Centrifugal Cast Bronze Bushing: Custom Manufacturing of Large 3-Meter Diameter Components, large diameter bearings
Crusher Mining Machinery Spare Part, oversized Bronze Bearing. When it comes to industrial machinery and heavy equipment, one of the key components that facilitate smooth operation are bushings. In the high-demand applications where these machines are used, bushings need to be robust, reliable, and durable. A specific type of bushing that ticks all these boxes is the centrifugal cast bronze bushing. And when these bushings reach substantial sizes, such as a diameter of 3 meters, their manufacture demands specialist knowledge and skill. Let’s explore how custom manufacturers approach this task, and the different bronze material alloys they might employ.
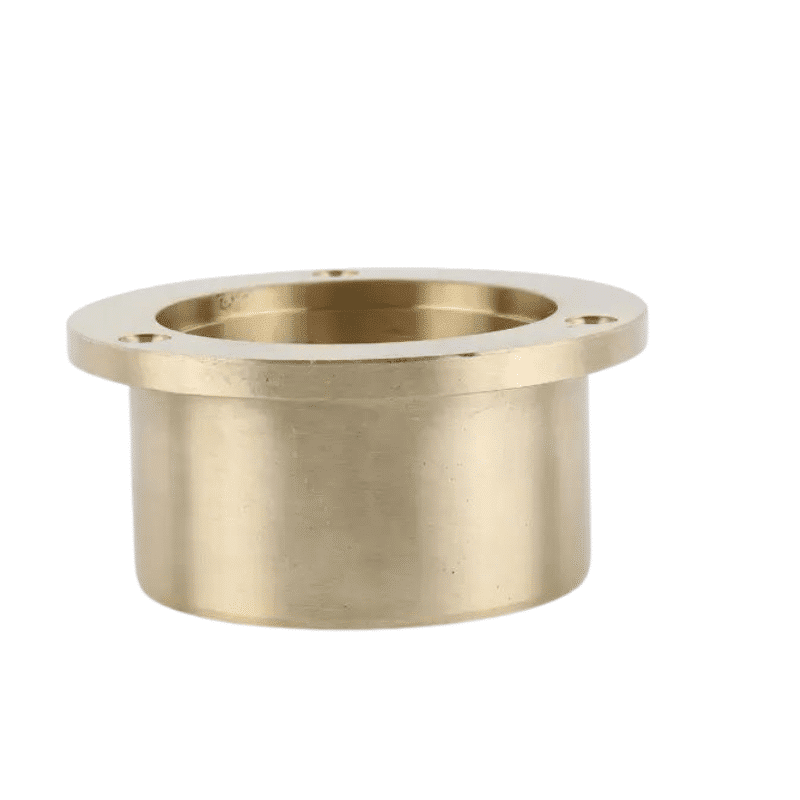
oversized Bronze Bearings, The Centrifugal Casting Process for Large Bronze Bushings, Large Bronze Parts for Machine
specializing in Centrifugal casting Bronze Bushing, oversized Bronze Bearings Part for Cone Crusher
Centrifugal casting is a process that involves pouring molten bronze into a mold which is rapidly rotated. The centrifugal force pushes the molten metal against the mold walls, resulting in a uniform and dense structure with excellent mechanical properties. This method is ideal for manufacturing large bushings due to its ability to produce high-quality, durable parts that are capable of withstanding heavy loads and high friction.
When creating a bushing with a diameter of 3 meters, the process becomes even more specialized. The manufacturing equipment must be able to accommodate the large size, and careful control is needed to ensure the molten bronze is evenly distributed throughout the mold, resulting in a uniformly dense bushing.
Custom Bronze Alloys for Bushing Manufacturing, Bronze Bush for Mining Machinery/Cone Crusher
The choice of bronze alloy can greatly affect the bushing’s final properties, and different applications may require different alloys. Here are a few common alloys used in the manufacture of large bronze bushings:
- Leaded Tin Bronze (C93200): Also known as SAE 660, this alloy is renowned for its excellent wear resistance and machinability. It’s often used in heavy-duty applications where high strength and good lubricity are required.
- Aluminum Bronze (C95400): This alloy has excellent resistance to wear, corrosion, and heat, and offers high strength. It’s suitable for applications with high loads and speeds.
- High Leaded Tin Bronze (C94500): Offering superior machinability and good resistance to wear and corrosion, this alloy is often used for bearings and bushings in low-speed, high-load applications.
- Manganese Bronze (C86300): Known for its high strength, hardness, and heavy load capability, this alloy is used in applications subject to high wear and abrasive conditions.
oversized Bronze Bearing Types and Alloy Selection, Casting Methods for Large Diameter Bronze Bearings
Extra-Large Diameter Bronze Bearings Technical Data for Custom Bronze Bushings, oversized Bronze Parts for Machine
Large Bushings: Achieving Superior Performance under Harsh Conditions
Engineering and manufacturing industries are continually evolving, requiring components that can withstand increasingly severe conditions. In this context, large bushings have emerged as essential players. With an ability to operate under harsh conditions, heavy loads, and yet require no maintenance in standard applications, these bushings are addressing a significant market demand.
The Need for Large Bushings
Whether it’s in the realm of heavy machinery, transport vehicles, construction equipment, or industrial manufacturing systems, there is a growing need for components that can handle extreme stress, intense friction, and substantial weight. Large bushings, with their substantial size and robust construction, are ideally suited to meet these demands.
From supporting heavy structures to ensuring smooth operation of moving parts under intense load, these bushings excel in multiple roles. What sets them apart is their ability to perform consistently without necessitating regular maintenance, thereby enhancing efficiency and minimizing downtime.
Attributes of Large Bushings
Large bushings are engineered with various attributes that enable them to function effectively in challenging scenarios. These features include:
- Robust Material Construction: Large bushings are typically crafted from materials like bronze, stainless steel, or composite materials, known for their high tensile strength, durability, and resistance to wear and tear.
- Self-Lubricating Design: Many large bushings feature self-lubricating properties, significantly reducing maintenance requirements. This feature also allows for smoother operation, minimizes friction and wear, and extends the component’s lifespan.
- Resistance to Harsh Conditions: These bushings are designed to withstand high temperatures, corrosive environments, and other adverse conditions, making them ideal for use in demanding industrial applications.
- High Load Capacity: Given their size and robust construction, large bushings are capable of handling substantial loads, making them integral components in heavy machinery and equipment.
In conclusion, large bushings are fulfilling a critical need in the manufacturing and engineering sectors. By providing superior performance under harsh conditions and heavy loads, while running maintenance-free in standard applications, these components are proving indispensable in a range of industries. The future promises further enhancements in large bushing technology, designed to keep pace with ever-evolving market demands.
The manufacture of large, 3-meter diameter, centrifugal cast bronze bushings is a complex task that demands specialist skills, careful process control, and a deep understanding of bronze alloys. With a broad array of bronze alloys available, each with unique properties, custom manufacturers are well-equipped to produce bushings that meet specific application requirements, ensuring optimal performance, longevity, and efficiency for heavy machinery and industrial equipment.
Each of these bronze alloys has unique mechanical properties. Here’s a simplified comparison:
Alloy | Tensile Strength (MPa) | Yield Strength (MPa) | Hardness (HB) |
---|---|---|---|
C93200 | 220 | 110 | 60 |
C95400 | 620 | 250 | 170 |
C94500 | 240 | 120 | 65 |
C86300 | 758 | 427 | 225 |
Note: These values are typical for each alloy, but they can vary slightly depending on the exact composition and manufacturing process.
Services We Offer
Extra-Large Diameter Bronze Bearings We label any bearing that necessitates an external diameter surpassing our largest standard size, typically 20 inches, as “Extra-Large” or “Large Diameter”. To accommodate these more substantial diameter prerequisites, we provide bespoke solutions employing either the centrifugal or static casting methods. These products can be procured in a rough machined state (with additional material left on all surfaces for your finishing needs), or as a fully machined, ready-to-use part.
Extra-large Bronze Bearings find extensive usage in a diverse array of applications, such as Heavy-duty Construction Machinery, Hydroelectric facilities, Offshore Marine sectors, Nuclear environments, and Machine Repair, to mention a few.
Over time, Cast Bronze Alloys have consistently been the preferred material due to their flexibility in customizing mechanical and physical attributes by simply tweaking the alloying element. An extensive range of alloys is available to cater to the unique requirements of very specific applications.
Applications of Large Diameter Bronze Bearings
Large diameter bronze bearings are used in a variety of heavy-duty applications, including:
- Heavy Duty Construction Equipment: These bearings are commonly used in pivot points in heavy construction machinery such as bulldozers and excavators.
- Hydro-Electric Applications: They are used in turbines and other hydroelectric equipment due to their ability to withstand water exposure.
- Offshore Marine: These bearings, particularly those made from corrosion-resistant alloys, are suitable for offshore applications where saltwater resistance is crucial.
- Nuclear Environments: In nuclear power plants, large diameter bronze bearings are used due to their radiation resistance.
- Machine Repair: They are often used in the repair and replacement of worn-out components in various machinery.
In conclusion, large diameter bronze bearings play a critical role in several industries. By choosing the right casting method, bearing type, and bronze alloy, these bearings can be customized to meet specific application requirements, enhancing the efficiency and durability of the machinery they are used in.
Casting Methods for Large Diameter Bronze Bearings
There are two primary casting methods used in the manufacture of large diameter bronze bearings: static casting and centrifugal casting.
Static Casting: This traditional method involves pouring molten metal into a stationary mold. The metal cools and solidifies to form the bearing. Although static casting is simple and cost-effective, it might not always provide the best mechanical properties for larger bearings.
Centrifugal Casting: In this process, molten bronze is poured into a mold that is rapidly rotated. The centrifugal force drives the molten metal against the mold wall, where it cools and solidifies, resulting in a uniformly dense structure with superior mechanical properties. Centrifugal casting is preferred for large diameter bearings due to its ability to produce high-quality, durable components.
Bearing Types and Alloy Selection
When it comes to the bearing type and alloy selection, these are dictated by the application’s specific needs.
Bearing Types: There are various bearing designs, each suited to different applications. Sleeve bearings, flange bearings, and thrust washers are common types. Large diameter bronze bearings often come as sleeve bearings due to their capability to handle high loads and provide excellent wear resistance.
Alloy Selection: The choice of bronze alloy depends on the desired physical and mechanical properties of the bearing. Some commonly used alloys include leaded tin bronze (C93200), aluminum bronze (C95400), high leaded tin bronze (C94500), and manganese bronze (C86300). Each of these alloys has unique characteristics, making them suitable for specific applications. For example, C95400, with its excellent wear resistance and strength, is great for high-load applications, while C93200 is preferred for its excellent machinability and wear resistance.