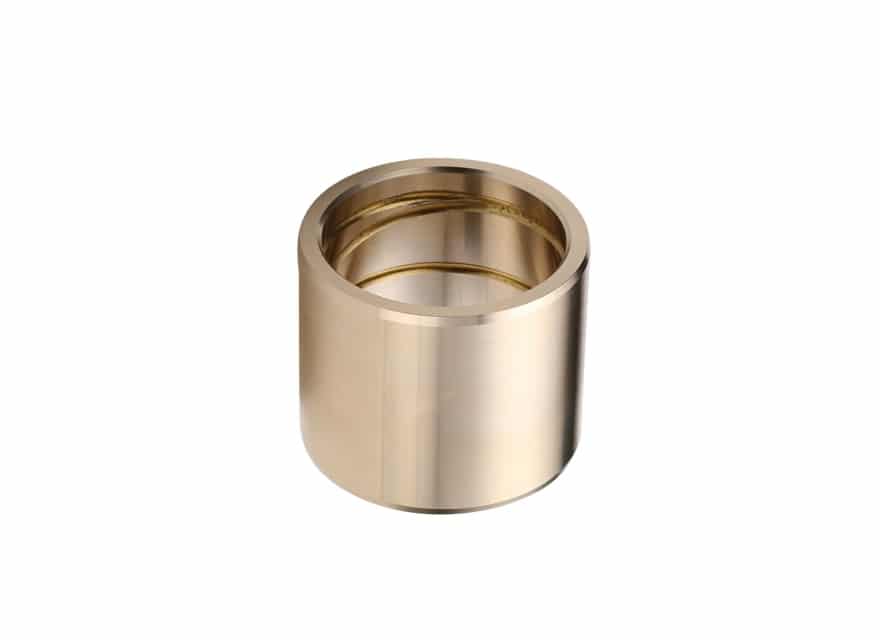
Custom Bushing Suppliers
Order custom-bearing bushings for your specific industrial application needs from experienced manufacturers. When it comes to industrial applications, choosing the right bearing bushings is critical to the success and longevity of the equipment. Custom bearing bushings can be designed and manufactured to meet the specific requirements of your application. Experienced manufacturers can provide high-quality custom bearing bushings that meet or exceed industry standards.
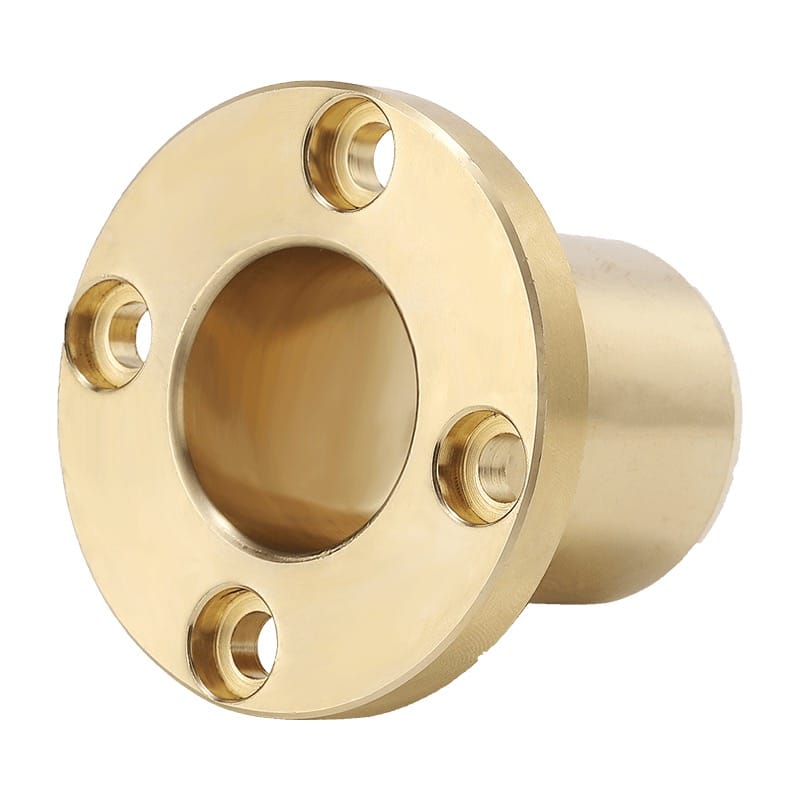
Bushing material, Understanding C93200 Material Properties
Cannabis for a better life
Find out about different bushing materials, including C93200, and learn which materials are best for different applications.
What Are the Best Bushing Materials?
Discover best practices for maintaining C93200 bushings to prevent wear, damage, and failure in industrial applications. ordering custom-bearing bushings from experienced manufacturers can provide several benefits for your industrial applications, including tailored design, high-quality materials, cost-effectiveness, expert guidance, and timely delivery. Contact a reputable manufacturer today to discuss your specific needs and requirements.
Top C93200 Bushing Suppliers
Get Custom C93200 Bushings
Choosing the Right Bushing Manufacturer
Lubricating C93200 Bushings for Optimal Performance
Benefits of Self-Lubricating Bushings
Beautifully crafted leather products.
self-lubricating bushings offer several benefits in industrial applications, including reduced maintenance, cost-effectiveness, improved performance, increased reliability, environmental benefits, and versatility. Choosing the appropriate material for self-lubricating bushings can help to ensure optimal performance and longevity of industrial equipment and machinery. Learn how self-lubricating bushings, including C93200, can reduce friction, noise, and wear in various industrial applications. Selecting the right bushing material is crucial for the success and longevity of a particular application. Factors such as load, speed, temperature, and environmental conditions should be taken into account when choosing the appropriate material. C93200 bronze is a commonly used material, but steel, polyurethane, nylon, and Polytetrafluoroethylene are also popular choices for specific applications.
The Advantages of Flanged Bushings
Discover the advantages of using flanged bushings, including C93200, in different industrial applications.
Flanged bushings are commonly used in industrial applications to provide support and reduce friction between two parts. They have a flange that provides additional support and helps to prevent axial movement of the bushing. C93200 bronze is a popular material used for flanged bushings due to its high strength, wear resistance, and corrosion resistance. flanged bushings offer several advantages in industrial applications, including reduced wear, increased stability, easy installation, cost-effectiveness, and versatility. C93200 bronze is a popular material used for flanged bushings due to its high strength and wear resistance, but other materials can also be used depending on the specific application requirements.
Choosing the Right Plain Bushing
Plain bushings are commonly used in industrial applications to provide support and reduce friction between two parts. Choosing the right plain bushing is critical to the success and longevity of the equipment.
Bushing materials are used in a variety of applications, such as automobiles, aerospace, construction equipment, and industrial machinery, to provide support and reduce friction between two parts. Different materials are used for bushings depending on the specific application, load, speed, and environmental conditions. One common bushing material is C93200, also known as SAE 660 or bronze.
C93200 bronze is a high-strength, leaded-tin bronze alloy that is often used in heavy-duty applications where high load and low speed are present. It has good wear resistance, high corrosion resistance, and excellent machinability. C93200 bronze is commonly used in bearings, pumps, valves, and other applications where low friction is required.
Learn about the features and applications of plain bushings, including C93200, and how to choose the right one for your needs. Discover the top suppliers of C93200 bushings and get a competitive quote for your replacement part needs.
Browse Bushing Lubrication…
Order custom C93200 bushings for your specific industrial application needs from experienced manufacturers. Learn how to lubricate C93200 bushings to optimize their performance and extend their lifespan. Selecting the best bushing material depends on the specific application requirements. Bronze, steel, pom, ptfe, Polytetrafluoroethylene, graphite, and are some of the best bushing materials for different applications, based on their strength, wear resistance, corrosion resistance, self-lubricating properties, and high-temperature resistance. It is important to consult with a professional to determine the best material for your specific application.
Understanding C93200 Material Properties, Learn about the properties of C93200 material and how it can be used in bushings. Discover its benefits and limitations.
C93200 is a high-strength bronze alloy that is commonly used in bushings and other industrial applications. Here are some of the properties of C93200 and how it can be used in bushings:
- High strength: C93200 has high strength and can withstand heavy loads and high pressures. It is commonly used in heavy-duty applications where high load and low speed are present.
- Good wear resistance: C93200 has good wear resistance and can withstand friction and wear over time. This makes it ideal for use in bushings, which are designed to reduce friction between two parts.
- High corrosion resistance: C93200 has high corrosion resistance and can withstand exposure to harsh environments, such as saltwater and chemicals. This makes it ideal for use in marine and chemical applications.
- Excellent machinability: C93200 has excellent machinability, making it easy to manufacture and shape into complex parts.
- Self-lubricating: C93200 has self-lubricating properties, which can reduce the need for external lubrication in certain applications.
C93200 is a popular material used in bushings due to its high strength, wear resistance, corrosion resistance, excellent machinability, and self-lubricating properties. However, it is important to consider its limitations, such as low-speed limitations and limited temperature range, when selecting the appropriate material for a specific application. Consult with a professional to determine if C93200 is the best material for your bushing application.
Lubricating C93200 Bushings for Optimal Performance Learn how to lubricate C93200 bushings to optimize their performance and extend their lifespan.
C93200 bushings are known for their self-lubricating properties, which reduce the need for external lubrication. However, in some applications, external lubrication may be necessary to optimize their performance and extend their lifespan. Here are some tips for lubricating C93200 bushings for optimal performance:
- Choose the right lubricant: The lubricant used for C93200 bushings should be compatible with the material and application requirements. Some lubricants may react negatively with the material, causing corrosion or other issues. Consult with a professional to determine the best lubricant for your specific application.
- Apply lubricant regularly: If external lubrication is necessary, the lubricant should be applied regularly to ensure optimal performance. The frequency of lubrication depends on the application requirements, such as load, speed, and temperature.
- Use the correct application method: The lubricant should be applied using the correct method to ensure even distribution and avoid over-lubrication. Consult with a professional to determine the best application method for your specific application.
- Monitor performance: Regularly monitor the performance of the bushing to ensure that the lubrication is effective and to detect any issues early on. If the bushing shows signs of wear or reduced performance, it may need to be replaced or re-lubricated.
- Clean the bushing before lubrication: Before applying lubricant, it is important to clean the bushing to remove any dirt, debris, or old lubricant. This ensures that the lubricant can be applied evenly and effectively.
Lubricating C93200 bushings can optimize their performance and extend their lifespan. It is important to choose the right lubricant, apply it regularly using the correct method, monitor performance, clean the bushing before lubrication, and consult with a professional to determine the best lubrication strategy for your specific application.
Bushing material, What Are the Best Bushing Materials? Find out about different bushing materials, including C93200, and learn which materials are best for different applications.
Bushing materials are selected based on the specific application requirements, such as load, speed, temperature, and environmental conditions. The following are some of the best bushing materials for different applications:
- Bronze: Bronze is a popular material for bushings because it is strong, durable, and has good wear resistance. C93200 bronze, also known as SAE 660 or bronze, is a common choice for heavy-duty applications with high load and low speed.
- Steel: Steel bushings are strong and can withstand high loads and temperatures. They are commonly used in heavy-duty applications, such as construction equipment, industrial machinery, and engines.
- Polyurethane: Polyurethane bushings have excellent resistance to wear, tear, and corrosion. They are commonly used in automotive suspension systems, where they provide improved handling and stability.
- Nylon: Nylon bushings are lightweight and have good resistance to wear and corrosion. They are commonly used in electrical and electronic equipment, as well as in the automotive industry.
- PTFE: PTFE bushings have low friction and excellent resistance to chemicals and heat.
- Graphite: Graphite bushings have excellent self-lubricating properties, reducing the need for external lubrication. They are commonly used in high-temperature applications.
- Ceramic: Ceramic bushings are highly resistant to wear, corrosion, and heat. They are commonly used in applications that require high accuracy and precision, such as medical and scientific equipment.
In conclusion, selecting the best bushing material depends on the specific application requirements. Bronze, steel, polyurethane, nylon, PTFE, graphite, and ceramic are some of the best bushing materials for different applications, based on their strength, wear resistance, corrosion resistance, self-lubricating properties, and high-temperature resistance. It is important to consult with a professional to determine the best material for your specific application.
Benefits of Self-Lubricating Bushings Learn how self-lubricating bushings, including C93200, can reduce friction, noise, and wear in various industrial applications.
Self-lubricating bushings are a type of bushing that do not require external lubrication. They are designed to operate with low friction, reducing wear and increasing the lifespan of the bushing and the parts it supports. Some benefits of self-lubricating bushings include:
- Reduced maintenance: Self-lubricating bushings require little to no maintenance, reducing downtime and increasing productivity.
- Cost-effective: Self-lubricating bushings can be more cost-effective than traditional bushings because they eliminate the need for external lubrication and the associated maintenance costs.
- Improved performance: Self-lubricating bushings can improve the performance of industrial equipment and machinery by reducing friction and wear, resulting in smoother operation and longer lifespan of the parts.
- Increased reliability: Self-lubricating bushings can increase the reliability of equipment and machinery by reducing the risk of failure due to lack of lubrication.
- Environmental benefits: Self-lubricating bushings can be more environmentally friendly than traditional bushings because they eliminate the need for external lubricants, which can be harmful to the environment.
- Versatility: Self-lubricating bushings can be used in a wide range of applications, including automotive, aerospace, and industrial machinery.
In addition to C93200 bronze, other materials can be used for self-lubricating bushings depending on the specific application requirements. Some popular materials include steel, polyurethane, and nylon.
Self-lubricating bushings reduce friction, noise, and wear in various industrial applications, leading to increased productivity and cost savings. By eliminating the need for external lubrication, self-lubricating bushings can also be more environmentally friendly than traditional bushings.
Design and Usage Flanged bushing Informational The Advantages of Flanged Bushings Discover the advantages of using flanged bushings, including C93200, in different industrial applications.
Flanged bushings are a type of bushing that have a flange on one end, which provides additional support and stability. Here are some advantages of using flanged bushings, including C93200, in different industrial applications:
- Increased stability: Flanged bushings provide increased stability to the equipment, as the flange prevents lateral movement of the bushing.
- Easy installation: Flanged bushings are easy to install and remove, as they can be inserted and removed from the equipment without the need for additional components.
- Reduced vibration: Flanged bushings can reduce vibration in equipment by providing additional support and stability to the parts.
- Cost-effective: Flanged bushings can be more cost-effective than traditional bushings because they eliminate the need for additional support components.
- Improved durability: Flanged bushings can improve the durability of the equipment by reducing wear and tear on the parts.
- Customizable: Flanged bushings can be customized to meet the specific application requirements, such as load, speed, and temperature.
C93200 bronze is a common material used in flanged bushings due to its high strength, wear resistance, and self-lubricating properties. Flanged bushings made of C93200 bronze can be used in various industrial applications, such as construction equipment, industrial machinery, and engines.
In conclusion, using flanged bushings, including C93200, can provide several advantages in industrial applications, such as increased stability, easy installation, reduced vibration, cost-effectiveness, improved durability, and customizability. Consult with a professional to determine if flanged bushings are the best solution for your specific application.
Flanged Bushings: What They Are and How They Work Understand the unique design and function of flanged bushings and how they can solve specific engineering challenges.
Flanged bushings are mechanical components used to reduce friction and wear between two moving parts. They are designed with a cylindrical shape and a flange at one end to provide additional support and stability.
Flanged bushings work by creating a thin layer of lubrication between the bushing and the shaft or housing it is installed in. This lubrication reduces friction and wear, which helps to increase the lifespan of both the bushing and the mating parts it is installed in.
The flange on the bushing serves several functions. First, it helps to prevent axial movement of the bushing by providing a surface for the mating part to rest against. This is particularly useful in applications where there is a significant amount of axial load or where the bushing is subjected to vibration.
Second, the flange helps to distribute the load over a larger surface area. This reduces the stress on the mating parts and helps to prevent damage or wear over time.
Finally, the flange can act as a guide for the mating part, helping to ensure that it remains properly aligned and centered with the bushing.
Flanged bushings are commonly used in a variety of industrial applications, including automotive, aerospace, and manufacturing. They are available in a range of sizes and materials to suit different applications and operating conditions.
Overall, flanged bushings are a versatile and effective solution for reducing friction and wear in mechanical systems. Their unique design and functionality make them an essential component in many engineering applications.
The Benefits of Cylindrical Bushings in Machinery Learn how cylindrical bushings can help reduce friction, wear, and noise in rotating parts of machines and equipment.
Cylindrical bushings are mechanical components that are used in machinery to reduce friction, wear, and noise in rotating parts. They are designed as a cylinder-shaped sleeve that fits around a shaft and is usually made of a low-friction material such as bronze, plastic, or composite.
One of the main benefits of cylindrical bushings is that they provide a layer of lubrication between the shaft and the surrounding component, which reduces friction and wear. This helps to extend the lifespan of the machinery by preventing premature failure of the rotating parts due to excessive wear.
In addition to reducing friction and wear, cylindrical bushings can also help to reduce noise in rotating machinery. The layer of lubrication provided by the bushing helps to dampen vibrations and reduce the amount of noise produced by the rotating parts.
Another benefit of cylindrical bushings is their versatility. They can be used in a wide range of machinery and equipment, including engines, transmissions, pumps, and motors. They are also available in different materials and sizes, making it easy to find the right bushing for a particular application.
Cylindrical bushings are also relatively easy to install and maintain. They can be replaced quickly and easily, without the need for specialized tools or equipment. This makes it easy to keep machinery running smoothly and prevent downtime due to bushing failure.
Cylindrical bushings are an important component in many types of machinery and equipment. Their ability to reduce friction, wear, and noise make them a cost-effective solution for extending the lifespan of rotating parts and keeping machinery running smoothly.
C93200 bronze cylindrical bushings
C93200 bronze cylindrical bushings are a type of cylindrical bushing made from a specific alloy of bronze. This particular type of bronze is known for its high strength, excellent wear resistance, and good corrosion resistance, making it a popular choice for use in machinery and equipment.
C93200 bronze is also commonly referred to as “bearing bronze” due to its suitability for use in bearings and bushings. This type of bronze contains a high percentage of copper, as well as smaller amounts of tin and zinc. These alloys work together to create a material that is strong, durable, and resistant to wear.
C93200 bronze cylindrical bushings are designed to provide a low-friction surface between two moving parts, which helps to reduce wear and extend the lifespan of the machinery. They are commonly used in high-load applications, such as in heavy machinery, marine equipment, and automotive engines.
One of the main benefits of using C93200 bronze cylindrical bushings is their ability to handle high loads and withstand harsh environments. The material is able to resist corrosion and wear even when exposed to moisture, heat, and other environmental factors.
Another benefit of using C93200 bronze cylindrical bushings is their ease of installation and maintenance. They can be easily replaced when necessary, without the need for specialized tools or equipment.
Overall, C93200 bronze cylindrical bushings are a reliable and cost-effective solution for reducing friction and wear in machinery and equipment. Their high strength and wear resistance make them suitable for use in a variety of applications, while their ease of installation and maintenance make them a convenient choice for machine operators and maintenance professionals.
Choosing the Right Plain Bushing Learn about the features and applications of plain bushings, including C93200, and how to choose the right one for your needs.
Plain bushings, also known as sleeve bearings, are a type of bearing used to reduce friction between two parts. They consist of a cylindrical metal sleeve with an inner diameter that matches the shaft diameter, and an outer diameter that matches the housing bore. Here are some features and applications of plain bushings, including C93200, and how to choose the right one for your needs:
Features and Applications:
- C93200 bronze is a popular material used in plain bushings due to its high strength, wear resistance, and self-lubricating properties.
- Plain bushings are used in a wide range of industrial applications, such as automotive, aerospace, construction equipment, and industrial machinery.
- Plain bushings are designed to operate with low friction, reducing wear and increasing the lifespan of the bushing and the parts it supports.
- Plain bushings can be self-lubricating, reducing the need for external lubrication and maintenance.
Choosing the Right Plain Bushing:
- Load: The bushing should be designed to handle the load of the application. The load can be static or dynamic, and the bushing should be able to handle both.
- Speed: The speed of the application can affect the performance of the bushing. If the speed is high, a bushing with a low coefficient of friction should be used.
- Temperature: The temperature of the application can affect the performance of the bushing. If the temperature is high, a bushing that can withstand high temperatures should be used.
- Environmental conditions: The environmental conditions of the application can affect the performance of the bushing. If the environment is corrosive, a bushing that can resist corrosion should be used.
- Material: The material of the bushing should be selected based on the specific application requirements. C93200 bronze, steel, polyurethane, nylon, PTFE, graphite, and ceramic are some of the best bushing materials for different applications.
- Lubrication: The lubrication requirements of the bushing should be considered when selecting the right bushing. Some bushings are self-lubricating, while others require external lubrication.
- Size and dimensions: The size and dimensions of the bushing should be selected to fit the application and the parts it supports.
Choosing the right plain bushing, including C93200, depends on several factors, including load, speed, temperature, environmental conditions, material, lubrication, and size and dimensions. Consult with a professional to determine the best bushing for your specific application to ensure optimal performance and longevity of your equipment.
C93200 bushings that can provide competitive quotes for replacement part needs
- viiplus supplier of bronze bushings, including C93200 bronze. They offer a wide range of sizes and configurations to meet the specific needs of various applications.
- viiplus supplier of bronze bushings, including C93200 bronze. They offer custom machining and fabrication services to meet the specific requirements of customers.
- viiplus supplier of bronze bushings, including C93200 bronze. They offer a wide range of sizes and configurations, as well as custom machining and fabrication services.
- viiplus supplier of bronze bushings, including C93200 bronze. They offer a wide range of sizes and configurations to meet the specific needs of various applications.
- viiplus supplier of bronze bushings, including C93200 bronze. They offer a wide range of sizes and configurations, as well as custom machining and fabrication services.
When choosing a supplier for C93200 bushings, it is important to consider factors such as the supplier’s experience, reputation, and customer service. It is also important to compare pricing and lead times to ensure the best value for your replacement part needs.
Get Custom C93200 Bushings Order custom C93200 bushings for your specific industrial application needs from experienced manufacturers.
If you require C93200 bushings that are specifically tailored to your industrial application needs, ordering custom bushings from experienced manufacturers may be the best option. Here are some benefits of ordering custom C93200 bushings:
- Tailored to specific needs: Custom C93200 bushings can be designed and manufactured to meet the specific requirements of your industrial application, such as load, speed, temperature, and environmental conditions.
- Improved performance: Custom C93200 bushings can improve the performance of your equipment and machinery by providing optimal support and reducing friction and wear.
- Longevity: Custom C93200 bushings can be designed and manufactured to withstand heavy loads and harsh environments, increasing the lifespan of your equipment.
- Cost-effective: Ordering custom C93200 bushings can be more cost-effective than purchasing off-the-shelf bushings, as you only pay for what you need.
- Experienced manufacturers: Experienced manufacturers can provide guidance and support throughout the design and manufacturing process, ensuring the best possible outcome for your specific needs.
When ordering custom C93200 bushings, it is important to work with a reputable manufacturer with experience in designing and manufacturing custom bushings. The manufacturer should be able to provide guidance on material selection, design, and manufacturing processes to ensure the best possible outcome for your application needs.
Choosing the right bushing manufacturer is crucial for ensuring that you receive high-quality bushings that meet the specific requirements of your industrial application. Here are some factors to consider when selecting a bushing manufacturer, including C93200:
- Expertise in your specific industrial application: Look for a manufacturer that has experience designing and manufacturing bushings for your specific industry and application. This ensures that the manufacturer has a deep understanding of the requirements and challenges of your application and can provide the most suitable bushing solution.
- Quality assurance: Choose a manufacturer that has a rigorous quality assurance process in place, including testing and inspection procedures. This ensures that the bushings meet industry standards and are free of defects.
- Material expertise: If you are looking for C93200 bushings or any other specific material, look for a manufacturer with expertise in that material. They should be able to provide guidance on material selection, machining, and finishing processes to ensure the best possible outcome for your application needs.
- Customization: Look for a manufacturer that offers customization options for bushings to meet the specific needs of your application.
- Customer service: Choose a manufacturer that provides excellent customer service, including responsive communication, timely delivery, and technical support.
- Competitive pricing: Compare pricing from multiple manufacturers to ensure that you receive a competitive quote for your bushing needs.
Choosing the right bushing manufacturer for your C93200 bushing needs or any other material requires careful consideration of their expertise in your specific industrial application, quality assurance, material expertise, customization options, customer service, and pricing. It is important to work with a reputable manufacturer that can provide guidance and support throughout the design and manufacturing process to ensure the best possible outcome for your application needs.
A Comprehensive Guide to Bronze Bushings Learn about the properties, uses, and benefits of bronze bushings in various industries.
Bronze bushings are essential components used in various industries to reduce friction and wear between two moving parts. These bushings are made from a variety of bronze alloys and are designed to provide a low-friction surface between the two components, helping to increase the lifespan of machinery and equipment.
One of the primary benefits of using bronze bushings is their ability to handle high loads and withstand harsh environmental conditions. Bronze is a strong and durable material that can withstand high levels of stress and shock, making it suitable for use in heavy machinery and equipment.
Bronze bushings also offer excellent wear resistance, which helps to reduce the need for frequent replacement and maintenance. This is particularly important in applications where downtime is costly, such as in the manufacturing, mining, and construction industries.
There are several types of bronze alloys used in the manufacture of bushings, including C93200, C95400, and C86300. Each alloy has its own unique properties and benefits, such as high strength, wear resistance, or corrosion resistance, making it important to select the right alloy for a particular application.
Bronze bushings are commonly used in a wide range of industries, including aerospace, automotive, agriculture, and marine. They are particularly well-suited for use in high-load applications, such as in engines, transmissions, and pumps.
When selecting bronze bushings for an application, it is important to consider factors such as load capacity, lubrication requirements, and environmental conditions. Proper installation and maintenance can also help to ensure optimal performance and longevity of the bushings.
Overall, bronze bushings are a reliable and cost-effective solution for reducing friction and wear in machinery and equipment. Their strength, durability, and wear resistance make them an essential component in many industries, helping to increase efficiency, reduce downtime, and extend the lifespan of machinery and equipment.
Installation and Maintenance Bushing
Bushing installation is an important process that should be done correctly to ensure optimal performance and safety. Similarly, proper maintenance of C93200 bushings is crucial to prevent wear, damage, and failure in industrial applications. Here are some tips for both installation and maintenance of C93200 bushings:
How to Properly Install C93200 Bushings:
- Prepare the equipment: Before installing the bushing, ensure that the equipment is clean, free of debris, and the shaft is properly aligned.
- Select the right bushing: Choose the appropriate C93200 bushing size and material for the application. Verify that the bushing is compatible with the shaft and housing bore.
- Lubricate the bushing: If necessary, lubricate the bushing before installation. Use the correct lubricant and apply it evenly to ensure optimal performance.
- Insert the bushing: Insert the bushing into the housing bore or other equipment component, and then slide it onto the shaft. Ensure that the bushing is seated securely and aligned correctly.
- Check the fit: After installation, check the fit of the bushing and the equipment. Ensure that there is no interference, and the equipment is operating correctly.
Maintenance Tips for C93200 Bushings:
- Lubrication: C93200 bushings are self-lubricating, but in some cases, external lubrication may be necessary. Follow the lubrication recommendations of the manufacturer or consult with a professional to determine the best lubrication strategy for your specific application.
- Regular inspection: Regularly inspect the C93200 bushings for signs of wear, damage, or misalignment. If any issues are found, address them promptly to prevent further damage or failure.
- Cleanliness: Keep the bushings and surrounding equipment clean and free of debris to prevent contamination and damage.
- Temperature control: Ensure that the temperature of the equipment and the environment remains within the recommended range for the C93200 bushings.
- Replace worn bushings: When C93200 bushings show signs of wear or damage, they should be replaced promptly to prevent further damage or failure.
Proper installation and maintenance of C93200 bushings are essential to ensure optimal performance and prevent damage or failure. Follow the installation and maintenance tips outlined above to keep your C93200 bushings and equipment operating smoothly and safely.
Types of bushings
There are several types of bushings, which are components used in mechanical systems to provide support and reduce friction between two moving parts. Some common types of bushings include:
- Sleeve bushings: These are cylindrical bushings that slide over a shaft or rod to provide a low-friction surface for it to rotate against.
- Flanged bushings: Similar to sleeve bushings, but with a flange on one end to prevent the bushing from sliding out of its housing.
- Tapered bushings: These bushings have a conical shape, and are used to secure pulleys, sprockets, and other components to shafts.
- Split bushings: Also known as clamp-on bushings, these are designed to be installed without having to remove the shaft or other components from the assembly.
- Spherical bushings: These bushings have a ball-and-socket design that allows them to accommodate misalignment between two components while still providing support and reducing friction.
- Self-lubricating bushings: These bushings have a built-in lubrication system that eliminates the need for external lubrication, making them ideal for applications where maintenance is difficult or impossible.
- Composite bushings: These bushings are made from a combination of materials, such as metal and plastic, to provide specific performance characteristics, such as low friction or high load capacity.
Understanding Small Bushings and Their Applications Discover the various uses and benefits of small bushings in electronics, machinery, and other industries.
Small bushings, including those made from bronze material in metric or inch sizes, are essential components used in a wide range of industries, including electronics, machinery, and manufacturing. These bushings are designed to provide a low-friction surface between two moving parts, which helps to reduce wear and tear on the machinery.
One of the primary benefits of using small bushings is their ability to reduce friction and wear in small, tight spaces where other components may not be suitable. They are commonly used in applications such as electric motors, small pumps, and other precision machinery.
Small bushings can also help to reduce noise and vibration in machinery by dampening vibrations and reducing the amount of noise produced by the rotating parts.
When selecting small bushings for an application, it is important to consider factors such as load capacity, lubrication requirements, and environmental conditions. Some small bushings may require specific types of lubrication, such as oil or grease, to ensure optimal performance.
Additionally, custom-size bushings can be manufactured to fit unique applications and requirements. This allows for greater flexibility in the design and construction of machinery and equipment.
Bronze is a common material used for small bushings due to its strength, wear resistance, and ability to withstand harsh environmental conditions. The material is also resistant to corrosion, making it suitable for use in applications where exposure to moisture or other corrosive substances is a concern.
Small bushings are an important component in many types of machinery and equipment, providing a low-friction surface to reduce wear and tear and improving overall performance. Understanding the unique requirements of an application can help to ensure that the appropriate small bushing is selected for optimal performance and durability.
Large Bushing, A Guide to Large Bushings for Heavy-Duty Applications
Large bushings, particularly those made from C93200 bronze material, are an essential component in heavy-duty machinery used in mining, construction, and other similar industries. These bushings are designed to handle high loads and provide long-lasting performance in harsh environments.
One of the main advantages of using large bushings in heavy-duty applications is their ability to withstand high levels of stress and shock. They are designed to provide a low-friction surface between two moving parts, which helps to reduce wear and tear on the machinery. This helps to increase the lifespan of the equipment and reduce maintenance costs over time.
Large bushings made from C93200 bronze material are particularly well-suited for heavy-duty applications due to their high strength and wear resistance. The material contains a high percentage of copper, which gives it its strength and durability. It is also resistant to corrosion and wear, even in harsh environments where other materials may fail.
Another advantage of using large bushings in heavy-duty machinery is their versatility. They can be used in a wide range of applications, including in conveyor systems, crushers, and other types of heavy machinery.
When selecting large bushings for heavy-duty applications, it is important to consider factors such as load capacity, lubrication requirements, and environmental conditions. It is also important to choose a reputable supplier who can provide high-quality bushings that meet the specific needs of the application.
Overall, large bushings made from C93200 bronze material are a reliable and cost-effective solution for heavy-duty machinery in mining, construction, and other heavy industries. Their ability to handle high loads, withstand harsh environments, and provide long-lasting performance make them an essential component in many types of machinery and equipment.
Pivot bushings c93200 bronze bearing material, Precision and Efficiency with Pivot Bushings Find out how to pivot bushings can optimize the movement of rotating or pivoting parts in machines and equipment.
Pivot bushings made from C93200 bronze bearing material are essential components used in machinery and equipment to optimize the movement of rotating or pivoting parts. These bushings are designed to reduce friction and wear in the pivot points, allowing for smoother and more efficient movement.
One of the main benefits of using pivot bushings is their ability to provide a low-friction surface between the pivot point and the surrounding component, which reduces wear and tear on the machinery. This helps to extend the lifespan of the equipment and reduce maintenance costs over time.
C93200 bronze bearing material is an ideal choice for pivot bushings due to its high strength, wear resistance, and ability to withstand harsh environmental conditions. The material contains a high percentage of copper, which gives it its strength and durability. It is also resistant to corrosion and wear, even in harsh environments where other materials may fail.
In addition to reducing friction and wear, pivot bushings also help to improve the efficiency and accuracy of the movement in rotating or pivoting parts. They provide a stable and consistent pivot point, which helps to ensure that the movement is smooth and predictable.
When selecting pivot bushings, it is important to consider factors such as load capacity, lubrication requirements, and environmental conditions. Some pivot bushings may require specific types of lubrication, such as oil or grease, to ensure optimal performance.
Pivot bushings made from C93200 bronze bearing material are a reliable and cost-effective solution for optimizing the movement of rotating or pivoting parts in machinery and equipment. Their ability to reduce friction and wear, improve efficiency and accuracy, and withstand harsh environmental conditions make them an essential component in many types of machinery and equipment.