ZCuAI10Fe3 Aluminum Bronze Graphite Wear Plate: Benefits and Applications
Bearings and Bushings for the Future: Precision and Customization: Our company, in bearing engineering with decades of experience, designs and develops high-precision self-lubricating bronze bearings & plain bushes. We offer a wide array of sliding bearings tailored to meet specific needs. Renowned for our expertise in custom bronze bushing and slide plate solutions, we provide an expansive selection of bushing metal alloys. Contact us today to benefit from unparalleled services at competitive prices.
ZCuAI10Fe3 Aluminum Bronze Graphite Wear Plate: Benefits and Applications
Standard sizes
Bronze Plate
Looking for a durable and reliable wear plate? Check out our Aluminum Bronze Graphite Impregnated Wear Plate – perfect for heavy-duty applications
Bronze Graphite Impregnated Wear Plate – Durable & Reliable
Bronze Wear Strips – Holes and Graphite
Grease Groove Wear Plates
Focus
Self-lubricating Bronze Plate- Holes and Grease Grooves
Self-lubricating
Plate Custom Size
Graphite plugged wear plates, bronze plates come in a variety of sizes. They come complete with self-lubricating graphite and are made of aluminum bronze.

What is Aluminum Bronze Graphite Wear Plate?
Aluminum Bronze Graphite Wear Plate is a type of self-lubricating bearing material that combines the properties of aluminum bronze and graphite to create a highly wear-resistant and low-friction surface. This material is used in various industries for applications where sliding movement and heavy loads are common, such as machinery, automotive, aerospace, and construction.
Benefits of using Aluminum Bronze Graphite Wear Plate
aluminum bronze graphite wear plates offer an excellent combination of strength, wear resistance, and self-lubrication, making them an ideal choice for various applications where sliding movement and heavy loads are present.
Using aluminum bronze graphite wear plates offers several benefits, making them a popular choice for a wide range of industries and applications.
taxation planning
Eiusmod tempor incididunt ipsum ut labore dolore magna aliqua. Ut enim minim veniam duisy ipsum sed quis.
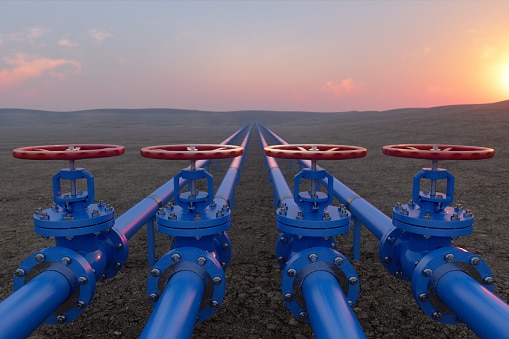
Applications of Aluminum Bronze Graphite Wear Plate
These wear plates are commonly used in the following applications:
- Bearings and bushings for heavy machinery, such as construction equipment, mining machinery, and agricultural equipment.
- Sliding components in automotive and aerospace applications, where both wear resistance and low friction are essential.
- Guideways, slides, and wear pads for industrial machinery, to ensure smooth, consistent movement and reduce maintenance requirements.
- Components in marine applications, where resistance to corrosion and wear in a saline environment is crucial.
- Industrial Machinery and Equipment
- Mining and Minerals Processing
- Oil and Gas
- Marine and Offshore
Bronze graphite impregnated wear plate material
Bronze graphite impregnated wear plate materials can be made from various bronze alloys depending on the specific requirements of the application. Some of the most common bronze alloys used in these wear plates include:
- Tin Bronze (C90700 to C94500): Tin bronze is known for its good corrosion resistance, wear resistance, and low friction properties. This alloy consists of copper and tin, with tin content typically ranging from 5% to 20%. Tin bronzes are often used in applications requiring moderate loads and speeds.
- Aluminum Bronze (C95400, C95500, C95800): Aluminum bronze alloys consist of copper and aluminum, with aluminum content usually ranging from 6% to 12%. These alloys offer excellent strength, wear resistance, and corrosion resistance. They are well-suited for applications with high loads and speeds, and in more aggressive environments.
- Manganese Bronze (C86200 to C86500): Manganese bronze is an alloy of copper, zinc, and manganese. Manganese content typically ranges from 2% to 5%. This alloy offers good strength, wear resistance, and excellent anti-corrosive properties. Manganese bronze is commonly used for applications requiring a combination of high strength and good corrosion resistance.
- Leaded Tin Bronze (C83600, C84400, C93200): Leaded tin bronze is an alloy of copper, tin, and lead. The lead content in this alloy provides improved machinability and increased wear resistance. Leaded tin bronze is suitable for applications requiring moderate loads and speeds, as well as good wear resistance and low friction.
The choice of bronze alloy depends on the specific application and performance requirements. Factors to consider when selecting an alloy include load, speed, operating temperature, and environmental conditions.
Wear Plate
Have you ever experienced the pain of equipment failure due to wear and tear? As a professional in the industry, I have witnessed the frustration that comes with unexpected downtimes and production losses. One of the most common causes of this problem is wear, which is why the use of wear plates has become a popular solution in various industrial applications.
In this blog post, we will dive into the world of wear plates, discussing what they are, how they work, and their benefits. We will also explore the different types of wear plates and how to choose the right one for your specific application. So, if you want to learn more about wear plates and how they can help you prevent equipment failure, keep reading.
What are Wear Plates?
Wear plates, also known as abrasion-resistant plates or AR plates, are protective sheets made of high-quality steel or other materials. They are designed to withstand the harsh working conditions in industries that involve high levels of wear and tear. The primary function of wear plates is to protect machinery and equipment from abrasive wear, impact, and erosion.
How do Wear Plates Work?
Wear plates work by absorbing the impact and friction generated by abrasive materials. When installed on a surface, they act as a protective shield, preventing the surface from wearing down due to constant contact with abrasive substances. This is achieved through a combination of the hardness and toughness of the material used in the wear plate.
The hardness of a wear plate refers to its ability to resist indentation or scratching. The harder the wear plate, the more resistant it is to abrasion. On the other hand, the toughness of a wear plate refers to its ability to withstand impact and shock without cracking or breaking.
What are the Benefits of Using Wear Plates?
Using wear plates offers several benefits, including:
- Enhanced Equipment Life: Wear plates provide an additional layer of protection that helps extend the life of your equipment.
- Reduced Downtime: By preventing equipment failure due to wear and tear, wear plates help reduce downtime and production losses.
- Increased Efficiency: With wear plates in place, your equipment can work more efficiently, as there is less friction and wear on the machinery.
- Cost Savings: By extending the life of your equipment and reducing downtime, using wear plates can save you money in the long run.
Types of Wear Plates:
There are several types of wear plates available in the market, each with its unique properties and benefits. Some of the most common types of wear plates include:
- Chromium Carbide Overlay (CCO) Wear Plates: CCO wear plates are made of a combination of chromium and carbon, making them highly resistant to abrasion and impact.
- Tungsten Carbide Wear Plates: Tungsten carbide wear plates are made of tungsten carbide particles embedded in a matrix of steel or other materials. They are ideal for applications that involve extreme wear and high impact.
- Ceramic Wear Plates: Ceramic wear plates are made of alumina, zirconia, or silicon carbide, making them highly resistant to abrasive wear.
- Rubber Wear Plates: Rubber wear plates are ideal for applications that involve sliding wear and impact. They are flexible and can conform to the shape of the equipment.
How to Choose the Right Wear Plate:
Choosing the right wear plate for your specific application can be challenging. Some factors to consider when selecting a wear plate include:
- Type of Wear: Consider the type of wear your equipment is exposed to, whether it’s abrasive wear, impact, or erosion.
- Material: Choose a wear plate made of a material that can withstand the type of wear you are experiencing.
- Thickness: The thickness of the wear plate should be sufficient to provide adequate protection.
- Installation: Consider the installation process and whether the wear plate can be easily
Wear Plate Material
Below is a chart that compares the technical data for the different bronze alloys: Tin Bronze (C90700 to C94500), Aluminum Bronze (C95400, C95500, C95800), Manganese Bronze (C86200 to C86500), and Leaded Tin Bronze (C83600, C84400, C93200).
Alloy Group | Typical Alloys | Composition | Tensile Strength (ksi) | Yield Strength (ksi) | Hardness (BHN) | Elongation (%) | Corrosion Resistance | Wear Resistance |
---|---|---|---|---|---|---|---|---|
Tin Bronze | C90700 to C94500 | Cu, Sn (5-20%) | 25 – 50 | 15 – 40 | 60 – 120 | 10 – 40 | Good | Good |
Aluminum Bronze | C95400, C95500, | Cu, Al (6-12%) | 70 – 120 | 30 – 100 | 150 – 250 | 5 – 20 | Excellent | Excellent |
C95800 | ||||||||
Manganese Bronze | C86200 to C86500 | Cu, Zn, Mn (2-5%) | 60 – 90 | 25 – 60 | 100 – 200 | 10 – 30 | Excellent | Good |
Leaded Tin Bronze | C83600, C84400, | Cu, Sn (5-10%), Pb (1-10%) | 20 – 40 | 10 – 25 | 50 – 90 | 10 – 40 | Good | Good |
C93200 |
Please note that the values in this chart are approximate and can vary based on the specific alloy within each group and the manufacturing process. The chart provides a general comparison of the different bronze alloy groups, but it’s essential to consult specific material data sheets and consult with an engineer or metallurgist to determine the best alloy for a given application.
Here is a chart that shows the chemical composition of the five bronze materials you mentioned, as well as various technical parameters for each material:
Bronze Material | Chemical Composition | Max. Load P (N/mm²) | Max. Speed V (m/s) | Max. PV (N/mm²·m/s) | Density ρ (g/cm³) | Tensile Strength (N/mm²) | Elongation (%) | Hardness (HB) | Max. Temp (℃) | Friction Coef. (μ) |
---|---|---|---|---|---|---|---|---|---|---|
ZCuZn25 | CuZn25 | 60 | 15 | 1.65 | 8.4 | 250 | 10 | 70 | 200 | 0.08 |
AI6Fe3Mn3 | CuAI6Fe3Mn3 | 75 | 15 | 2.25 | 7.8 | 440 | 4 | 130 | 300 | 0.08 |
ZCuSn6Zn6Pb3 | CuSn6Zn6Pb3 | 75 | 10 | 1.65 | 8.8 | 250 | 10 | 70 | 150 | 0.08 |
ZCuAI10Fe3 | CuAI10Fe3 | 70 | 15 | 2.25 | 7.7 | 450 | 3 | 140 | 300 | 0.08 |
CuSn12 | CuSn12 | 60 | 10 | 1.65 | 8.9 | 260 | 8 | 80 | 200 | 0.08 |
CuSn5Zn5Pb5 | CuSn5Zn5Pb5 | 60 | 10 | 1.65 | 8.9 | 180 | 12 | 50 | 150 | 0.08 |
taxation planning
Eiusmod tempor incididunt ipsum ut labore dolore magna aliqua. Ut enim minim veniam duisy ipsum sed quis.
Advantages of Aluminum Bronze Graphite Wear Plate
- Superior Wear Resistance
- High Load Capacity
- Low Coefficient of Friction
- Corrosion and Chemical Resistance
- Easy Machinability and Weldability
We manufacturer slide bronze plate tailored to your individual needs.
Benefits of using Aluminum Bronze Graphite Wear Plate
High wear resistance: Aluminum bronze graphite wear plates exhibit excellent wear resistance due to the combination of aluminum bronze and graphite. The alloy’s strength and hardness provide a durable surface, while the graphite particles act as a solid lubricant, reducing friction and wear.
Self-lubricating properties: The graphite particles embedded within the aluminum bronze matrix serve as a solid lubricant, eliminating the need for external lubrication in many applications. This can reduce maintenance costs, decrease the risk of contamination from external lubricants, and improve overall performance.
Corrosion resistance: Aluminum bronze alloys are known for their good resistance to corrosion, making them suitable for use in harsh environments, such as marine applications, where exposure to saline water, chemicals, or other corrosive agents is common.
High load capacity: The strength and hardness of aluminum bronze allow these wear plates to handle heavy loads without significant deformation or wear. This makes them an ideal choice for applications involving high pressure or heavy-duty machinery.
Low friction: The self-lubricating properties of graphite embedded in the aluminum bronze matrix reduce friction between sliding surfaces. Lower friction contributes to improved efficiency, reduced wear, and longer component life.
Good thermal conductivity: Aluminum bronze graphite wear plates have good thermal conductivity, helping to dissipate heat generated during operation. This can reduce the risk of overheating and minimize thermal expansion, ensuring consistent performance and reducing the likelihood of component failure.
Versatility: These wear plates can be used in a wide range of applications, including bearings, bushings, guideways, slides, and wear pads. Their combination of properties makes them suitable for use in industries such as automotive, aerospace, construction, marine, and heavy machinery.
aluminum bronze graphite wear plates offer numerous benefits, including high wear resistance, self-lubrication, corrosion resistance, high load capacity, low friction, good thermal conductivity, and versatility. These properties make them an attractive option for many applications where heavy loads, sliding movement, and harsh environments are common.
Machined Bronze Plate, Manufacturing Processes for Aluminum Bronze Graphite Wear Plate
Creating the aluminum bronze alloy:
The first step in manufacturing aluminum bronze graphite wear plates is to create the aluminum bronze alloy. This is usually done through one of the following processes:
a. Melting and casting: The base metals, such as copper and aluminum, along with other alloying elements, are melted together in a furnace. Once the desired composition is achieved, the molten alloy is poured into a mold or a continuous casting machine to form a desired shape, such as a billet, slab, or ingot. The cast product is then cooled and solidified.
b. Powder metallurgy: In this process, metal powders of the desired composition are mixed together and then compressed under high pressure to form a compacted shape. This compacted shape is then sintered in a controlled atmosphere furnace at a temperature below the melting point of the alloy, causing the metal particles to bond together and create a solid piece.
Impregnating graphite into the aluminum bronze alloy:
After the aluminum bronze alloy has been formed, the next step is to introduce the graphite particles into the material. There are several techniques for doing this:
a. Powder metallurgy with graphite addition: In this process, graphite particles are mixed with the metal powders during the initial powder metallurgy stage. After the compacted shape is sintered, the graphite particles are evenly distributed throughout the aluminum bronze matrix, creating a self-lubricating material.
b. Infiltration: In this technique, the aluminum bronze alloy is produced with a porous structure. Graphite particles are then introduced into the pores of the material through a process called infiltration. The infiltration process can be done using a slurry of graphite particles in a liquid carrier or by applying a dry graphite powder to the porous aluminum bronze surface. The material is then heated to a high temperature, causing the graphite to fill the pores and bond with the aluminum bronze matrix.
c. Mechanical impregnation: In this method, the aluminum bronze alloy is formed into a desired shape, and then graphite particles are mechanically pressed or rolled onto the surface. The wear plate may then be subjected to a heat treatment to improve bonding between the graphite particles and the aluminum bronze matrix.
After the aluminum bronze graphite wear plate has been manufactured, it may undergo additional processes such as machining, grinding, or polishing to achieve the desired dimensions and surface finish. The final product is a wear-resistant, self-lubricating material suitable for various applications, including bearings, bushings, slides, and wear pads.
How to Select the Right Aluminum Bronze Graphite Wear Plate
Selecting the right aluminum bronze graphite wear plate for your application involves considering several factors to ensure optimal performance and longevity. Here are some key aspects to take into account:
Load capacity: Determine the load capacity required for your specific application. Aluminum bronze graphite wear plates can handle heavy loads, but different compositions and manufacturing processes may offer varying load capacities. Choose a wear plate that meets or exceeds the load requirements of your application.
Operating environment: Consider the operating environment, including temperature, humidity, and exposure to corrosive substances. Some aluminum bronze graphite wear plates may have added elements or coatings that enhance corrosion resistance or offer better performance under specific environmental conditions.
Friction and wear: Analyze the sliding conditions, such as the sliding speed and contact pressure, to determine the level of friction and wear resistance required. Select a wear plate with the appropriate graphite content and composition to provide the necessary self-lubrication and wear resistance.
Thermal conductivity: If your application involves high temperatures or requires efficient heat dissipation, choose a wear plate with good thermal conductivity. This can help prevent overheating and thermal expansion, ensuring consistent performance and reducing the risk of component failure.
Dimensional stability: For applications where precise dimensions and tight tolerances are critical, select a wear plate with excellent dimensional stability. This can help maintain accurate alignment and reduce the need for frequent adjustments.
Material availability and cost: Consider the availability of the specific aluminum bronze graphite wear plate material and its cost. Opt for a material that is readily available and within your budget without compromising on performance.
Customization: If your application has unique requirements, look for a manufacturer that can provide custom solutions. This may include custom compositions, dimensions, or surface finishes to meet your specific needs.
Manufacturer reputation and support: Choose a reputable manufacturer with a proven track record of producing high-quality aluminum bronze graphite wear plates. A reliable manufacturer should also offer technical support and assistance in selecting the right wear plate for your application.
Selecting the right aluminum bronze graphite wear plate involves evaluating factors such as load capacity, operating environment, friction and wear, thermal conductivity, dimensional stability, material availability, customization options, and manufacturer reputation. By carefully considering these aspects, you can choose a wear plate that best meets the needs of your specific application and ensures optimal performance and durability.
Self lubricating bronze wear plates material, bronze alloys material for slide plates
- Aluminum Bronze Alloy: Aluminum bronze is an alloy primarily composed of copper and aluminum. The copper content typically ranges from 80% to 88%, while the aluminum content varies between 8% and 12%. Other elements, such as iron, nickel, manganese, or silicon, may be added in small amounts to improve the alloy’s mechanical properties, wear resistance, or corrosion resistance. Aluminum bronze alloys are known for their high strength, good wear resistance, and excellent corrosion resistance.
- Graphite: Graphite particles make up a small but significant portion of the aluminum bronze graphite wear plate, typically ranging from 1% to 5% of the material composition. Graphite is a form of carbon with a crystalline structure that provides excellent self-lubrication and thermal conductivity. In the wear plate, graphite particles act as a solid lubricant, reducing friction and wear during operation.
The combination of these two primary components creates a material with exceptional wear resistance, self-lubrication, high strength, and corrosion resistance. The exact proportions of each component may vary depending on the specific application requirements, desired mechanical properties, and manufacturing processes.
In addition to the aluminum bronze and graphite, some wear plates may also incorporate other elements or materials to enhance specific properties. For example, additional solid lubricants, such as molybdenum disulfide (MoS2) or polytetrafluoroethylene (PTFE), may be added to further reduce friction and wear. Similarly, other metal alloys or compounds can be added to enhance the wear plate’s overall performance in specific environments or applications.
Self lubricating bronze wear plates material, bronze alloys material for slide plates
Bronze Graphite Wear Plate, Bronze Plate Technical Data:
Material | CuZn25AI5Mn4Fe3 | CuSn5Pb5Zn5 | CuAI10Ni5Fe5 | CuSn12 | CuZn25AI5Mn4Fe3 |
Density | 8 | 8.9 | 7.8 | 8.9 | 8 |
Hardness | ≥210 | ≥70 | ≥150 | ≥75 | ≥235 |
Tensile strength | ≥750 | ≥250 | ≥500 | ≥270 | ≥800 |
Yield strength | ≥450 | ≥90 | ≥260 | ≥150 | ≥450 |
Elongation | ≥12 | ≥13 | ≥10 | ≥5 | ≥8 |
Coefficient linear expansion | 1.9×10-5/℃ | 1.8×10-5/℃ | 1.6×10-5/℃ | 1.8×10-5/℃ | 1.9×10-5/℃ |
Max. Temp. | -40~+300℃ | -40~+400℃ | -40~+400℃ | -40~+400℃ | -40~+300℃ |
Max. dynamic load | 100 | 60 | 50 | 70 | 120 |
Max. speed(Dry) | 15 | 10 | 20 | 10 | 15 |
N/mm²*m/s(Lubrication) | 200 | 60 | 60 | 80 | 200 |
Compression deformation | < 0.01 mm | < 0.05mm | < 0.04mm | < 0.05mm | < 0.005mm |
Installation and Maintenance of Aluminum Bronze Graphite Wear Plate
=Installing and maintaining aluminum bronze graphite impregnated slide plates requires careful attention to ensure optimal performance, minimal wear, and a longer service life. Here are some guidelines for proper installation and maintenance:
Installation:
Surface preparation: Ensure that the mating surfaces where the slide plate will be installed are clean, smooth, and free of burrs or debris. This will help create a uniform contact surface and reduce friction and wear during operation.
Alignment: Properly align the slide plate and the mating component to prevent uneven wear, binding, or misalignment. Use appropriate tools, such as straight edges, levels, or laser alignment systems, to ensure precise alignment.
Fastening: Secure the slide plate using appropriate fasteners, such as bolts, screws, or adhesive bonding, as per the manufacturer’s recommendations. Ensure that fasteners are properly torqued and evenly distributed to avoid uneven stress and potential failure.
Lubrication: Although aluminum bronze graphite slide plates are self-lubricating, additional lubrication may be required in some cases, especially during initial operation or in extreme operating conditions. Consult the manufacturer’s guidelines for any specific lubrication requirements.
Maintenance:
Regular inspection: Periodically inspect the slide plate for signs of wear, damage, or contamination. Check for uneven wear patterns, cracks, or other visible damage that may indicate improper alignment or overloading. Also, look for any debris or contaminants that may have accumulated on the slide plate or mating surfaces.
Cleaning: Keep the slide plate and mating surfaces clean by removing dirt, debris, or contaminants that could increase friction and wear. Use a soft brush or cloth and, if necessary, a mild solvent to remove stubborn contaminants. Avoid using abrasive materials or harsh chemicals that could damage the slide plate surface.
Lubrication: Check the slide plate’s lubrication status periodically and replenish or apply additional lubrication if needed, following the manufacturer’s guidelines. Proper lubrication can help reduce friction, wear, and extend the service life of the slide plate.
Alignment and fastening: Regularly check the alignment of the slide plate and its mating components, and make any necessary adjustments. Also, inspect the fasteners for proper torque and tightness, and retighten or replace them as needed.
Replacement: Monitor the wear of the slide plate over time, and replace it when it reaches the end of its service life or if excessive wear, damage, or deformation is observed. Prompt replacement of a worn slide plate can help prevent damage to other components and ensure optimal performance.
By following these installation and maintenance guidelines, you can ensure the proper functioning and longevity of your aluminum bronze graphite impregnated slide plates, maximizing their performance and minimizing downtime in your application.
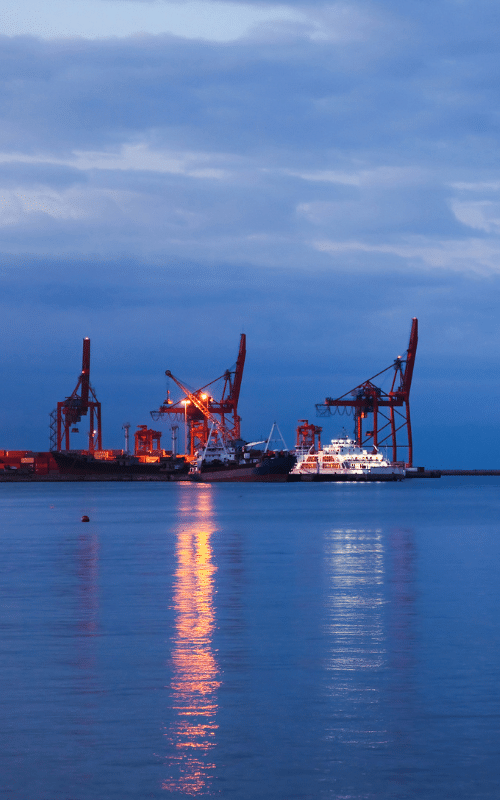
Solutions For Every Industry
Searching for Dependable Bushing Solutions? viiplus Has What You Need.
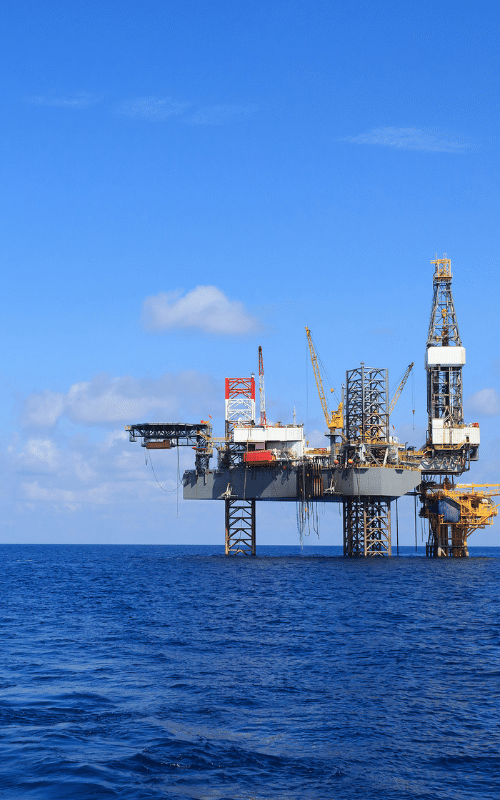
Design Guides, Materials
Bushing design, Comprehensive design manuals covering a range of self-lubricating materials used in all of viiplus’s manufacturing processes.
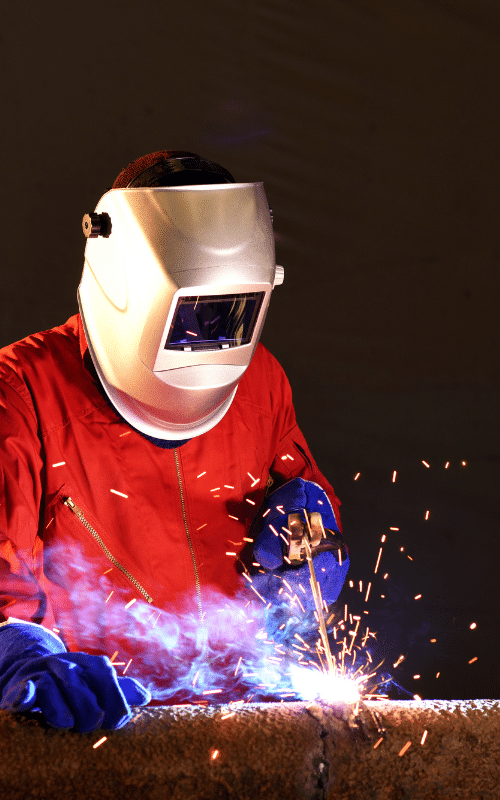
Technical Guides
Manufacturing On Demand, Technical Guides For Machining Design. Discover the latest in metal alloys, materials, and design tips for manufacturing custom machined and self-lubricating bearing parts.
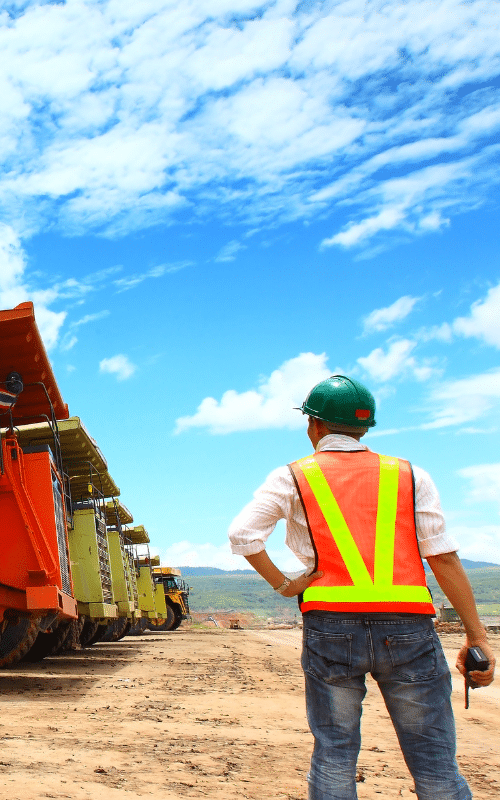
Get Instant Quote
To receive your instant quote, simply upload your drawing file and choose your production process & bushing material.
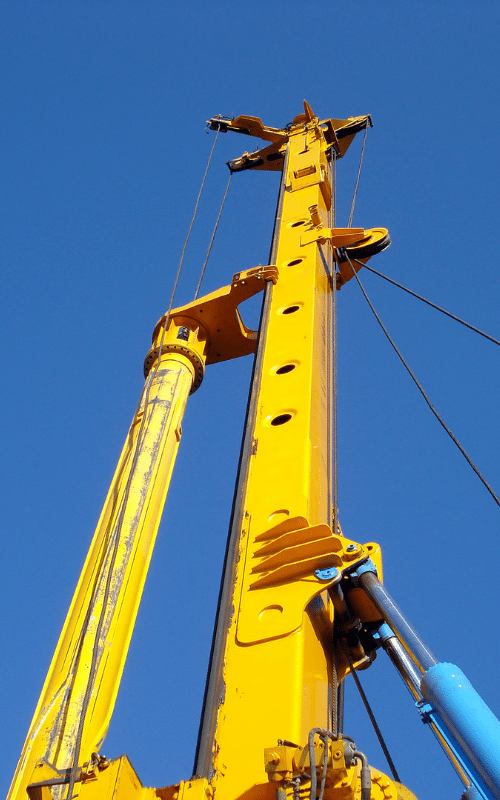
Prototyping, Place Order
After you place your order, we will start the production process. You will receive updates when your order has completed production and is ready to be dispatched.
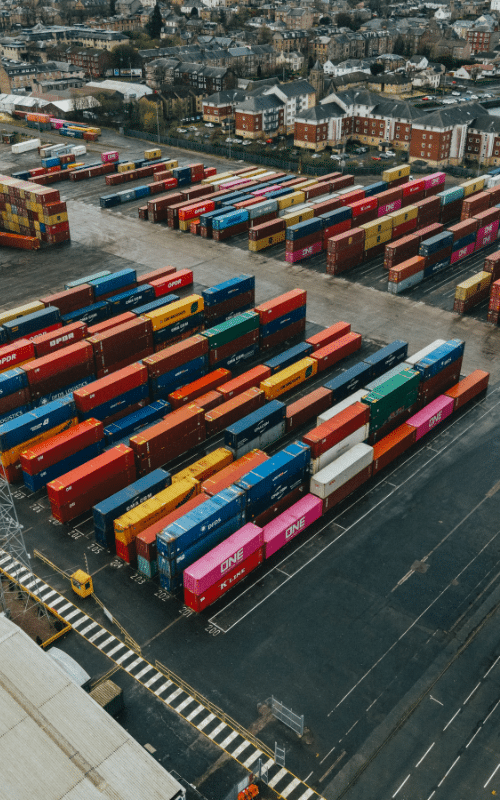
Receive Your custom Parts
We provide precision-inspected high-quality parts, packing lists and documents, and delivery tracking.