Machining Copper Gears and Worm Gear Bushes: A Comprehensive Guide
In the realm of mechanical engineering, copper stands tall as a versatile and reliable material. Its excellent properties make it a preferred choice for crafting gears and worm gear bushes that are crucial components in various industrial applications. This blog post will delve into the art of machining copper gears and worm gear bushes, shedding light on the process, benefits, and applications of these essential components. CuAl11Ni is a type of aluminum bronze alloy known for its high strength and durability. This material is often used in manufacturing various machinery components, including worm wheels and gears, due to its excellent mechanical properties.
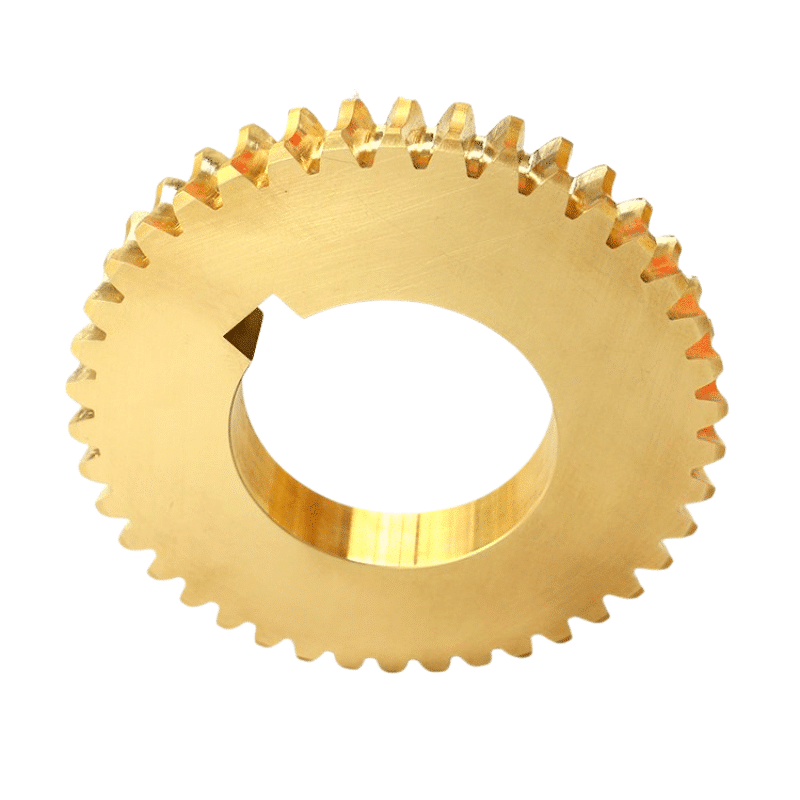
Machining Copper Gears Parts
specializing in CuAl11Ni Bronze Bushing
Copper gears find extensive use in industries where reliability and efficiency are paramount. The process of machining copper gears involves precise techniques to create gear teeth with accurate profiles, ensuring seamless transmission of power and motion.
When selecting custom bronze alloy materials for worm gear bushes, it is essential to consider the specific requirements of the application, such as load conditions, environmental factors, and operational temperatures. By choosing the right custom bronze alloy, engineers can ensure that their worm gear systems deliver optimum performance and have extended service lives in diverse industrial settings.
If you are considering manufacturing a worm wheel or related components, CuAl11Ni is an excellent material choice due to its high strength, corrosion resistance, and suitability for heavy-duty applications.
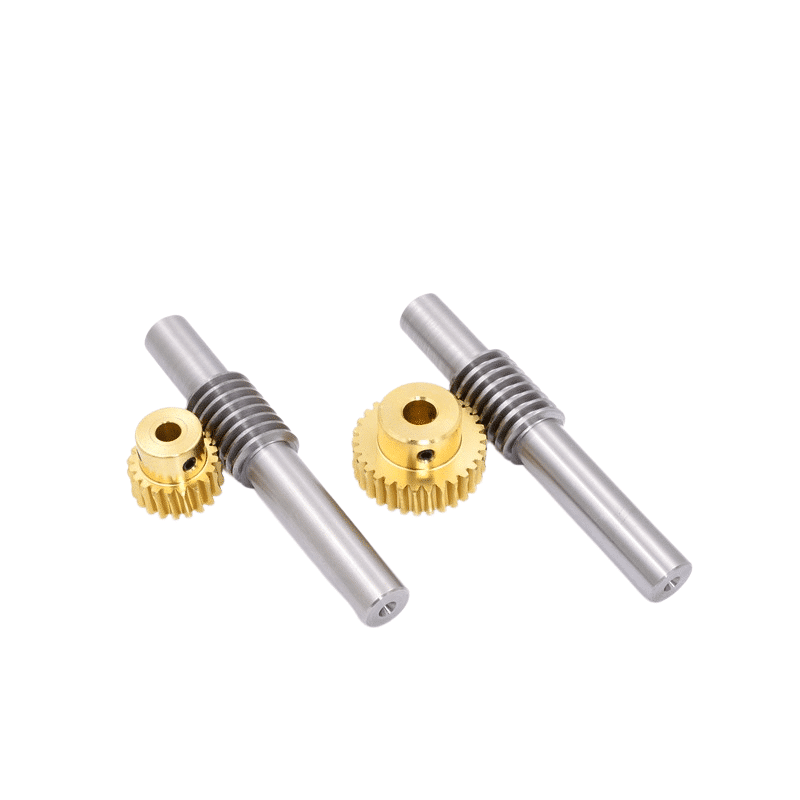
Custom bronze alloy materials
Custom bronze alloy materials offer a perfect combination of wear resistance, load-bearing capacity, and self-lubricating properties, making them an excellent choice for manufacturing worm gear bushes. With their ability to withstand heavy loads, resist wear, and operate smoothly with minimal maintenance, custom bronze alloy worm gear bushes play a crucial role in ensuring the efficiency and reliability of various industrial applications.
Worm gear systems are critical components in various industrial applications, providing efficient power transmission and motion control. To ensure optimal performance and longevity, selecting the right material for worm gear bushes is crucial. Bronze alloys, renowned for their excellent mechanical properties and wear resistance, are often the preferred choice for manufacturing worm gear bushes. In this blog post, we will explore the advantages of using custom bronze alloy materials for worm gear bushes and their applications in different industries.
CNC High Precision Machining, Customized Bronze BushFor All Your Industrial Needs
Machining bronze Gears with Precision: A Guide to Bronze b earring
CNC High Precision Machining – Copper Gears: A Guide to Material Selection and Processing
Copper gears are commonly used mechanical transmission components known for their high torque and speed capabilities. The machining of copper gears requires attention to various details and techniques to ensure optimal performance. Surface treatments can enhance their hardness and wear resistance, making them suitable for demanding mechanical transmission systems. Let’s explore the key aspects of machining copper gears, including material selection and processing techniques.
Material Selection for Copper Gears
Copper gears are typically made from copper alloys, and two common grades are H59 and H62. H59 copper exhibits high strength, good corrosion resistance, excellent toughness, and ease of machining. On the other hand, H62 copper boasts outstanding electrical and thermal conductivity, as well as excellent wear resistance. The choice between H59 and H62 depends on the specific application requirements and the properties needed from the copper gear.
Machining Techniques for Copper Gears
To achieve high precision and quality, the machining of copper gears requires specialized equipment such as CNC lathes, milling machines, and grinders. During the machining process, it is crucial to avoid excessive heat and vibration to prevent unnecessary damage to the copper gears. Proper lubrication and cooling are essential to ensure the quality and efficiency of the machining process.
Surface Treatment for Copper Gears
To improve the surface hardness and wear resistance of copper gears, surface treatments like coatings or plating can be applied. One common surface treatment method is spray coating, which creates a protective layer on the gear surface. The choice of surface treatment depends on the specific application and the desired properties of the copper gears.
Applications of Copper Gears
Copper gears find widespread use in mechanical transmission systems that require high torque and speed, such as in automobiles, machine tools, and marine vessels. They play a crucial role in efficiently transferring power and motion in these applications.
Conclusion
Copper gears are essential components in various mechanical transmission systems, known for their high torque and speed capabilities. Choosing the right copper alloy, such as H59 or H62, is crucial to meet specific application requirements. Precision machining techniques, with attention to proper lubrication and cooling, ensure the quality and durability of copper gears. Surface treatments further enhance their properties, making them suitable for demanding industrial applications.
If you require high-quality copper gears manufactured through CNC high precision machining, our company offers a range of mechanical parts, from simple to complex, with a tolerance of +/-0.005mm. Our skilled technicians and advanced equipment guarantee top-notch products. Additionally, we provide surface treatment services after CNC machining to meet your specific needs. Please feel free to contact us for a quotation and discover the advantages of our integrity machining service and extensive manufacturing experience.
The tolerances of a five-axis machining center refer to the allowable deviation from the specified dimensions during the machining process. These tolerances play a crucial role in determining the precision and accuracy of the machined parts. The tolerance levels in a five-axis machining center can vary depending on several factors, including the complexity of the part, the material being machined, and the capabilities of the machine itself.
In general, five-axis machining centers are capable of achieving tight tolerances, often in the range of a few thousandths of an inch (0.001 inches or 0.0254 mm) or even less. Some high-end machines and advanced setups can achieve even tighter tolerances, reaching sub-micron levels (less than 0.001 mm).
It is essential to understand that achieving tighter tolerances requires careful consideration of various factors, including machine calibration, tool selection, cutting parameters, and material properties. Additionally, the complexity of the part’s geometry and the number of axes involved can influence the achievable tolerance levels.
When working with a five-axis machining center, it is crucial to communicate the required tolerances clearly with the machine operator and consider the specific requirements of the part’s application. This ensures that the final machined parts meet the desired precision and functionality standards.
Ultimately, the capabilities of the specific five-axis machining center, along with the expertise of the operators and the machining processes employed, play a significant role in determining the achievable tolerances. Working with experienced and skilled machining professionals and employing state-of-the-art equipment are essential for consistently achieving tight tolerances in complex five-axis machining operations.
Five-Axis Machining Center: Advancing Precision and Versatility in Manufacturing
Introduction
In the realm of advanced manufacturing, the quest for higher precision, increased efficiency, and enhanced versatility has led to the development of cutting-edge machining technologies. One such innovation is the five-axis machining center, a powerhouse of engineering prowess that has revolutionized the way complex parts and components are manufactured. In this blog post, we will explore the key features, benefits, and applications of the five-axis machining center, shedding light on its significance in modern industrial processes.
What is a Five-Axis Machining Center?
A five-axis machining center is a computer numerical control (CNC) machine that utilizes five axes of motion to perform precision machining operations. Unlike conventional machining centers that typically move the workpiece along three linear axes (X, Y, and Z), a five-axis machining center adds two additional rotary axes (A and B) to provide unparalleled freedom of movement and machining capability.
Key Features and Advantages
- Multi-Axis Movement: The primary advantage of a five-axis machining center lies in its ability to move the cutting tool and workpiece along multiple axes simultaneously. This freedom enables machining complex geometries and contours without the need for repositioning the workpiece, reducing setup time and increasing overall efficiency.
- Improved Precision: The five-axis setup allows for continuous tool contact with the workpiece from multiple angles, resulting in smoother surface finishes and greater accuracy, particularly in hard-to-reach areas.
- Reduced Setups: With the ability to access multiple sides of the workpiece in a single clamping, the need for multiple setups is minimized. This reduces errors and ensures consistent part quality.
- Versatility: Five-axis machining centers can handle a wide range of parts, from simple components to intricate, highly complex designs. This versatility makes them suitable for various industries, including aerospace, automotive, medical, and defense.
- Enhanced Productivity: By reducing the number of operations and setups required, five-axis machining centers significantly improve productivity, making them indispensable in high-volume production environments.
Applications of Five-Axis Machining Centers
- Aerospace: Five-axis machining centers are extensively used in the aerospace industry to produce critical components such as turbine blades, engine housings, and complex structural parts, which demand both precision and lightweight design.
- Automotive: In the automotive sector, five-axis machining centers manufacture engine blocks, cylinder heads, and mold tooling, allowing for precise machining of intricate features and optimized part performance.
- Medical: The medical industry benefits from five-axis machining centers for producing surgical instruments, orthopedic implants, and intricate medical device components with high precision and biocompatible materials.
- Mold and Die Making: Five-axis machining centers excel in mold and die making, enabling the production of complex molds and dies with minimal manual finishing, thus reducing lead times.
Conclusion
The advent of five-axis machining centers has undoubtedly transformed the manufacturing landscape, enabling engineers and designers to realize their boldest and most innovative ideas with unprecedented precision and efficiency. By unlocking the power of multi-axis movement, these advanced machining centers have become indispensable tools in various industries, propelling technology and manufacturing capabilities to new heights.
As the demand for intricate, high-quality components continues to grow, the five-axis machining center stands ready to meet the challenges of modern manufacturing, driving progress and ensuring that the products of tomorrow are built with unparalleled precision and versatility.
Six-Axis Machining Centers: Versatile Solutions for Complex Component Manufacturing
Introduction
Six-axis machining centers are the pinnacle of advanced manufacturing technology, offering unparalleled versatility and precision in the production of complex components. With the ability to move the cutting tool along six axes of motion, these CNC machines have revolutionized the way intricate parts are manufactured. In this article, we will explore the types of components that are typically produced using six-axis machining centers and understand why they are the preferred choice for various industries.
Types of Components Produced by Six-Axis Machining Centers
Aerospace Components: Six-axis machining centers are extensively used in the aerospace industry to produce critical components like turbine blades, impellers, and structural parts. The complex contours and aerodynamic shapes of these components demand the high precision and multi-axis capabilities offered by six-axis machines.
Medical Implants and Prosthetics: The medical industry relies on six-axis machining centers to manufacture custom implants and prosthetics with intricate geometries. These machines can produce patient-specific implants, ensuring a perfect fit and optimum functionality.
Automotive Engine Components: In the automotive sector, six-axis machining centers are employed to produce engine blocks, cylinder heads, and crankshafts. These components require precise machining of complex features, and the six-axis capability enables efficient production.
Artistic Sculptures and Molds: Six-axis machining centers are also utilized in the art and design industry to create intricate sculptures and molds. The machines’ ability to precisely replicate 3D models allows artists to bring their creative visions to life.
Turbomachinery: In power generation and turbomachinery industries, six-axis machining centers are instrumental in manufacturing components like turbine rotors, compressor blades, and stator vanes. These components require precise machining to ensure optimal performance and efficiency.
Defense and Firearms Components: In the defense sector, six-axis machining centers are used to manufacture firearms components, such as receivers, barrels, and bolt carriers. The machines’ versatility allows for complex machining processes in a single setup.
Advantages of Six-Axis Machining Centers
Multi-Axis Flexibility: The primary advantage of six-axis machining centers is their ability to move the cutting tool along six axes, providing unmatched flexibility in machining complex shapes and contours.
Increased Precision: Six-axis machines can access hard-to-reach areas with ease, ensuring precise machining and smoother surface finishes.
Reduction in Setup Time: With the capability to perform multiple machining operations in a single setup, six-axis machining centers reduce the need for repositioning the workpiece, leading to a significant reduction in setup time and increased productivity.
Improved Tool Life: The ability to approach the workpiece from different angles results in more even tool wear, extending tool life and reducing tooling costs.
Conclusion
Six-axis machining centers have become indispensable tools in the manufacturing industry, enabling the production of complex and intricate components with unmatched precision and efficiency. From aerospace to medical, automotive to artistic applications, these versatile machines cater to a diverse range of industries and offer solutions for the most challenging machining tasks.
As technology continues to advance, six-axis machining centers will play a pivotal role in shaping the future of manufacturing, allowing engineers and designers to push the boundaries of what is possible and bring their innovative ideas to reality. With their multi-axis flexibility and precision, six-axis machining centers will continue to be at the forefront of advanced manufacturing, driving progress and propelling industries to new heights.
Here’s an overview of the key steps in the copper gear machining process:
- Material Selection: Choosing the right copper alloy is essential to achieve the desired gear properties. Different copper alloys offer varying levels of strength, thermal conductivity, and corrosion resistance, enabling engineers to tailor gears to specific applications.
- Gear Hobbing: Gear hobbing is the most common method for machining copper gears. It involves using a specialized cutting tool called a hob, which rotates and cuts into the copper workpiece to form the gear teeth. This process ensures precise tooth profiles and dimensional accuracy.
- Gear Shaping: Gear shaping is an alternative process to hobbing, especially for gears with unique tooth profiles. It involves using a gear-shaped cutter to progressively shape the gear teeth on the copper workpiece.
- Finishing and Inspection: After the initial machining, the copper gears undergo finishing operations, such as grinding and honing, to ensure smooth tooth surfaces and eliminate any imperfections. Rigorous quality inspection guarantees that the gears meet the required specifications.
Benefits of Copper Gears
- High Thermal Conductivity: Copper’s exceptional thermal conductivity allows gears to dissipate heat efficiently, reducing the risk of overheating and wear.
- Corrosion Resistance: Copper gears are resistant to corrosion, making them suitable for applications in challenging environments or exposure to moisture.
- Low Friction: Copper’s low coefficient of friction results in reduced wear and frictional losses, contributing to the gear’s longevity and overall efficiency.
Machining Worm Gear Bushes
Worm gear bushes are essential components in worm gear sets, providing support and reducing friction between the worm and the mating gear. Machining worm gear bushes requires precision to ensure proper engagement and smooth operation. Here are the primary steps involved in machining copper worm gear bushes:
- Material Selection: Similar to machining gears, choosing the appropriate copper alloy is crucial for worm gear bushes. The material should possess high wear resistance and a low coefficient of friction.
- Turning and Boring: The machining process begins with turning and boring the copper workpiece to achieve the required outer and inner diameters, as well as the desired length.
- Grooving and Threading: Specific worm gear bushes require grooves or threads for lubrication or secure fitting within the assembly. This step adds these essential features to the bush.
- Surface Treatment: Depending on the application, the copper worm gear bush may undergo surface treatments like heat treatment or coating to enhance its properties further.
Benefits of Copper Worm Gear Bushes
- Self-Lubricating: Copper worm gear bushes possess inherent lubricating properties, reducing the need for external lubrication and minimizing maintenance requirements.
- Wear Resistance: Copper’s wear-resistant properties ensure that worm gear bushes withstand heavy loads and continuous operation without premature wear.
Applications of Copper Gears and Worm Gear Bushes
Copper gears and worm gear bushes find applications in various industries, including:
- Automotive: Copper gears are used in automotive transmissions, steering systems, and engine components, while worm gear bushes are essential in steering boxes and transmissions.
- Machinery: Copper gears and worm gear bushes are employed in industrial machinery, robotics, and precision equipment due to their reliability and efficiency.
- Electronics: Copper gears are utilized in various electronic devices, such as printers, copiers, and scanners, where precision and low friction are crucial.
Machining copper gears and worm gear bushes requires a meticulous approach to ensure the highest quality and performance. As versatile materials, copper gears and worm gear bushes play a vital role in transmitting power and motion efficiently across a wide range of industries. With their remarkable properties like high thermal conductivity, corrosion resistance, and self-lubrication, copper gears and worm gear bushes continue to be indispensable components in the world of mechanical engineering.
C3604 bronze, also known as “Free-Cutting Brass,” is a type of brass alloy. It is a widely used material in engineering and manufacturing applications due to its excellent machinability and desirable mechanical properties.
C3604 bronze is primarily composed of copper (Cu) and zinc (Zn), with small amounts of other elements, including lead (Pb) and a small percentage of impurities. The specific composition of C3604 bronze typically consists of approximately 60-63% copper and 35-38% zinc, with traces of lead and other elements.
Key Properties of C3604 Bronze:
- Machinability: C3604 bronze is highly valued for its excellent machinability, which means it can be easily shaped and cut into various parts and components using machining processes such as turning, milling, and drilling.
- Corrosion Resistance: This bronze alloy offers good corrosion resistance, making it suitable for use in environments where protection against moisture and oxidation is essential.
- Electrical Conductivity: C3604 bronze exhibits reasonably high electrical conductivity, making it suitable for electrical connectors and components.
- Wear Resistance: The addition of lead in the alloy enhances its wear resistance, making C3604 bronze suitable for applications involving sliding and contact surfaces.
- Low Friction: The lead content in C3604 bronze contributes to its low coefficient of friction, reducing frictional losses in moving parts.
Applications of C3604 Bronze:
C3604 bronze finds applications in various industries, including:
- Electrical and Electronics: It is used in electrical connectors, terminals, and other electrical components due to its electrical conductivity.
- Plumbing and Fittings: C3604 bronze is commonly used in plumbing fittings, valves, and couplings due to its corrosion resistance and ease of machining.
- Automotive: It is utilized in automotive parts, such as fittings, connectors, and bushings, thanks to its excellent machinability and wear resistance.
- Industrial Machinery: C3604 bronze is employed in various mechanical parts, including gears, bearings, and bushings, due to its machinability and wear resistance.
- Fasteners: The alloy’s excellent machinability makes it suitable for producing fasteners, screws, and nuts.
C3604 bronze is a versatile material appreciated for its combination of machinability, corrosion resistance, electrical conductivity, and wear resistance. It has become a popular choice in many industries where precision machining and reliable performance are essential.