Bronze Graphite Plate
Bronze Graphite Plate
Say goodbye to the hassle of frequent lubrication maintenance. Our self-lubricating technology ensures smooth operation and reduces wear and tear, extending the lifespan of your equipment. Experience uninterrupted productivity and cost savings as you bid farewell to the need for messy lubricants and time-consuming upkeep.
Manufacturing on Demand, alternative solutions
Bronze Graphite Plate
The hardness and operating temperatures for the cast bronze alloys CuZn25Al6FeMn3, C93200, C95400, C93700, C93800, C90700, C90300, C86300, C95500, and C95900.
Bronze-graphite plates are perfectly suited for scenarios where conventional lubrication is either impractical or unwanted. These plates excel under conditions of heavy load and slow speeds, offering self-lubrication thanks to the integrated graphite. The specific CuZn25Al6FeMn3 alloy composition guarantees both the resilience and efficacy of the plate in challenging situations that demand resistance to high temperatures and dependable lubricating qualities.
To encapsulate, the CuZn25Al6FeMn3 bronze-graphite plate stands out as an effective choice for situations that require the ability to support heavy loads at low speeds, along with the necessity for self-lubrication and the capacity to withstand temperatures up to 450°C. Its distinctive alloy composition and structural design render it an ideal option for a range of industrial uses where traditional lubricating solutions fall short.
Operating Temperatures and Hardness Ratings of Cast Bronze Alloys: Cast bronze alloys are available in various types, each presenting unique strengths and limitations. The distinct characteristics of these alloys are primarily determined by incorporating specific elements into their composition in differing amounts. For instance, adding Lead (Pb) to a bronze alloy can enhance its machinability and impart natural bearing qualities, whereas integrating Aluminum (Al) can boost its load-bearing capabilities and impart resistance to corrosion, especially from seawater. The elemental makeup of bronze alloys allows for a range of beneficial properties to be achieved. Engineers looking to design the optimal alloy for bronze bearing applications often focus on properties such as operating temperature and hardness. Bronze bearings might have to operate under severe temperatures depending on their use. Thus, determining the exact minimum and maximum operating temperatures that a specific bronze alloy can withstand is essential for designing the perfect alloy for particular applications.
The CuZn25Al6FeMn3 bronze graphite plate is engineered specifically for use in high-load, low-speed settings where traditional lubrication methods are either unnecessary or impractical. This plate combines graphite with a bronze alloy base, ensuring self-lubrication while being capable of enduring high temperatures of up to 450°C (842°F), and in some instances, as high as 593°C (1100°F). Known also as high-lead tin bronze, the CuZn25Al6FeMn3 composition excels in wear resistance, has a robust capacity for bearing heavy loads, and exhibits outstanding resistance to corrosion.
CuZn25Al6Fe3Mn3 is a solid bronze material used for bushings and bearings. It is a copper-zinc alloy with additional elements like aluminum, iron, and manganese. This material offers high tensile strength and is suitable for applications requiring good wear resistance and durability.
- Chemical Composition:
- Copper (Cu): 60-66%
- Zinc (Zn): 22-28%
- Aluminum (Al): 5-7%
- Iron (Fe): 2-4%
- Manganese (Mn): 2-4%
- Properties:
- High tensile strength
- Good wear resistance
- Suitable for oil-lubricated applications
- Used in bushings, bearings, and other mechanical components!
This material is known for its reliability in various industrial applications due to its favorable combination of properties.
CuZn25Al6FeMn3 bronze graphite plate, Graphite-embedded bronze alloys are engineered to offer self-lubrication and withstand high temperatures, making them ideal for situations where conventional lubrication is impractical or unwanted. These alloys, particularly those made from the CuZn25Al6FeMn3 composition, are recognized for their capability to endure temperatures up to 450°C (842°F), and under specific circumstances, up to 593°C (1100°F). The inclusion of graphite, serving as a solid lubricant within the bronze framework, alongside the distinct properties of the CuZn25Al6FeMn3 bronze alloy—known for its remarkable wear resistance, high capacity for load-bearing, and superior corrosion resistance—enhances their application. The synergy of graphite and this specific bronze alloy results in materials that are highly suited for high-load, low-speed scenarios where traditional lubricants fail, such as in some industrial machines, vehicle parts, and heavy-duty equipment.
For scenarios demanding a bronze alloy that must resist temperatures of at least 450°C, the graphite-incorporated CuZn25Al6FeMn3 alloy stands out. This composition ensures the material’s optimal performance at high temperatures, offering the necessary self-lubrication and resistance to wear for challenging applications.
In essence, the CuZn25Al6FeMn3 bronze-graphite alloy is an optimal choice for various industrial uses requiring a minimum temperature resistance of 450°C. Its high-temperature endurance, coupled with its self-lubricating and wear-resistant characteristics, positions it as a preferred option in environments where conventional lubrication approaches are infeasible or undesired.
The hardness and operating temperatures of various cast bronze alloys are crucial for selecting the appropriate material for specific applications, especially in bearing and structural applications where these properties significantly impact performance and durability. Below is a detailed overview of the hardness (measured in Brinell hardness number) and operating temperature ranges (minimum and maximum) for the specified cast bronze alloys based on the provided information.
Hardness and Operating Temperatures
Alloy | Brinell Hardness (500kg/3000kg load) | Min Operating Temperature (°F) | Max Operating Temperature (°F) |
---|---|---|---|
C93200 | 65 typical | -450 | +500 |
C95400 | 175 | -450 | +750 to +1200 (Intermittent) |
C93700 | 60 typical | -450 | +500 |
C93800 | 55 typical | -450 | +500 |
C90700 | 100 typical | -450 | +550 |
C90300 | 70 typical | -450 | +550 |
C86300 | 225 | -450 | +400 |
C95500 | 195 | -450 | +750 to +1200 (Intermittent) |
C95900 | 241 min | -450 | +750 to +1200 (Intermittent) |
Key Points:
- Hardness: The Brinell hardness of these alloys ranges significantly, from as low as 55 typical for C93800 to as high as 241 min for C95900. This variation indicates the diversity in the mechanical properties of bronze alloys, making them suitable for a wide range of applications. Hardness affects wear resistance, durability, and the ability to withstand mechanical loads.
- Operating Temperature: All listed alloys have a minimum operating temperature of -450°F, showcasing their excellent performance in extremely cold environments. The maximum operating temperature varies, with some alloys like C95400, C95500, and C95900 capable of handling up to +1200°F intermittently, making them suitable for applications experiencing high temperatures.
- Application Suitability: The choice of alloy depends on the specific requirements of the application, including mechanical load, wear conditions, environmental factors, and required lifespan. For example, alloys with higher hardness and temperature tolerance, such as C95400 and C95900, are well-suited for high-load and high-temperature applications, while those with lower hardness, like C93800, may be more appropriate for applications where wear resistance is less critical.
This comprehensive overview based on the provided data highlights the importance of considering both hardness and operating temperature ranges when selecting a cast bronze alloy for specific applications. These properties, along with other factors like corrosion resistance and machinability, play a critical role in ensuring the optimal performance and longevity of the components made from these materials.
Graphite sliders and wear plates used in preform molds offer a variety of advantages and applications.
Features and Advantages of Graphite Sliders:
- Wear resistance and lubrication: The surface of the graphite sliders features grooves for graphite rods, greatly enhancing their wear resistance and lubrication, thus extending their lifespan.
- High temperature and load capacity: Graphite copper sliders are capable of withstanding high temperatures and loads, suitable for conditions with high temperatures or poor lubrication.
- Oil-free lubrication: Graphite copper sliders transcend the traditional reliance on oil and grease for lubrication, achieving oil-free lubrication which ensures stable and reliable practicality.
Materials and Structure:
- High-strength brass base: The graphite copper slider uses a high-strength brass base, embedded with orderly arranged graphite rods as the friction material. This combination enhances the hardness and wear resistance more than twofold compared to regular copper materials.
- Structural design: The graphite copper slider includes vertical and horizontal copper sliders, which are perpendicular and integrally formed. The horizontal copper slider features positioning holes on its side, with graphite holes on the upper surface and the left side of the vertical copper slider, where graphite rods are inserted.
Applications:
- Injection molding processing: Graphite copper sliders are extensively used in plastic injection molding machines, extrusion structures, automatic switches of high voltage, lifting supports in construction machinery, and in supporting arcs, pulleys, and transmission wheels in hydraulic projects.
- Preform molds: In preform molds, graphite sliders and wear plates are utilized for guide rails and sliders to provide better lubrication and wear resistance.
Market Products:
- Bronze solid graphite slide board: For example, oil-free self-lubricating guide plates and L-type rail sliders made from bronze solid graphite are used as wear plates in preform molds.
- Custom products: Some suppliers offer customized graphite sliders and wear plates to meet specific mold requirements.
In summary, the application of graphite sliders and wear plates in preform molds not only enhances the mold’s wear resistance and lubrication but also extends the mold’s service life, making them suitable for various industrial applications involving high temperatures and heavy loads.
Custom Milling CNC Machining
CNC milling is a common metalworking method that can be used for various operations on a workpiece, such as drilling, slotting, and chamfering. For custom hole machining, the following steps are typically used:
- Drilling: Using a drill bit to create the required hole diameter on the workpiece. The depth, position, and angle of the hole can be controlled programmatically according to design requirements. Different types of drill bits (flat-bottom drills, twist drills, etc.) can be used to meet various machining needs.
- Reaming: After drilling, a reamer is used to further enlarge the hole diameter to achieve non-standard sizes and meet special requirements.
- Finishing: A milling cutter is used to finish the hole wall, improving the surface quality. Contour milling and other processes can be employed to achieve complex hole shapes.
- Automated Programming: Using CAD/CAM software to program hole positions, dimensions, machining paths, and other parameters ensures machining accuracy and efficiency.
CNC hole machining provides high precision, efficiency, and automation, making it suitable for industries like aerospace, automotive, and mold making where strict requirements for hole shapes are necessary. By wisely selecting tools, machining parameters, and programming, various customized hole machining needs can be met.
For the custom machining of oil grooves on copper sliders:
- Drilling: Drill bits are used to create the required oil groove diameter on the copper slider. The depth, position, and angle of the drilling can be precisely controlled through CNC programming.
- Reaming: Following drilling, a reamer is used to expand the diameter to the required oil groove size. This allows for the creation of non-standard size grooves to meet special requirements.
- Finishing: Ball end mills or other specialized tools are used to finely finish the walls of the oil grooves, enhancing the surface quality and eliminating machining marks.
- Contour Milling: If the oil groove shape is complex, contour milling processes can be utilized. The machining is completed through roughing, semi-finishing, and finishing steps.
- Automated Programming: CAD/CAM software is used to program the dimensions, positions, and machining paths of the oil grooves, ensuring precision and enhancing efficiency.
Through the above CNC milling processes, oil grooves can be efficiently and accurately machined on copper sliders to meet lubrication and sealing requirements. The choice of tool types, machining parameters, and programming methods is crucial for achieving high-quality oil grooves.
graphite filled bronze Plate
Material: CuZn25Al6FeMn3: A high-strength bronze alloy Plate
Graphite-filled bronze plate, particularly those made from the CuZn25Al6FeMn3 alloy, are highly valued in industrial applications for their unique combination of mechanical properties and self-lubricating capabilities. The graphite-filled bronze platecan operate effectively in high-temperature environments up to 450°C (842°F)! High Load Capacity: The CuZn25Al6FeMn3 alloy can handle high loads, making it suitable for heavy-duty applications.
Graphite-filled bronze plate made from the CuZn25Al6FeMn3 alloy offer a robust solution for high-strength, high-temperature, and maintenance-free applications. Their unique combination of self-lubrication, high load capacity, and excellent wear and corrosion resistance makes them an optimal choice for various industrial uses where traditional lubrication methods are not feasible.
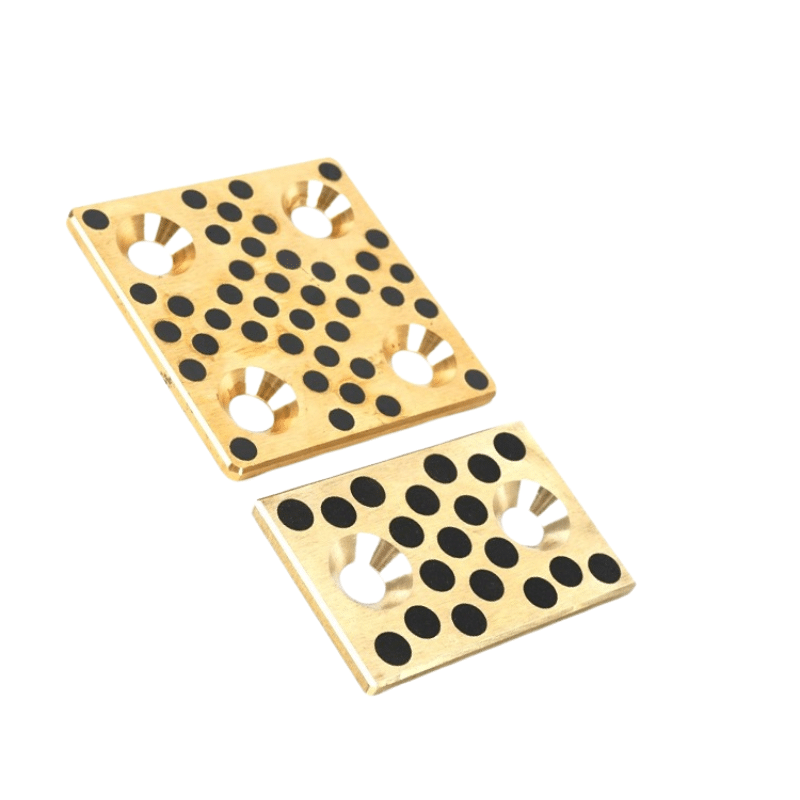
Your expert in self-lubricating Bearing
and Bronze alloys – serving globally
Brand replacement products and functionally equivalent parts, alternative solutions
Manufactures flange bronze bearings, service & maintenance companies to meet the exacting specifications required in a wide range of industrial applications.
Machined bronze bushing that meet the exacting requirements & specifications supplied by our clients. Spherical bearings, spindles, semi-spheres and supports that we have manufactured.
You will find to follow a selection of self lubricating bronze bearing material CuSn7Zn4Pb7, CuSn12, CuAl10Fe5Ni5,
CuZn25Al5Mn4Fe3
Alternative solution,We offer an outsourced machining service for bronze bushes, manufacturing precise parts to the designs supplied to us by our clients.
Selection of other composite bushing material of self lubricating bearing that we have manufactured.
Wrapped Bronze Sleeve Bearing, Are you interested in our products?
Manufacturer of bimetal and steel bronze bushing parts according to client’s drawing.