Bearing Bronze Alloys: Characteristics and Selection Guide, CNC machining
Bearing Bronze Solutions – Tailored for Efficiency & Strength
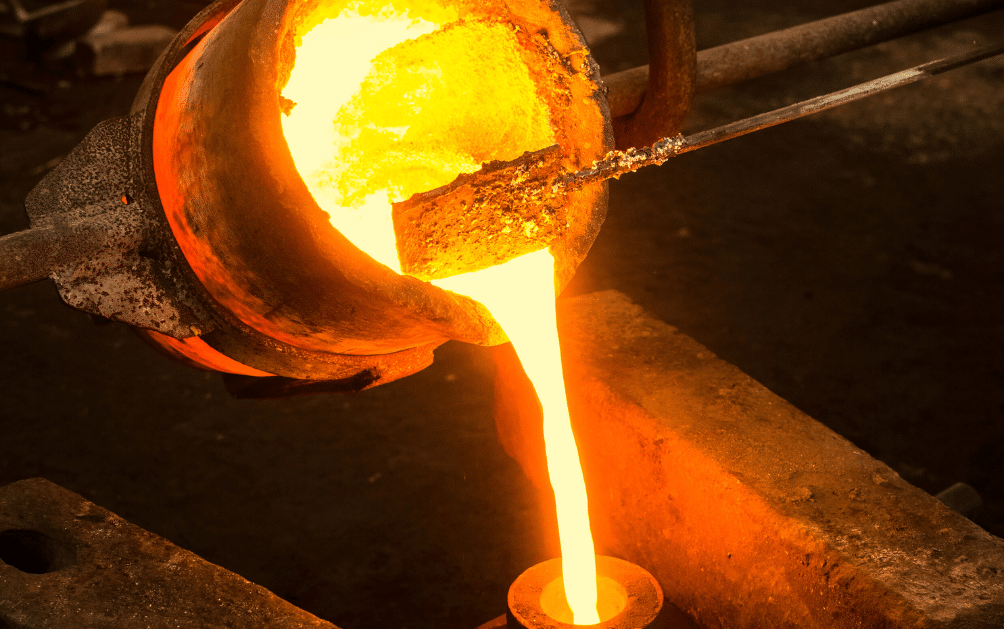
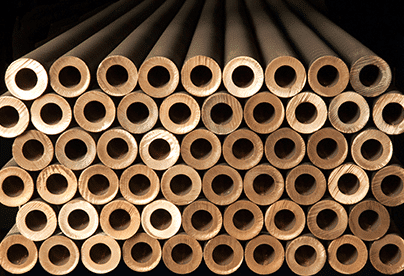
What is Bearing Brass? Oil Free Bushings / Plain Bushings

Special Brass: The Composition and Properties
Self-Lubricating Brass Features
Maintenance and Lubrication, Brass Bearing
Bearing brass, Self lubricating Brass Bushing, Plain bearing bushes with flange / brass / solid lubricant
Bearing brass is renowned for its strength, self-lubricating properties, and machinability, making it ideal for high-durability, low-maintenance components. It is essential in automotive, aerospace, and industrial machinery for enhancing system performance and reliability. Proper maintenance and machining knowledge ensure optimal performance of bearing brass components throughout their lifespan. Made from an alloy of copper and zinc, with variations for specific properties, these bushes meet diverse mechanical needs. We are ready to service your die component requirements. Contact us now for custom brass bearing components!
Machining Bearing Brass: Milling, Drilling, Grinding; Bronze Bushing and Bearing Material – Sleeve & Flange and More.
Machining bearing brass is notably different from working with other metals due to its softness and ductility. Here’s how bearing brass interacts with different machining processes:
Milling: When milling bearing brass, sharp, polished tools are essential to prevent the metal from sticking to the cutter. A higher cutting speed and a non-water soluble cutting fluid can result in smoother finishes and precise cuts.
Drilling: Similar to milling, sharp drills and appropriate lubrication (preferably oil-based) help maintain accuracy and surface integrity during the drilling process. Gradual feed rates and regular drill bit withdrawal are effective in removing chips and preventing clogging.
Grinding: Grinding bearing brass can be challenging due to its soft nature. Using a grinding wheel with a fine grit and low feed rates helps minimize heat buildup and prevents the metal from deforming.
Oil Free Bushings / Plain Bushings, Tolerance and Fit Considerations for Cast Bronze Bushings
The brass bushings are engineered for optimal performance, providing strength, as well as wear and corrosion resistance. Bronze bushings are vital in various mechanical assemblies, offering durability and efficiency when installed within the correct tolerance ranges. Installing a bronze bushing narrows its bore from an F7 to an H7 tolerance range, influenced by several factors:
– H7 Tolerance for Housing Bore: The housing bore must meet H7 tolerance standards to ensure a precise fit, avoiding overly tight or loose fitting.
– Adequate Housing Wall Thickness: The housing needs sufficient wall thickness to support the bushing without deforming under stress, maintaining the assembly’s integrity.
– Optimal Socket Wall Strength: Ensuring robust socket wall strength prevents structural weaknesses, enhancing the bushing’s durability and longevity.
Recommended tolerance fields vary by application based on counterpart requirements.
Flanged brass plain bearing bushes with solid lubricant provide excellent performance under high load and low-speed conditions. Shaft
- d8: For high-load applications
- e7: For low-load applications
- f7: For high accuracy
- g6: For high accuracy during intermittent operation
h6 Tolerance: Ideal for applications demanding top precision, like cutting tools and mold construction, h6 tolerance ensures a tight fit, reducing play and increasing accuracy.
f7 and e7 Tolerances: These are suggested for high accuracy in general engineering, offering a balance between a tight fit and easy assembly, suitable for diverse tasks.
Applying these tolerances is vital for optimizing the performance and reliability of bronze bushings in mechanical assemblies. By selecting the right tolerance fields and ensuring the housing can accommodate them, engineers can greatly enhance the effectiveness of their designs.
High-tension brass bushes and High strength brass bearing, The Future of Bearing Brass in Engineering and Design
About us
Custom Parts Services and Prototyping!
Special Bronze Alloys And Aluminium Bronze Bearing, Search Our Material Alloy
Bearing brass Plates and Angle Strips: Precision and Clearance Specifications
Bearing brass plates and angle strips are customized for specific applications and accuracy, with thicknesses usually between 0.02 mm and 0.15 mm. These components are engineered for precise clearances, enabling smooth mechanical operation and alignment. Bronze guide slides typically maintain a 0.05 mm lateral clearance for free movement without excessive play, ensuring accurate and stable performance. A 0.1 mm vertical clearance is also common to accommodate vertical movements or potential thermal expansion. These specifications are vital for the optimal performance of bronze components in engineering and manufacturing, allowing precise fitting and operational efficiency.
Exploring the Versatility of Self-Lubricating Spherical Brass Bearings
Introduction
In the realm of mechanical engineering and industrial applications, the choice of bearing material plays a critical role in ensuring the longevity and efficiency of machinery. Among the myriad of options available, self-lubricating spherical brass bearings stand out as a versatile and reliable choice. This blog post delves into the unique features and benefits of these bearings, highlighting why they are an excellent addition to various mechanical systems.
What are Self-Lubricating Spherical Brass Bearings?
Self-lubricating spherical brass bearings are specialized components designed to reduce friction and wear in machinery without the need for external lubrication. These bearings consist of a spherical inner component that fits snugly into a brass outer casing. The brass material is infused with lubricants, allowing for smooth and maintenance-free operation.
Key Features and Benefits
1. Self-Lubricating Properties
One of the standout features of these bearings is their self-lubricating capability. The brass casing is embedded with solid lubricants, which are gradually released during operation. This ensures continuous lubrication, reducing the need for regular maintenance and re-lubrication schedules.
2. Durability and Longevity
Brass is known for its excellent wear resistance and durability. When combined with self-lubricating properties, these bearings can withstand high levels of stress and friction, making them ideal for heavy-duty applications. The inherent strength of brass also ensures that the bearings maintain their structural integrity over extended periods, even in demanding environments.
3. Versatility in Applications
Self-lubricating spherical brass bearings are incredibly versatile and can be used in a wide range of applications. They are commonly found in automotive components, industrial machinery, aerospace, and even in household appliances. Their ability to operate effectively in both high and low-load conditions makes them a go-to choice for many engineers and designers.
4. Corrosion Resistance
Brass has natural corrosion-resistant properties, which are further enhanced in self-lubricating bearings. This makes them suitable for use in environments where exposure to moisture and chemicals is a concern. The bearings can operate efficiently without the risk of rust or corrosion, ensuring the longevity of the machinery in which they are installed.
5. Cost-Effective Solution
While the initial investment in self-lubricating spherical brass bearings may be higher than traditional bearings, the long-term benefits far outweigh the costs. The reduced need for maintenance, coupled with the extended lifespan of the bearings, results in significant cost savings over time. Additionally, the improved efficiency of machinery due to reduced friction can lead to lower energy consumption and operational costs.
Applications of Self-Lubricating Spherical Brass Bearings
Self-lubricating spherical brass bearings are utilized in various industries due to their unique properties. Here are a few notable applications:
- Automotive Industry: Used in steering mechanisms, suspension systems, and other critical components to enhance performance and reduce maintenance.
- Industrial Machinery: Essential for the smooth operation of conveyor systems, pumps, and compressors.
- Aerospace: Employed in aircraft components where reliability and durability are paramount.
- Marine Equipment: Ideal for use in marine environments due to their corrosion resistance.
- Home Appliances: Found in washing machines, fans, and other household devices to ensure quiet and efficient operation.
Conclusion
Self-lubricating spherical brass bearings are a remarkable innovation in the field of mechanical engineering. Their ability to provide continuous lubrication, combined with the durability and corrosion resistance of brass, makes them an invaluable component in various applications. By choosing these bearings, industries can achieve greater efficiency, reduced maintenance costs, and enhanced performance of their machinery. Whether in automotive, industrial, aerospace, or household applications, self-lubricating spherical brass bearings are a testament to the advancements in bearing technology.
By incorporating these bearings into your machinery, you can ensure a smoother, more efficient, and longer-lasting operation. Explore the possibilities and benefits of self-lubricating spherical brass bearings for your next project.
4o
Maintenance Free, Bearing Bronze Components, brass Bearings
In hac habitasse platea dictumst nam quam nunc, blandit vel, luctus pulvinar.