High Tensile Brass Bearing, Maintenance-free, self-lubricating, sliding bearings
About us
Type Of Bearing
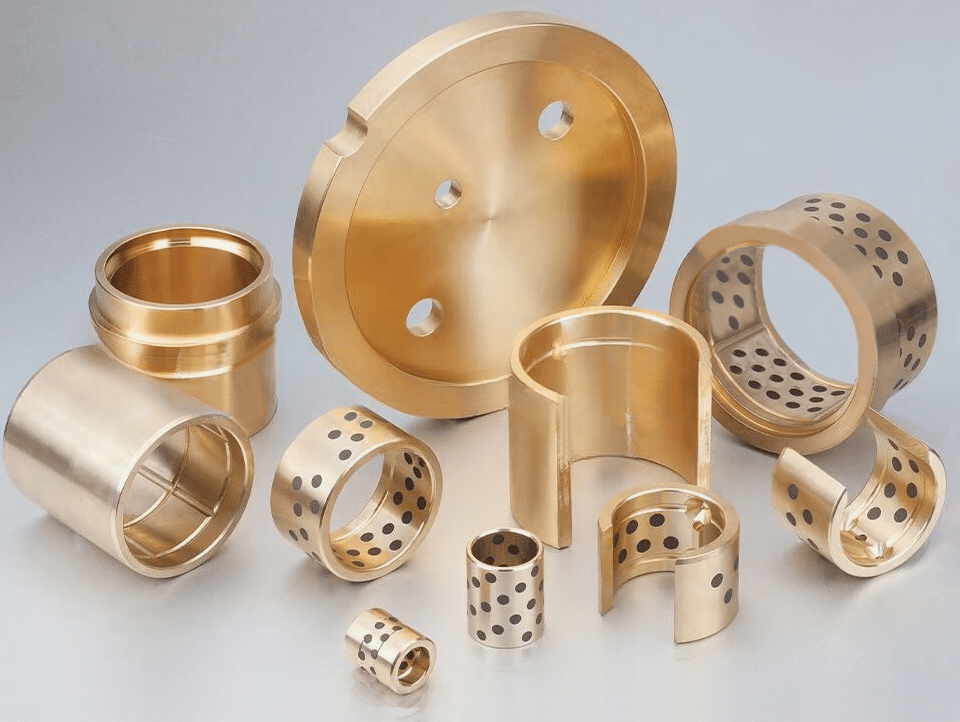
Design Custom Bearings, Custom Parts Manufacturing. Download Our Plain Bearing Brochure
These high tensile brasses are copper and zinc alloys, enriched with small percentages of other metals. We manufacture CuZn25Al5Mn4Fe3 alloys.
The materials comprise durable copper and brass alloys engineered for high wear resistance, featuring sliding surfaces uniformly adorned with “macro-distributed” solid lubricant deposits. It’s crucial to ensure adequate coating of the sliding plugs to facilitate the formation of a stable transfer film, essential for smooth sliding bearing operation, depending on the motion sequence. The high density of the bronze ensures a robust load-bearing capacity while effectively embedding any dirt particles within the lubricant deposits. There are two variants of graphite-based plugs and one PTFE-based plug available. In technical dry operation, graphite bearings are furnished with a 10 to 20 µm thick running-in film, facilitating the transfer of solid lubricant to the counterpart material upon initial contact between the sliding partners.
Self Lubricating Custom parts, Customized High tensile brasses Bearing and Plate
Maintenance-free, self-lubricating sliding bearings: High tensile brasses, such as EN 1982 CuZn25Al5Mn4Fe3, are engineered materials designed to offer superior mechanical properties for demanding applications.
A conventional lubricated bronze material can only develop a separating lubricating film under specific movement conditions and sliding speeds. However, with graphite-plugged lubrication, the sliding material itself provides lubrication. From the outset of sliding, solid lubricant is released through microabrasion, resulting in the creation of smooth surfaces with a firmly adhering film of solid lubricant on the sliding partners. Even under heavy loads, the lubricant persists in the contact zone, ensuring thorough separation of the sliding surfaces and maintaining a consistently low coefficient of friction with minimal wear.
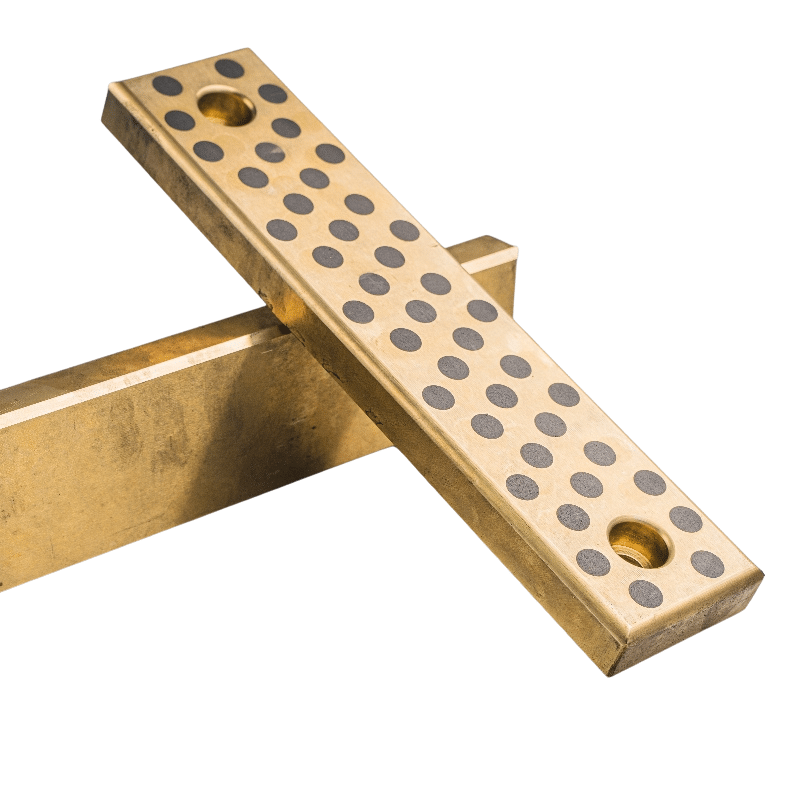
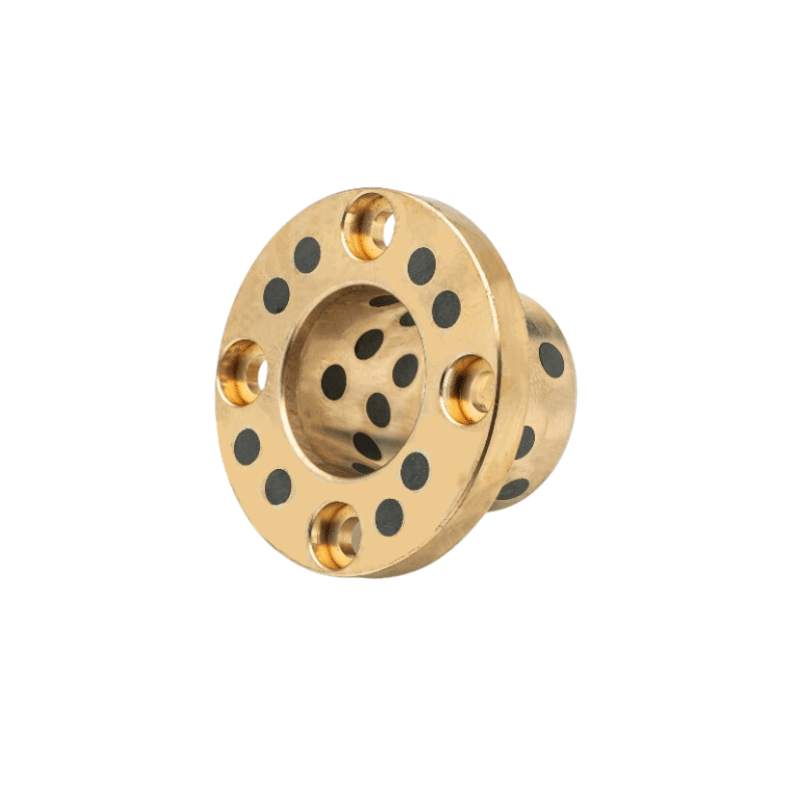
High Tensile Brass Alloy Solid Lubricant Embedded. Metallic High-Tensile Brass Alloy
High tensile brass alloys with solid lubricant embedded are engineered materials designed to provide excellent mechanical properties and wear resistance, particularly for applications involving plain bearings and bushings. This straight and flange specification, which is the most common specification in the copper alloy series, is ideal for high-load, low-speed applications.
Perfect for use in hydroelectric turbines, hydraulic steelwork, and any applications exposed to seawater. Utilizing leaded, corrosion-resistant bronze CuSn7ZnPb7, bronze graphite bearings provide a high-performance solution, leveraging the self-lubricating properties of solid lubricants.
- Plate Bearing
- Cylindrical Bearing
- Flanged Bearing
- Spherical Bearing
- Other Geometries
Custom Parts Services and Prototyping!
Leaded, Phosphor And Aluminium Bronze Bearing, Search Our Material Alloy
Design Custom Parts & Plain Bearings Made From High-Strength Metal
Slide Bearings are a type of plain bearing designed to handle higher loads and are often used in situations where linear motion is required. When manufacturing custom parts, it’s crucial to maintain a high level of communication with the client to ensure that the final product meets their expectations and performs as intended in their specific application. If you have any specific questions about the manufacturing process, materials, or applications of custom parts, plain bearings, or slide bearings, feel free to ask! Customized bearings, bushings and plain bearing designer give you the manufacturing costs of production methods as well.
Main Metal Type
Type | 650 | 650S5 | 650W1 | 650W3 | 650S1 | 650S2 | 650S3 | |
Material | CuZn25AI5Mn4Fe3 high tensile brass | CuSn5Pb5Zn5 bronze bushing | CuAl10Ni5Fe5 bronze bearing | CuSn12 bronze alloy bearing | ||||
Density | 7.8 | 8.9 | 7.8 | 8.9 | ||||
HB Hardness | ≥210 | ≥250 | ≥210 | ≥230 | ≥70 | ≥150 | ≥75 | |
Tensile Strength MPa | ≥750 | ≥800 | ≥755 | ≥755 | ≥250 | ≥500 | ≥270 | |
Yield Strength MPa | ≥450 | ≥450 | ≥400 | ≥400 | ≥90 | ≥260 | ≥150 | |
Elongation % | ≥12 | ≥8 | ≥12 | ≥12 | ≥13 | ≥10 | ≥5 | |
Thermal Expansion Coefficient | 1.9×10*%/°C | 1.8×10*9/°C | 1.6×10^*/°C | 1.8×10*/°C | ||||
Max. Operation Temp. | -40~+250°C | -40~+400°C | ||||||
Max. load MPa | 50 | 75 | 75 | 100 | 50 | |||
Max. speed m/s | Dry | 0.5 | 0.1 | 0.5 | 0.1 | 0.5 | ||
Lubricated | 1 | 0.25 | 1 | 0.25 | 2.5 | |||
Max. PV (N/mm2*m/s) | Dry | 1.65 | 1 | |||||
Lubricated | 3.25 | 1.65 |
The above data is recommended by viiplus. The designing data should be evaluated according to the particular application conditions.
Solid Lubricants
Lubricant | Feature | Typical Applications |
SL1 Graphite + Additives |
Good Chemical resistance and low friction coefficients. Operation temperature up to +400oC |
Suitable for general industry applications exposed to atmosphere. |
SL4 PTFE+MoS2+Additives |
Low friction coefficients and good water lubricating feature. Operation temperature up to +300oC |
Suitable for water lubrication conditions. The applications include vessels, hydraulic turbines and steam turbines. |
Characteristics of High Tensile Brass Alloy with Solid Lubricant Embedded:
- High Tensile Strength: These alloys are formulated to have a high tensile strength, making them suitable for applications where the material is subjected to significant mechanical stress.
- Solid Lubricant: The inclusion of a solid lubricant, such as graphite, molybdenum disulfide (MoS2), or other materials, enhances the self-lubricating properties of the brass alloy. This can reduce friction and wear, especially in situations where traditional lubrication methods are not feasible or where maintenance is minimal.
- Wear Resistance: The combination of a high tensile brass alloy and a solid lubricant results in a material that is highly resistant to wear, which is critical for the longevity and performance of bearings and bushings.
- Corrosion Resistance: Brass alloys generally have good corrosion resistance, which can be further improved by the addition of specific elements or treatments.
- Low Maintenance: Due to their self-lubricating nature, these materials can operate with minimal maintenance, making them ideal for applications where regular lubrication is difficult or undesirable.
- Applications: These alloys are used in a variety of applications, including:
- Plain bearings in automotive and industrial machinery
- Bushings for various mechanical components
- Wear plates and guides in machinery
- Components in environments with limited access for lubrication
Manufacturing Process:
The manufacturing process for these alloys typically involves the following steps:
- Alloy Preparation: The base brass alloy is prepared with the desired composition, including elements that contribute to its high tensile strength.
- Lubricant Addition: The solid lubricant is then added to the molten alloy. This can be done through various methods, such as powder metallurgy, where the lubricant is mixed with the alloy powder before compaction and sintering.
- Compaction: The mixture is compacted, often using high pressure, to form a solid billet or preform.
- Sintering: The compacted material is then sintered at high temperatures to achieve the desired properties, including strength and hardness.
- Machining: The sintered material is machined into the final component, such as a bearing bushing.
- Finishing: The final components may undergo additional finishing processes, such as polishing or heat treatment, to achieve the desired surface finish and mechanical properties.
Standards and Specifications:
While you mentioned the ASTM B505 C86300 standard, it’s important to note that this standard specifically refers to a high-lead brass alloy. For high tensile brass alloys with embedded solid lubricants, there may not be a direct equivalent standard, as these are specialized materials. However, manufacturers and engineers will often develop their own specifications or follow general guidelines for bearing materials to ensure the materials meet the required performance criteria.
When specifying these materials, it’s crucial to work closely with suppliers and material scientists to ensure that the final product meets the specific requirements of the application in terms of strength, wear resistance, and lubrication.
Characteristics of EN 1982 CuZn25Al5Mn4Fe3:
- Composition: This high tensile brass is composed of:
- 25% Zinc (Zn)
- Up to 5% Aluminum (Al)
- Up to 4% Manganese (Mn)
- Up to 3% Iron (Fe)
- Balance of Copper (Cu)
- Hardness: The high percentage of zinc, along with the addition of aluminum, manganese, and iron, contributes to the material’s hardness. This makes it an excellent choice for applications where high wear resistance is required.
- Strength: The alloy’s strength is enhanced by the presence of aluminum and manganese, which form hard intermetallic compounds within the brass matrix.
- Corrosion Resistance: While brass is generally resistant to corrosion, the addition of aluminum can further improve this property, although it may be somewhat reduced due to the presence of iron.
- Machinability: High tensile brasses can be more challenging to machine than softer brasses due to their hardness, but they still offer good workability with the right tools and techniques.
- Applications: Given its hardness and strength, EN 1982 CuZn25Al5Mn4Fe3 is well-suited for machine elements that are subjected to high mechanical stress, such as gears, bushings, and bearings in heavy-duty machinery.
International Standard – ASTM B505 C86300:
The ASTM B505 C86300 is an international standard that specifies the requirements for copper and copper alloy bearing materials. The C86300 designation within this standard refers to a high-strength, high-lead brass alloy (with approximately 3% lead content) that is known for its excellent bearing properties and machinability.
While EN 1982 CuZn25Al5Mn4Fe3 and ASTM B505 C86300 both fall under the category of high-strength brass alloys suitable for bearing applications, they have different compositions and properties. The EN 1982 alloy is known for its high tensile strength due to the inclusion of aluminum and manganese, whereas the ASTM B505 C86300 alloy is a high-lead brass, which provides good bearing properties due to the presence of lead.
When selecting a material for a specific application, it’s crucial to consider the specific requirements of that application, such as the need for hardness, strength, corrosion resistance, and machinability. Both standards provide high-quality options for bearing materials, but the choice between them would depend on the precise demands of the application in question.
Providing Brass, Bronze, and Specialty Copper Alloys, Copper Alloy Machining Services