Sliding Material and Bush Bearing Type Selection Guide
Experience the Strength of Self-lubricating Bearings
Bush Bearing Supplier
The choice of material for a sliding bearing bushing is crucial as it can significantly affect the performance and longevity of the bearing in a given application. We offers a wide range of bushings in various designs and materials. Straight bushings can only accommodate radial loads, while flanged bushings can handle both radial and axial loads in one direction. Each design and material combination has unique properties that make it suitable for specific applications.
Bush Bearing Selection Guides :
When selecting a bushing, it’s important to consider factors such as ambient temperature range, coefficient of friction, load capacity, and sliding velocity. For example, the permissible ambient temperature ranges for different bushing types can be extended with special lubricants. The friction characteristics are influenced by load, sliding velocity, surface roughness, and lubrication conditions.
Precision Bush Bearings Delivered Fast: Upgrade Your Machinery with Quality Bush Bearings. Fast Shipping!
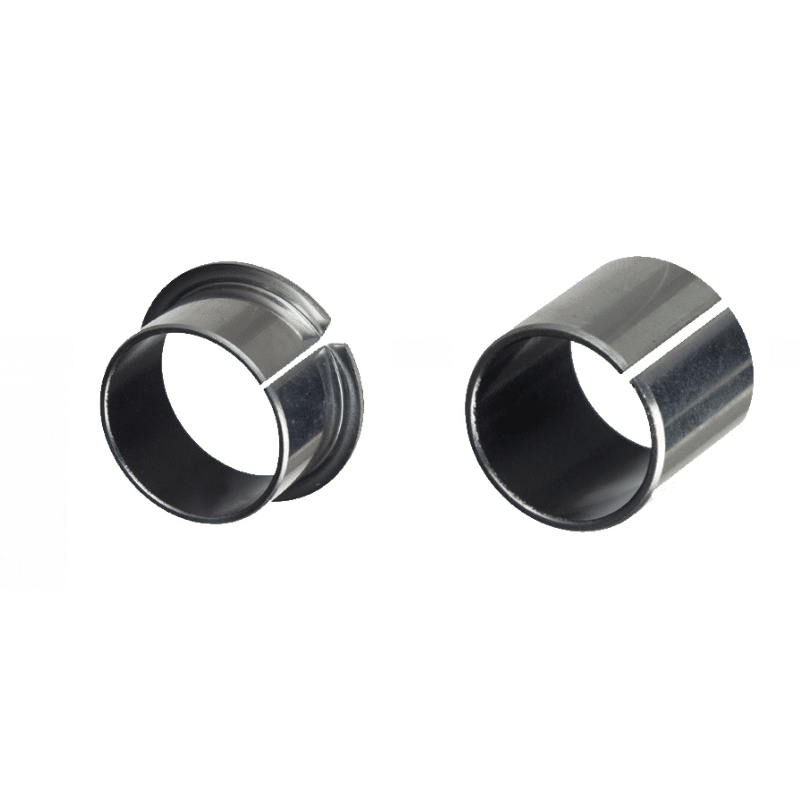
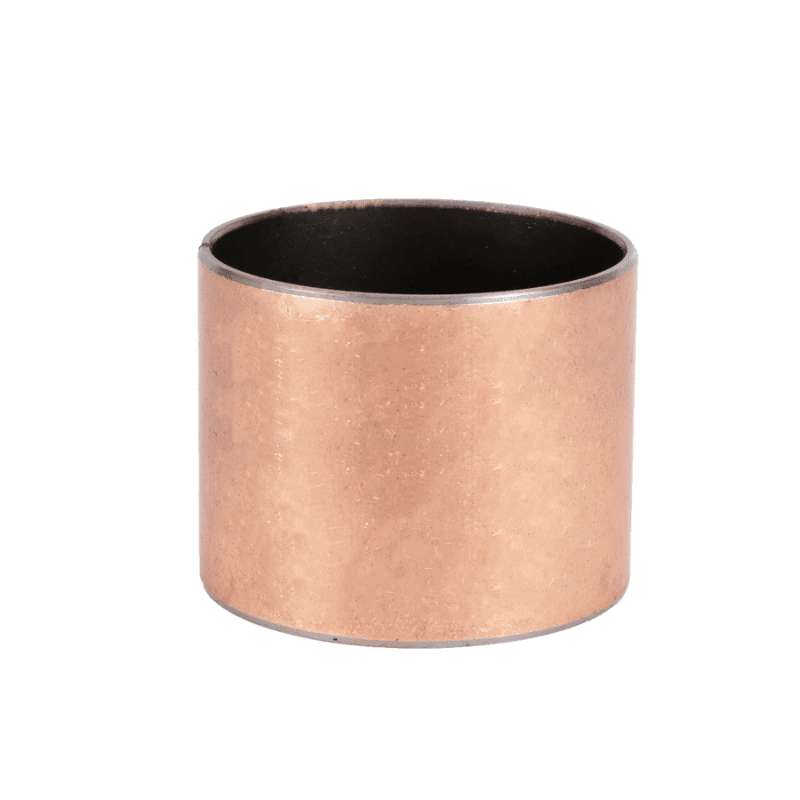
Bush Bearings and Sliding Bearing :
We offers maintenance-free polymer bearings that are suitable for environments that are dirty or dusty and do not require oil or grease. The bush bearing product line includes various types of linear guide rails and slides that are designed to be durable, lightweight, and easy to assemble. They also provide an online lifetime calculator to help with the selection process.
Need Reliable Bush Bearings? Explore Our Vast Selection. Durable & Precision-Engineered Bearings for All Applications!
Expert Bush Bearing Solutions: Find the Perfect Bearing Fit with Our Expert Help. Custom Sizes Available. Contact Us!
Bushing vs Bearing :
Sleeve bearings, or bushings, are the simplest type of bearing, characterized by their sleeve shape. They are used in applications requiring low friction where precise alignment isn’t essential.
Discover affordable industrial bush bearings with bulk discounts! Request your free quote today!
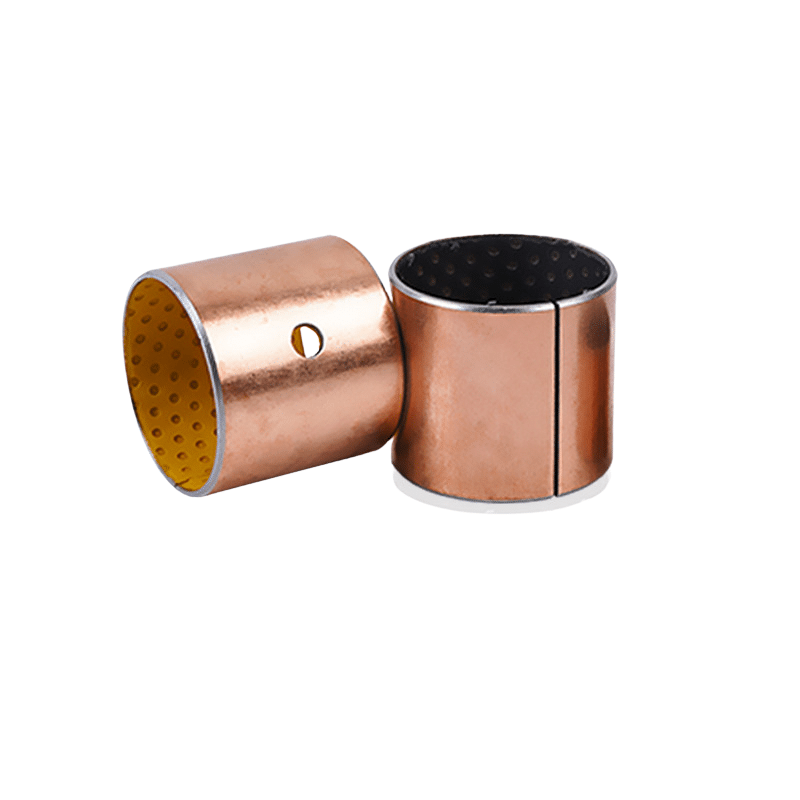
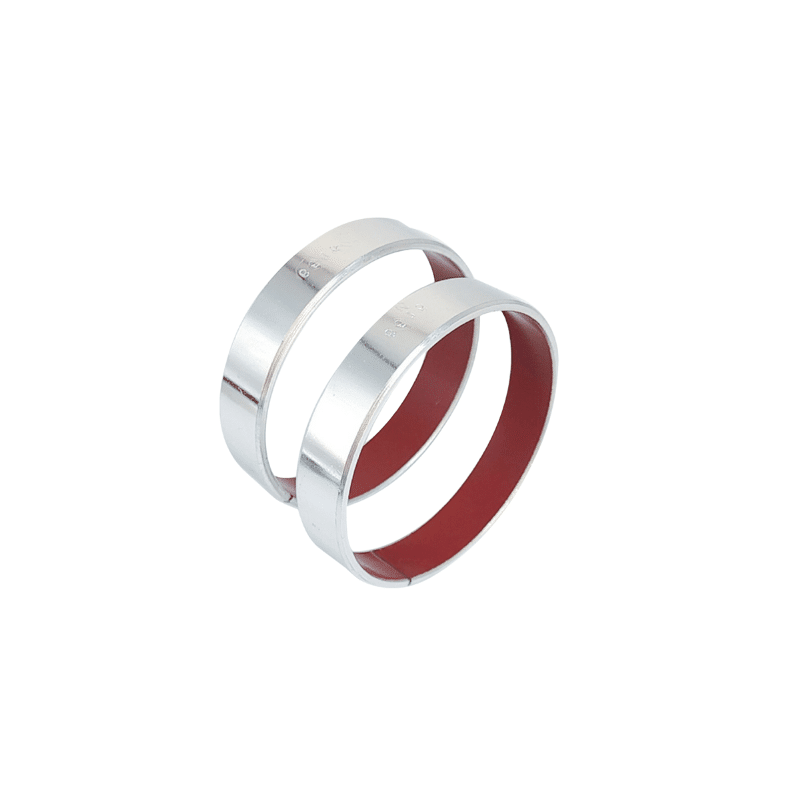
Sliding Material and Bushing Type Selection Guide :
This guide provides information on selecting the appropriate sliding material and bushing type for specific applications, ensuring quality and service. The material of a sliding bearing bushing should be chosen based on the specific requirements of the application, including the type of movement, load conditions, temperature range, and environmental factors. We provide a variety of materials and designs to meet these diverse needs.
Bush Bearings for High-Performance Needs: Enhance Efficiency with Our Bush Bearings. Built to Last. Order Now and Experience the Difference!
Choosing the Right Bush Bearing Material: A Deep Dive for Optimal Performance
Bush bearings, also known as plain bearings or sleeve bearings, are fundamental components in countless machines. Their simple design – essentially a sleeve supporting a rotating or sliding shaft – belies the critical importance of selecting the right material. Choosing incorrectly can lead to premature failure, excessive friction, costly downtime, and even damage to other components.
Superficial knowledge isn’t enough. A bearing that works perfectly in a low-load, clean environment might fail catastrophically under high pressure or in corrosive conditions. This deep dive explores the world of bush bearing materials, examining their properties, comparing common choices, and guiding you toward making an informed decision.
Why Bush Bearing Material Selection is Paramount
The material directly influences a bearing’s core performance characteristics. Getting it right means optimizing:
-
Load Capacity: Will the bearing deform or crush under operational forces?
-
Wear Resistance: How long will it last before needing replacement?
-
Friction Coefficient: How efficiently will it operate? Lower friction means less energy loss and heat generation.
-
Temperature Resistance: Can it handle the operating heat (or cold) without degrading?
-
Corrosion Resistance: Will it survive exposure to moisture, chemicals, or other environmental factors?
-
Cost-Effectiveness: Balancing initial cost with lifespan and maintenance needs.
Let’s delve into the properties that define a bearing material’s suitability:
Table 1: Key Bearing Material Properties & Their Significance
Property | Description | Why It Matters |
Compressive Strength | Ability to withstand static loads without permanent deformation (yielding). | Prevents the bearing from being crushed under load. Critical for high-load apps. |
Fatigue Strength | Ability to withstand repeated cyclic loads without cracking or failure. | Essential for applications with variable or reversing loads (e.g., engines). |
Wear Resistance | Ability to resist material loss due to abrasion, adhesion, or surface fatigue. | Determines the bearing’s lifespan, especially in abrasive or poorly lubricated conditions. |
Friction Coefficient | Ratio of frictional force to normal force between bearing and shaft (Static & Dynamic). | Lower friction = less power loss, less heat generated, potentially less wear. |
Embeddability | Ability to absorb small contaminant particles into its surface. | Protects the harder shaft from scoring/damage by trapping debris. |
Conformability | Ability to deform slightly to accommodate shaft imperfections or misalignment. | Improves load distribution, reduces edge loading, forgives minor assembly errors. |
Thermal Conductivity | Rate at which heat is transferred away from the bearing surface. | Helps dissipate frictional heat, preventing overheating and material degradation. |
Thermal Expansion | How much the material expands or contracts with temperature changes. | Must be considered for maintaining proper operating clearance across temperatures. |
Corrosion Resistance | Ability to resist degradation from chemicals, moisture, oxidation, etc. | Crucial for operation in harsh environments or with specific lubricants/fluids. |
Machinability | Ease with which the material can be shaped into the final bearing form. | Impacts manufacturing cost and complexity, especially for custom sizes. |
Cost | Raw material cost plus manufacturing expenses. | Must align with the overall project budget and performance requirements. |
Common Categories of Bush Bearing Materials
We can broadly classify bush bearing materials into three main groups: Metals, Polymers (Plastics), and Composites. Each has distinct advantages and disadvantages.
1. Metal Bushings: The Traditional Workhorses
Metals have long been the standard for many bearing applications due to their strength and temperature resistance.
-
Bronze Alloys: Perhaps the most common metal bearing material. Different alloys offer tailored properties:
-
Tin Bronze (e.g., C90300, C90500): Good strength, wear resistance, and corrosion resistance. General purpose.
-
Leaded Bronze (e.g., C93200 – SAE 660): Added lead improves machinability, embeddability, and conformability. Provides some “emergency” lubricity if lubrication fails. Tolerant of minor misalignment and contamination. Caution: Lead content raises environmental/health concerns.
-
Aluminum Bronze (e.g., C95400): High strength, excellent corrosion resistance (especially saltwater), good wear resistance, suitable for higher loads. Less conformable than leaded bronzes.
-
Phosphor Bronze (e.g., C51000, C54400): Increased phosphorus enhances hardness, wear resistance, and fatigue strength. Often used in higher load/speed applications than tin bronzes.
-
-
Babbitt Metals (White Metals): Tin-based or Lead-based alloys, often used as a lining inside a stronger steel or bronze shell.
-
Key Features: Excellent embeddability and conformability, low friction coefficient. Relatively low load capacity and temperature limits compared to bronzes. Ideal for high speeds, lower loads, and applications where shaft protection is critical (e.g., engine crankshaft bearings).
-
-
Cast Iron (e.g., Gray Cast Iron):
-
Key Features: Lower cost, good wear resistance (graphite flakes provide some self-lubrication), good vibration damping. More brittle than bronze. Used in lower-speed, moderate-load applications.
-
-
Sintered (Powdered) Metals: Typically bronze or iron powders pressed and heated (sintered).
-
Key Features: Creates a porous structure that can be impregnated with oil (e.g., SAE 841 Oil-Impregnated Bronze). Provides self-lubrication, ideal for applications where regular maintenance is difficult. Load capacity is generally lower than solid equivalents.
-
Table 2: Comparison of Common Metal Bushing Materials
Material | Key Strengths | Key Weaknesses | Typical Applications | Relative Cost |
Leaded Bronze | Good balance of properties, conformable, embeddable | Moderate strength, lead concerns | General machinery, moderate loads/speeds, tolerant operation | Medium |
Alu. Bronze | High strength, excellent corrosion resistance | Less conformable, can be harder on shafts | Heavy loads, corrosive environments, gears, valve guides | Medium-High |
Babbitt | Excellent conformability/embeddability, low friction | Lower strength, lower temp limit | Engine bearings, turbines, high speed/low load | High (often as liner) |
Cast Iron | Low cost, good wear/damping, self-lubricating (gray) | Brittle, lower corrosion resistance | Low speed machinery, agriculture, simple applications | Low |
Sintered Bronze | Self-lubricating, quiet operation | Lower load capacity, limited temp (by oil) | Small motors, appliances, hard-to-lubricate spots | Low-Medium |
2. Polymer (Plastic) Bushings: Lightweight & Versatile
Polymer bearings have gained significant popularity due to their self-lubricating properties, light weight, corrosion resistance, and often lower cost.
-
Acetal (POM – Polyoxymethylene): Good strength and stiffness, excellent dimensional stability (low moisture absorption), low friction, good wear resistance. A popular general-purpose plastic bearing material.
-
PTFE (Polytetrafluoroethylene ): Extremely low friction coefficient, excellent chemical resistance, wide temperature range. Drawbacks: Low strength, poor wear resistance (unless filled), prone to cold flow (creep) under load. Often used as a liner or filled with glass, carbon, or bronze for improved mechanical properties.
-
UHMWPE (Ultra-High Molecular Weight Polyethylene): Excellent abrasion resistance, high impact strength, low friction, good chemical resistance. Lower temperature limit and load capacity than Nylon or Acetal. Great for high-wear, lower-load applications like conveyor belts or food processing.
-
PEEK (Polyether Ether Ketone): High-performance thermoplastic. Excellent strength, stiffness, wear resistance, chemical resistance, and high-temperature performance (up to ~250°C / 480°F). Significantly more expensive. Used in demanding applications (aerospace, medical, chemical processing).
Table 3: Comparison of Common Polymer Bushing Materials
Material | Key Strengths | Key Weaknesses | Typical Applications | Relative Cost |
Nylon (PA) | Tough, good wear (esp. filled), low cost | High moisture absorption (dimensional change) | Low-medium loads, rollers, wheels, where moisture isn’t critical | Low |
Acetal (POM) | Dimensionally stable, good strength/stiffness | Lower temp limit than PEEK, less tough than Nylon | General purpose, precision parts, food contact (some grades) | Low-Medium |
PTFE | Very low friction, excellent chemical/temp resistance | Low strength/wear, creep under load (unless filled) | Low load/speed slides, chemical pumps, seals (often filled) | Medium (higher when filled) |
UHMWPE | Excellent abrasion resistance, high impact | Lower temp/load limit than Acetal/Nylon | Conveyors, chutes, food processing, high-wear guides | Medium |
PEEK | High temp, high strength, excellent chemical res. | High Cost | Aerospace, medical, chemical, demanding industrial | Very High |
Composite Bushings: The Best of Both Worlds?
Composites combine different materials – often leveraging the strengths of metals and polymers – to achieve performance characteristics unattainable by a single material type. They represent engineered solutions for demanding applications where standard materials fall short.
-
Metal-Backed Polymer Bushings:
-
Structure: These are multi-layered bearings. A strong metal backing (typically steel for strength and cost-effectiveness, or bronze for better corrosion resistance and thermal conductivity) provides rigidity and dimensional stability. Bonded to this is an intermediate porous layer, often sintered bronze. This layer serves multiple purposes: it mechanically locks the polymer layer to the backing, helps transfer heat away from the bearing surface, and can act as a reservoir for lubricant impregnation during manufacturing. Finally, a polymer-based overlay (the actual bearing surface) is applied and impregnated into the bronze layer.
-
Common Overlays:
-
PTFE-Based : Incorporates PTFE and other fillers (like lead in original DU, now often lead-free fillers) for extremely low friction, self-lubrication, and good chemical resistance. Ideal for dry running or minimal lubrication applications across a wide temperature range. Requires a transfer film to form on the shaft for optimal performance.
-
Acetal (POM)-Based (Pom series): Features an acetal copolymer overlay, often with lubricant pockets indented into the surface. Designed for marginally lubricated or grease-lubricated applications. Offers good wear resistance and load capacity but generally lower temperature limits and slightly higher friction than PTFE-based types.
-
-
Key Benefits: High load capacity (static and dynamic) due to the metal backing, excellent heat dissipation, very low friction (especially PTFE-based), self-lubricating, compact dimensions, good chemical resistance (depending on overlay).
-
Limitations: Can be susceptible to edge loading if misalignment is severe, corrosion resistance depends on the backing material and plating (if any). Performance relies heavily on the integrity of the thin polymer layer.
-
-
Fiber-Reinforced Polymer Bushings:
-
Structure: These composites consist of high-strength fibers embedded within a polymer matrix. The fibers act as the primary load-bearing elements, while the polymer matrix binds them together, transfers load between fibers, and provides the bearing surface’s characteristics (chemical resistance, base friction).
-
Common Fibers:
-
Glass Fibers: Offer a good balance of increased strength, stiffness, and relatively low cost. Most common reinforcement.
-
Carbon Fibers: Provide significantly higher stiffness, strength, and lower weight compared to glass fibers, plus excellent fatigue resistance and low thermal expansion. More expensive.
-
Aramid Fibers (e.g., Kevlar®): Known for exceptional toughness, impact resistance, and vibration damping, but lower compressive strength than glass or carbon.
-
Polyester Fibers: Lower cost option for moderate strength improvements.
-
-
Common Polymer Matrices: Nylon (PA), PEEK, Epoxy Resins, Phenolic Resins, Polyester, Polyurethane (PU). The matrix largely determines temperature limits, chemical resistance, and inherent friction/wear properties. Lubricating fillers (PTFE, graphite, MoS2) are often added.
-
Manufacturing: Can be made through injection molding (with chopped fibers), filament winding (continuous fibers wound onto a mandrel, often with epoxy resin, creating very high strength in specific directions), or lamination processes.
-
Key Benefits: High strength-to-weight ratio, excellent corrosion resistance (no metal components), good wear resistance (can be tailored), potential for complex shapes (molded), good vibration damping, and often self-lubricating. Can operate in abrasive or wet environments where metals struggle.
-
Limitations: Generally lower thermal conductivity than metal-backed types (heat dissipation can be a concern at high speed/load), potentially higher cost, can be abrasive to softer shaft materials (depending on fibers/fillers), properties can be anisotropic (direction-dependent) especially in filament-wound types, lower tolerance for sharp impacts compared to ductile metals (though toughness can be high).
-
Table 4: Contrasting Metal-Backed vs. Fiber-Reinforced Composite Bushings
Feature | Metal-Backed Polymer (e.g., DP4, DX) | Fiber-Reinforced Polymer (e.g., Carbon/PEEK, Glass/Epoxy) | Key Decision Factor |
Primary Strength | High Static Load Capacity, Rigidity | High Strength-to-Weight, Corrosion Resistance, Toughness | Match bearing type to dominant load/environmental challenge |
Heat Dissipation | Excellent (Metal Backing) | Fair to Good (Matrix/Fiber dependent) | Critical for high speed/load applications. |
Friction | Very Low (esp. PTFE types) | Low to Moderate (Matrix/Fiber/Filler dependent) | Metal-backed often offers lowest friction out-of-the-box. |
Corrosion Resistance | Good (Bronze Backing) to Fair (Steel) | Excellent (No Metal) | FRP excels in chemically aggressive or wet environments. |
Weight | Medium | Low | FRP preferred where weight saving is critical (e.g., aerospace). |
Impact Resistance | Good | Good to Excellent (esp. Aramid fibers) | FRP can offer superior toughness. |
Operating Temp. | Wide Range (Overlay Limited) | Wide Range (Matrix/Fiber Limited, potentially Very High w/ PEEK/Carbon) | High-temp FRPs can exceed limits of many polymer overlays. |
Cost | Medium to High | High to Very High | Performance benefits vs. budget constraints. |
Form Flexibility | Mostly Cylindrical/Flanged/Washers | Higher (Molding allows complex shapes) | FRP offers more design integration possibilities. |
Shaft Friendliness | Generally Good (Soft Polymer Layer) | Can be abrasive (depends on fiber/filler) | Shaft hardness needs consideration with FRPs. |
Typical Use Case | High Load Pivot Points, Linkages, Hydraulics | Aerospace, Marine, Chemical Processing, High-Performance Industrial | Application environment and specific performance needs. |
Composite bushings bridge the gap between the limitations of simple metals and polymers, offering engineered solutions for applications demanding high load capacity and low friction, or high strength and excellent corrosion resistance, often with self-lubricating properties.
Factors Influencing Material Selection: The PV Factor and Beyond
A crucial concept in bearing selection, especially for polymer and composite bearings, is the PV factor.
-
P = Pressure (Load per Unit Area) (psi or N/mm²)
-
V = Surface Velocity (Sliding Speed) (fpm or m/s)
The PV value (P x V) represents the combined mechanical and thermal stress on the bearing. Every bearing material has a maximum limiting PV value, above which wear rate increases dramatically, and thermal failure (melting, degradation) becomes likely.
-
High P, Low V: Requires high compressive strength, good wear resistance (e.g., Aluminum Bronze, Fiber-Reinforced Composites).
-
Low P, High V: Requires low friction coefficient, good thermal conductivity/heat resistance (e.g., Babbitt, PTFE-based Composites, Carbon Graphite).
-
High P, High V: The most demanding scenario. Requires materials with high limiting PV values, excellent wear resistance, and often external lubrication/cooling (e.g., Metal-Backed Composites, High-Temp FRPs, sometimes specially treated Bronzes).
Beyond PV, Consider:
-
Operating Temperature: Min/Max temps affect material strength, clearance (thermal expansion), and lubricant viscosity/integrity.
-
Environment: Presence of moisture, chemicals, dirt, radiation. Dictates need for corrosion resistance, sealing, embeddability.
-
Lubrication:
-
Fully Lubricated (Hydrodynamic): Material properties are less critical as shaft & bearing are separated by oil film. Fatigue strength and corrosion resistance matter.
-
Marginally Lubricated (Boundary/Mixed Film): Bearing material properties are crucial! Low friction, wear resistance, compatibility with lubricant are key. Self-lubricating materials excel here.
-
Dry Running: Requires inherently low friction, self-lubricating materials (Polymers, Composites, Graphite).
-
-
Shaft Material & Hardness: The bearing and shaft form a system. Harder shafts generally allow for higher bearing loads and reduce wear on both components. Some bearing materials (e.g., abrasive FRPs) require very hard shafts. Softer materials (Babbitt, Polymers) are more forgiving of softer shafts.
-
Misalignment: Requires materials with good conformability (Babbitt, Leaded Bronze, some Polymers) or designs incorporating self-aligning features.
-
Cost & Availability: Balance performance needs with budget and lead times for standard or custom bearings.
Conclusion: Making the Informed Choice
Selecting the optimal bush bearing material is not a one-size-fits-all process. It requires a thorough understanding of the application’s demands – load, speed, temperature, environment, lubrication, and shaft characteristics – and matching those demands to the properties of candidate materials.
-
Start with Metals (Bronzes) for general-purpose, moderate-to-high loads, and good temperature resistance, especially if lubrication is reliable.
-
Consider Polymers (Acetal, Nylon, UHMWPE) for lower loads, corrosion resistance, self-lubrication needs, and cost sensitivity, paying close attention to temperature and moisture limitations.
-
Explore Composites (Metal-Backed, Fiber-Reinforced) when pushing performance boundaries – requiring high load capacity with self-lubrication, extreme corrosion resistance, high strength-to-weight, or operation in very demanding environments.
-
Don’t forget Babbitt for high-speed, fluid-film applications where shaft protection is paramount.
-
Leverage Sintered Metals for cost-effective self-lubrication where loads are moderate.
Using comparison tables, understanding the PV factor, and carefully considering all operating conditions are essential steps. Consulting manufacturer data sheets for specific material grades is crucial, as properties can vary significantly even within the same family (e.g., different bronze alloys or filled PTFE compounds). Investing time in material selection upfront prevents costly failures and ensures the longevity and efficiency of your machinery.
Bearing (The Broad Category)
-
Definition: A bearing is a general engineering term for any machine element that constrains relative motion between two or more parts to only the desired motion (like rotation or linear movement) and reduces friction between them.
-
Function: Bearings support shafts or other components, allowing them to move smoothly with minimal wear and energy loss.
-
Types: There are two fundamental ways bearings achieve this:
-
Sliding Contact: One surface slides directly against another (with or without lubrication).
-
Rolling Contact: Elements (like balls or rollers) are placed between two surfaces (races) to allow rolling motion instead of sliding.
-
Bushing (A Specific Type of Bearing)
-
Definition: A bushing is a specific type of bearing that operates using sliding contact. It is also commonly known as a plain bearing or a sleeve bearing.
-
Structure: Typically, a bushing is a simple, often one-piece component (though multi-layered composites exist), usually cylindrical. It provides a bearing surface for rotary or linear applications. There are no rolling elements.
-
Mechanism: The shaft slides directly against the inner surface of the bushing. Lubrication (grease, oil, solid lubricant embedded in the material, or the inherent properties of the material like PTFE) is often crucial to minimize friction and wear.
The Core Distinction: Sliding vs. Rolling
The easiest way to differentiate is by mechanism:
-
Bushings / Plain Bearings / Sleeve Bearings = Use SLIDING contact.
-
Rolling Element Bearings = Use ROLLING contact (e.g., ball bearings, roller bearings, needle bearings, tapered roller bearings).
Analogy:
Think of the term “Vehicle” vs. “Car”.
-
Bearing is like Vehicle: A broad category encompassing many types (cars, trucks, motorcycles, bicycles).
-
Bushing is like Car: A specific type within the broader category of vehicles.
All bushings are bearings, but not all bearings are bushings. Ball bearings, for instance, are bearings, but they are not bushings.
Why the Confusion?
Often, in casual or even some technical contexts, when people compare “bushings” vs. “bearings,” they are implicitly using “bearings” as shorthand for “rolling element bearings.”
So, the comparison is really: Plain Bearings (Bushings) vs. Rolling Element Bearings.
Table: Bushing (Plain Bearing) vs. Rolling Element Bearing
Feature | Bushing (Plain Bearing / Sleeve Bearing) | Rolling Element Bearing (Ball, Roller, etc.) |
Primary Mechanism | Sliding Contact | Rolling Contact |
Key Components | Typically a single sleeve/part | Inner Race, Outer Race, Rolling Elements (Balls/Rollers), Cage |
Friction | Generally higher (esp. at startup) | Generally lower (esp. at startup) |
Load Capacity | Can be very high (large contact area) | High dynamic load capacity for size |
Speed Capability | Often lower limit (heat generation) | Often capable of higher speeds |
Noise/Vibration | Generally quieter, good damping | Can generate more noise/vibration |
Sensitivity to Debris | Can embed small particles (embeddability) | Highly sensitive to contamination |
Misalignment Tolerance | Some materials conform (conformability) | Lower tolerance (unless self-aligning type) |
Maintenance | Often simpler, can be self-lubricating | Requires proper lubrication & sealing |
Cost | Generally lower | Generally higher |
Complexity | Simple | More Complex |
In Summary:
-
Bearing: The umbrella term for components reducing friction and guiding motion.
-
Bushing: A specific type of bearing (a plain bearing) that works via sliding contact, usually a simple sleeve.
When discussing bearing material selection, as in the previous article, we were primarily focused on materials for bushings (plain bearings), because the material itself forms the sliding surface and dictates performance. In rolling element bearings, the material choice for the races and rolling elements is critical, but the mechanism (rolling) is fundamentally different.
Custom Online CNC Machining Services
Get instant quotes for custom metal and self-lubricating bronze parts with our online CNC machining service. Create prototypes and production parts in just days!