based alloys. This specification is relevant to a variety of bronze materials that are often used in the production of bearings, bushings, and other components required for heavy-duty mechanical operations. An example of such a material is C93200 Bearing Bronze (also known as SAE660). This bronze variety is known for its excellent machinability, notable hardness, strength, and resistance to wear. It is particularly well-suited for bearings and bushings operating under medium loads and speeds, assuming there is sufficient lubrication. Another notable material is C95400 Aluminum Bronze, recognized for its extreme hardness, strength, and resistance to abrasion. These materials are frequently employed in various applications, including automotive parts, industrial machinery components, pump fittings, and many other areas.
Centrifugal Cast Bronze Bearings: Bronze Bushes and Ring Components, centrifugal cast, centrifugally cast, Centrifugal casting bronze Bushing, Bronze ring, oversized, Centrifugal Casting Bronze Bushing – Finish Machine Flange Size, Machining of flange planes for large structural components,
Centrifugally Cast Bronze
Centrifugal Cast Bronze Bearings Defined: These bearings are crafted utilizing the centrifugal casting technique, employing bronze as the core material. This method is instrumental in creating cylindrical or tubular components like bearings, achieved by rapidly rotating a mold and introducing molten metal. The outcome is a product with a consistent and dense grain structure, enhancing the quality of the bearings.
Characteristics of Bronze: The choice of bronze for bearings is driven by its outstanding attributes, such as resistance to wear and corrosion, and its natural self-lubricating capacity. These properties enable bronze bearings to endure substantial loads and high temperatures, making them versatile for numerous uses.
Self-Lubrication Advantage: One significant benefit of bronze bearings is their inherent self-lubricating feature, which minimizes the need for external lubrication. This quality renders them low-maintenance and ideal for scenarios where applying lubrication is impractical.
Customization Options: There is a broad spectrum of sizes and bronze alloys available for centrifugal cast bronze bearings. This diversity allows for tailoring to meet specific needs, with different alloys offering varied benefits like enhanced strength or better resistance to corrosion.
Use Cases: These bearings are integral in a variety of sectors, including the automotive, aerospace, marine, and industrial machinery industries. They are essential in numerous applications such as engines, gearboxes, pumps, and other equipment that demands dependable and long-lasting bearings.
In essence, centrifugal cast bronze bearings are meticulously designed components produced via a distinct casting process, with bronze as the foundational material. They exhibit superior performance traits and are exceptionally suited for situations where dependability and durability are paramount.
Centrifugal Casting Method: This process involves rotating a mold at high velocities while pouring liquid bronze into it. The action of centrifugal force evenly distributes the molten metal, facilitating the creation of cylindrical or ring-like shapes. This technique is especially effective for producing bronze components of high density and quality.
Benefits:
- Consistent Grain Texture: The centrifugal casting technique yields a bronze with a uniform and fine grain structure, enhancing its mechanical characteristics.
- Enhanced Density: By using centrifugal force, the process minimizes gas porosity, resulting in a dense and sturdy casting.
- Capability to Form Complex Shapes: This method is adept at crafting intricate and hollow forms, such as cylinders or rings.
- Improved Metallurgical Qualities: The process augments the metallurgical properties of bronze, making it suitable for a wide range of uses.
Uses: Components made from centrifugal cast bronze are utilized in various sectors, including the production of gears, bushings, bearings, and other mechanical parts, prized for their strength and dependability.
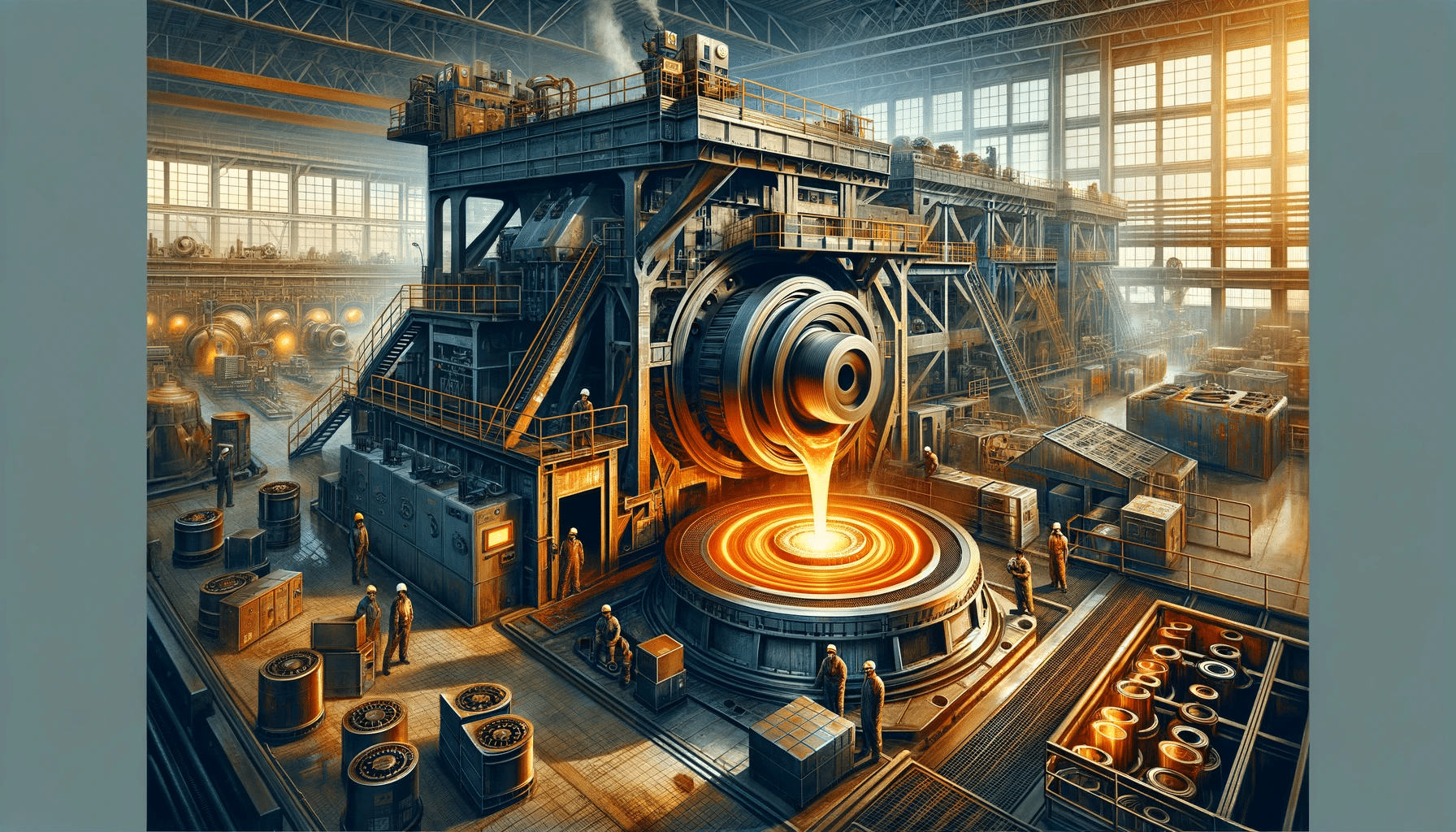
Alloy Family and Their Grades:
- Red Brass Alloys: C83300, C83600, C83800
- Semi-Red Brass Alloys: C84400, C84800
- Yellow Brass Alloys: C85200, C85400, C85700
- Manganese Bronze Alloys: C86200, C86300, C86400, C86500
- Copper-Silicon Alloys: C87200, C87500
- Leaded Tin Bronze Alloys: C92200, C92300, C92600, C92700, C93700, C93800, C94100, C94500
- Tin Bronze Alloys: C90300, C90500, C90700, C90800, C91600, C91700, C93200, C93400, C93500, C94300
- Aluminum Bronze Alloys: C95200, C95300, C95400, C95500, C95800
- Copper Nickel Alloys: C96200, C96400
- Nickel Silver Alloys: C97300, C97600, C97800
- Pure and Chrome Copper Alloys: C81100, C81500
Centrifugal Casting: Advantages and Limitations
Advantages:
- Enhanced Mechanical Properties: Centrifugal casting often leads to more dense and fine-grained structures. This can increase mechanical strength properties like tensile strength, yield strength, and elongation by up to 30% compared to traditional gravity or static casting methods. The high pressure from centrifugal force contributes to this improved grain structure.
- Reduction of Defects: This method effectively separates less dense impurities, which are then removed during machining, resulting in parts free of defects. It also consistently avoids issues like shrinkage cavities, gas pockets, and blowholes.
- Cost Efficiency: Centrifugal casting can create complex shapes with less need for machining, recognized to cost savings. The uniformity and other beneficial characteristics of the castings can also reduce the amount of time and material wasted during machining.
- Production Flexibility: The process is versatile, allowing for the cost-effective production of various shapes and sizes.
- Improved Quality: Products made using centrifugal casting tend to be more resistant to atmospheric corrosion due to fewer line defects and higher density. The process also encourages directional solidification, which can decrease or eliminate gas and porosity defects.
Limitations:
- Shape and Size Constraints: Centrifugal casting is mainly limited to cylindrical shapes and has certain size restrictions. It may not be as effective for complex, hollow parts with intricate internal structures.
- Surface Finish Quality: Achieving a high-quality surface finish might be more challenging with this method, potentially necessitating additional finishing processes.
- Control of Inner Wall Dimensions: The dimensions of the inner wall can be less precisely controlled compared to the outer wall.
- Alloy Limitations: Not every alloy is suitable for centrifugal casting, limiting the range of materials that can be used with this technique
Cast Bronze Alloys Operating Temperatures
Alloy | C93200 Bronze Bearings | C95400 Bronze Bearings | C93700 Bronze Bearings | C93800 Bronze Bearings | |
Brinell | 65 typical (500kg load) | 175 (3000kg load) | 60 typical (500kg load) | 55 typical (500kg load) | |
Min Operating Temperature | (-450°F) | (-450°F) | (-450°F) | (-450°F) | |
Max Operations Temperature | (+500°F) | (+750°F) to (+1200°F) Intermittent | (+500°F) | (+500°F) | |
Alloy | C90700 | C90300 | C86300 | C95500 | C95900 |
Brinell | 100 typical (500kg load) | 70 typical (500kg load) | 225 (3000 kg load) | 195 (3000kg load) | 241 min (3000kg load) |
Min Operating Temperature | (-450°F) | (-450°F) | (-450°F) | (-450°F) | (-450°F) |
Max Operations Temperature | (+550°F) | (+550°F) | (+400°F) | (+750°F) to (+1200°F) Intermittent | (+750°F) to (+1200°F) Intermittent |
Building on the information provided, we have developed a downloadable chart that will assist in selecting the most appropriate bronze alloy for your bearing application.
Material grade (GB) |
Main features | Applications |
ZCuPb10Sn10 grade | Lubrication performance, wear resistance and corrosion resistant performance is good, suitable for bimetal casting materials | Surface pressure is high, and there is the lateral pressure of the sliding bearing, such as rolling rolling, vehicle use bearing, load peaks 60 mpa hit parts, as well as the highest peak of 100 mpa bimetallic bearing bush of the internal combustion engine, and the piston pin sets, lining, etc. |
ZCuPb15Sn8 grade | Under the condition of lack of lubricant and use water quality lubricants, sliding and lubricating, free cutting, casting performance is poor, for dilute sulfuric acid corrosion resistant performance is good | Surface pressure is high, and the lateral pressure of bearing, copper cooling pipe can be made from cold rolling mill, impact resistance load of up to 50 mpa parts, internal combustion engines of bimetallic bearing, mainly used for the biggest load of 70 mpa of piston pin set, acid-proof accessories |
ZCuPb20Sn5 grade | At higher sliding performance, in the absence of a lubricating medium and water as medium are particularly good self-lubricating performance suitable for bimetal casting material, sulfuric acid corrosion resistance, easy cutting, casting performance is poor | High sliding speed of the bearing, and crusher, water pump, cold rolling mill bearings, piston pin load of 70 mpa |
ZCuPb30 grade | Have good self-lubrication, free cutting, casting performance is poor, easy to produce the gravity segregation | High sliding velocity of bimetallic bearing shell, wearing parts, etc. |
ZCuZn25Al6Fe3Mn3
grade |
With high mechanical properties, the casting performance is good, good corrosion resistance, has a tendency to stress corrosion | Suitable for high strength, wear parts, such as bridge plate, nut, screw, wear-resistant plate, the slider, and worm gear, etc |
ZCuZn26Al4Fe3Mn3 grade | With high mechanical properties, the casting performance is good, in the air, water, and seawater corrosion resistance is good, can be welded | Require high strength, corrosion resistant parts |
ZCuZn38Mn2Pb2
grade |
Have higher mechanical properties and good corrosion resistance, abrasion resistance, good cutting performance | General purpose structure, ship, instrument appearance, simple casting using such as sleeve, sleeve, bearings, slider, etc |
ZCuZn40Mn3Fe1 grade | With high mechanical properties, good casting properties and machinability, and in the air, water, and water has good corrosion resistance, has a tendency to stress corrosion cracking | Seawater corrosion parts, pipe fittings and under 300 °C, manufacturing and other large Marine propeller castings |
ZCuZn33Pb2 grade | Structural material, feed temperature is 90 °C when good oxidation resistance, electrical conductivity of about 10 ~ 14 ms/m | The shell of gas and water supply equipment, machinery manufacturing, electronics, precision instruments and optical instruments of component parts |
Other standards and material | ASTM, JIS, AISI, EN, BS; Manganese brass: C86300 and etc.; Tin bronze: C83600, C93200, CuSn12, CuSn7Zn4Pb7 and etc.; Aluminum Bronze: C62900, C95400, C95500, CuAl10Fe5Ni5 and etc.. |
Specification | Customized Bronze/Brass/Copper Alloy Centrifugal Casting Bushing with oil groove in China |
Material | Stainless steel, Alloy Steel, Brass, Copper, Aluminum, Aluminum alloy, Iron |
Machining | CNC machining center, CNC lathe |
Casting Tolerance | IT5 – IT7,CT5-7 |
Machining tolerance | +/- 0.005mm,ISO2768-f,ISO-mk |
Heat treatment | Solid solution annealed, quenched and tempering |
Weight range | 0.1Kg-120Kg |
Dimensions | ≤1200mm×800mm×400mm |
Surface finish | Ra 1.6-Ra 3.2 |
Finish | Polishing, Shoot blasting, Glass bead sandblasting, etc. |
The difference between continuous casting and centrifugal casting
Continuous casting and centrifugal casting are two different metal casting processes, each with specific advantages and disadvantages.
Continuous casting
Continuous casting is a metal casting process that features:
Process: Liquid metal is continuously poured into the mold to form a long strip or plate casting.
Advantages: Increase process yield and reduce waste, suitable for the manufacture of shell composite metal castings.
Disadvantages: May result in less flexibility of part geometry and reduced productivity.
Centrifugal casting
Centrifugal casting is another metal casting process that features:
Process flow: Centrifugal force is used to manufacture cylindrical parts in industry, there are three variants of true centrifugation, semi-centrifugation and vertical centrifugation.
Advantages: High casting density, almost no defects, can prevent casting cracks.
Disadvantages: High investment required, high skilled labor requirements, slow production speed.
In summary, continuous casting is suitable for increasing production and reducing waste, while centrifugal casting is suitable for producing high-density, defect-free parts, but requires higher investment and technical requirements.
Your expert in self-lubricating Bearing
and Bronze alloys – serving globally
Brand replacement products and functionally equivalent parts, alternative solutions
Manufactures flange bronze bearings, service & maintenance companies to meet the exacting specifications required in a wide range of industrial applications.
Machined bronze bushing that meet the exacting requirements & specifications supplied by our clients. Spherical bearings, spindles, semi-spheres and supports that we have manufactured.
You will find to follow a selection of self lubricating bronze bearing material CuSn7Zn4Pb7, CuSn12, CuAl10Fe5Ni5,
CuZn25Al5Mn4Fe3
Alternative solution,We offer an outsourced machining service for bronze bushes, manufacturing precise parts to the designs supplied to us by our clients.
Selection of other composite bushing material of self lubricating bearing that we have manufactured.
Wrapped Bronze Sleeve Bearing, Are you interested in our products?
Manufacturer of bimetal and steel bronze bushing parts according to client’s drawing.