Cast Bronze Bushings
Bearings and Bushings for the Future: Precision and Customization: Our company, in bearing engineering with decades of experience, designs and develops high-precision self-lubricating bronze bearings & plain bushes. We offer a wide array of sliding bearings tailored to meet specific needs. Renowned for our expertise in custom bronze bushing and slide plate solutions, we provide an expansive selection of bushing metal alloys. Contact us today to benefit from unparalleled services at competitive prices.
Cast Bronze Bushings
Leaded, Phosphor And Aluminium Bronzes Plates and Bearing,
Wear Plates – Mold and Die Products, Search Our Material Alloy
Composites and Metallic Bearings, Bushing Manufacturing,
Cast Bronze Metric Bearings and Bushings
Custom Cast Bronze Bearing solutions for your engineering needs, Metric Cast Bronze – Bushings
CDA 932 or SAE 660 cast bronze sleeve bearings are manufactured from continuous cast bronze, ensuring a uniform composition throughout the bearing. This method significantly minimizes the risk of porosity and other defects commonly associated with other casting techniques. Cast copper bushings are indispensable components in industrial applications. Through the use of various copper alloy materials and custom designs, they can meet a wide range of performance requirements and operating environments. Centrifugal and continuous casting techniques make the production of copper bushings more efficient and precise, while the capability for rapid manufacturing of custom designs ensures that specific customer needs are quickly met. Global slide bearing technology supplier and premier provider of customized, high-precision bearing solutions for: We produce super-precision bearings, bushing and specialty bearing units using state of the art production techniques. Our customers value our broad application expertise and technical cooperation, especially during the design phase. Based on short development times, they receive solutions that are economically attractive precisely fitted to technical requirements.
Cast Bronze
“The High Quality Cast Bronze Bushing at the Low Cost!”
Custom solutions for your engineering needs.
Standard Cast Bronze Bearings – Bronze Standards.
To find the specific Cast Bronze product you require, simply click on the corresponding small product image located in the right column. Our range includes sleeves, flanges, thrust washers, and wear plates (where available). Our products are made from high-quality Cast Bronze SAE 660 / CDA 932, and come with a broad array of additional capabilities. As a recognized OEM and producer of subassemblies, components, and parts, we are committed to continuous innovation in our materials, processes, and solutions. We develop highly-engineered products tailored for customers across diverse industries where the performance of the product is crucial. We are a globally recognized leader in designing and manufacturing bearings and bushings, dedicated to excellence in every aspect of our business.
Chemical Requirements | ||||||||||||
Copper Alloy UNS No. |
Composition, % max, except as indicated | |||||||||||
Nickel | ||||||||||||
Copper | Tin | Lead | Zinc | Iron | Including | Aluminum | Manganese | Antimony | Sulfur | Phosphorus | Silicon | |
Cobalt | ||||||||||||
C86300 | 60.0–66.0 | 0.20 | 0.20 | 22.0–28.0 | 2.0–4.0 | 1.0A | 5.0–7.5 | 2.5–5.0 | … | … | … | … |
C90500 | 86.0–89.0 | 9.0–11.0 | 0.30 | 1.0–3.0 | 0.20 | 1.0A | 0.005 | … | 0.20 | 0.05 | 0.05B | 0.005 |
C91100 | 82.0–85.0 | 15.0–17.0 | 0.25 | 0.25 | 0.25 | 0.50A | 0.005 | … | 0.20 | 0.05 | 1.0B | 0.005 |
C91300 | 79.0–82.0 | 18.0–20.0 | 0.25 | 0.25 | 0.25 | 0.50A | 0.005 | … | 0.20 | 0.05 | 1.0B | 0.005 |
C93700 | 78.0–82.0 | 9.0–11.0 | 8.0–11.0 | 0.8 | 0.7C | 0.50A | 0.005 | … | 0.50 | 0.08 | 0.10B | 0.005 |
A In determining copper minimum, copper may be calculated as copper plus nickel. | ||||||||||||
B For continuous castings, phosphorus shall be 1.5 % max. | ||||||||||||
C Iron shall be 0.35 % max. when used for steel-backed. |
High Precision Self-Lubricating Bearings
Trusted & reliable self-lubricating bearings supplier
Trusted handyman services
Self-lubricating bearing- Check out the variety of configurable, Bushing with flange – Self-lubricated Composite bushing, Plain Bearing,Thrust Washer ( Graphite Embedded) & Self Lubricating Bushes, has other mechanical components, custom size strip available. Self-Lubricating Bearings are renowned worldwide for an unbeatable reputation of quality and innovation.
Cast Bronze Solutions That Drive Innovation
Experience and Expertise in the Design of Cast Bearings and Engineered Bushings
Advancing Precision in Slide Bearing Technologies. Tackling Complex Challenges Through Innovation: We design and manufacture top-performing bearings and engineered products by harnessing custom engineering to develop solutions for the most demanding applications across various industries. Whether your needs lie in mining, medical devices, hydropower, or heavy industry, our extensive experience and deep knowledge enable us to create highly engineered solutions for your most challenging issues.
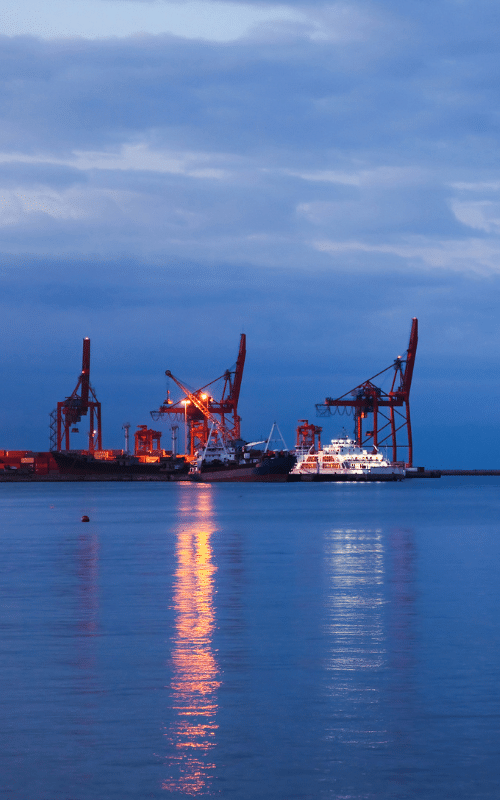
Solutions For Every Industry
Searching for Dependable Bushing Solutions? viiplus Has What You Need.
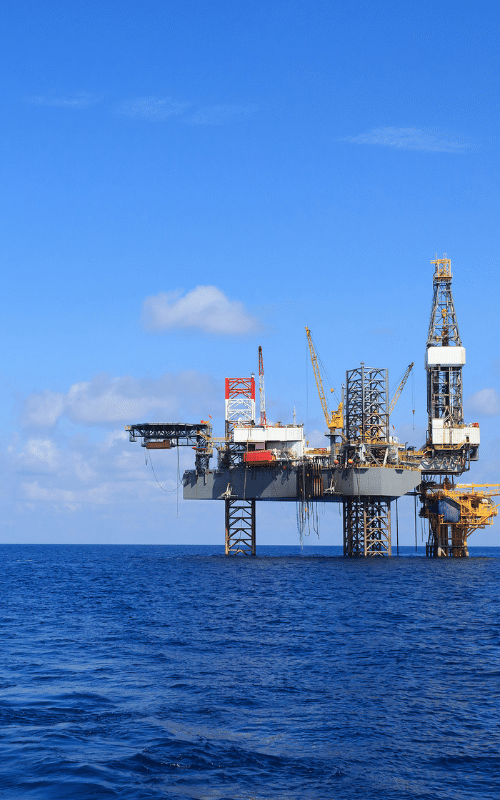
Design Guides, Materials
Bushing design, Comprehensive design manuals covering a range of self-lubricating materials used in all of viiplus’s manufacturing processes.
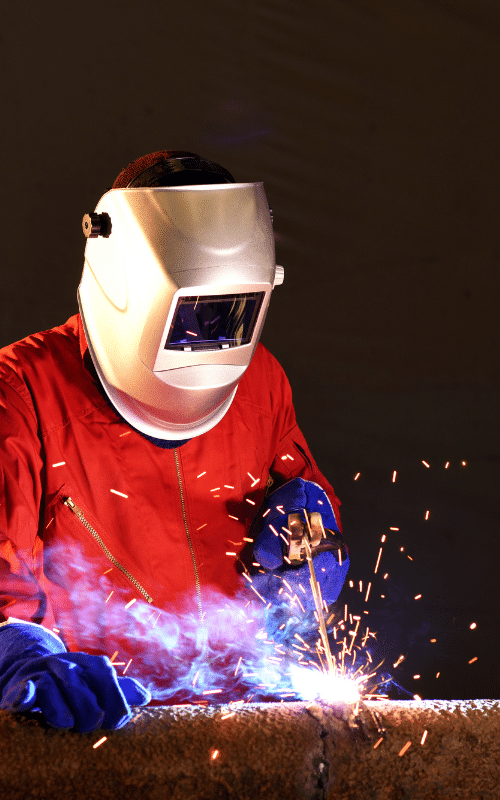
Technical Guides
Manufacturing On Demand, Technical Guides For Machining Design. Discover the latest in metal alloys, materials, and design tips for manufacturing custom machined and self-lubricating bearing parts.
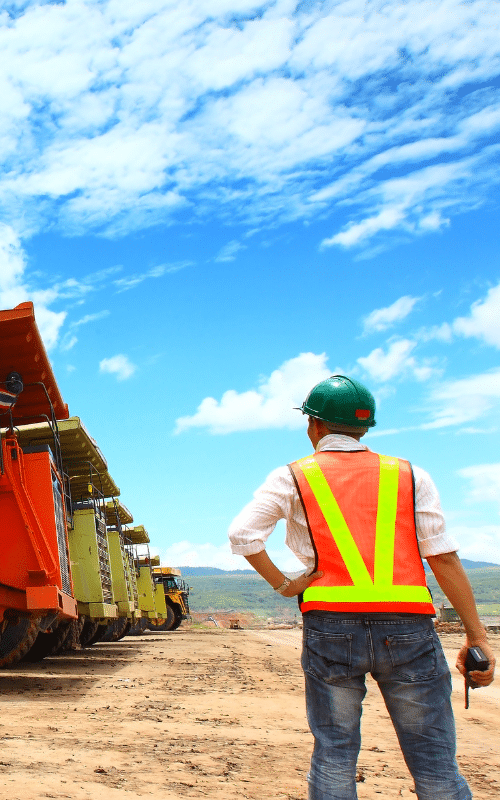
Get Instant Quote
To receive your instant quote, simply upload your drawing file and choose your production process & bushing material.
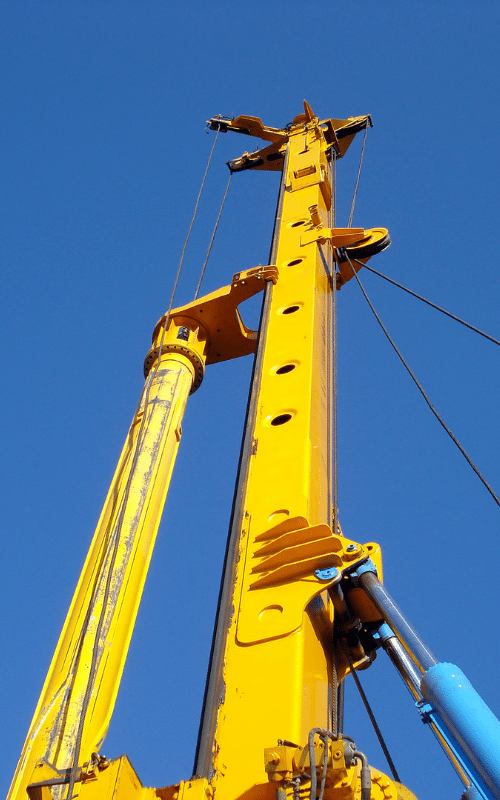
Prototyping, Place Order
After you place your order, we will start the production process. You will receive updates when your order has completed production and is ready to be dispatched.
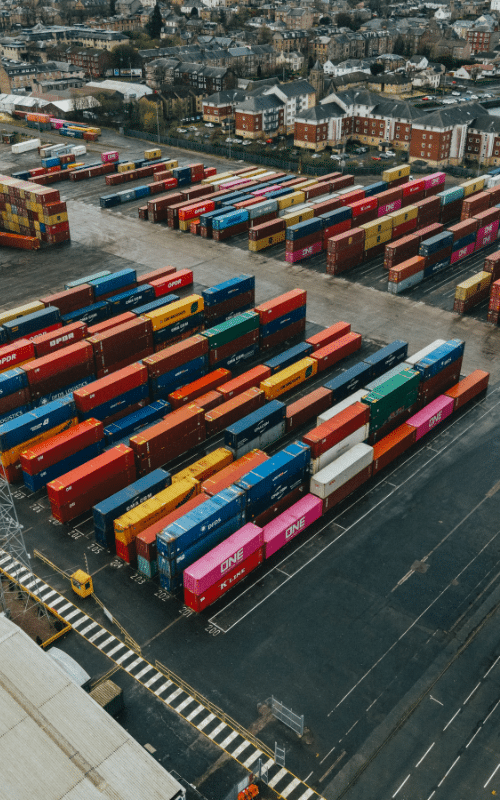
Receive Your custom Parts
We provide precision-inspected high-quality parts, packing lists and documents, and delivery tracking.